涂料技术
研究硅烷偶联剂改性水性聚氨酯胶黏剂
2.4.2耐水性
采用内乳化方法制得的水性聚氨酯因为在分子结构上引入了亲水性基团,因此,胶膜的吸水性往往都很强,这是水性聚氨酯的最大的缺点之一。而在聚氨酯中引入可以在胶结过程中发生交联反应的硅烷偶联剂是提高胶膜耐水性的有效方法,因此交联度的大小直接决定胶膜的耐水性能。实验中研究了不同的硅烷偶联剂用量对胶膜的耐水性的影响,结果如图4所示。
采用内乳化方法制得的水性聚氨酯因为在分子结构上引入了亲水性基团,因此,胶膜的吸水性往往都很强,这是水性聚氨酯的最大的缺点之一。而在聚氨酯中引入可以在胶结过程中发生交联反应的硅烷偶联剂是提高胶膜耐水性的有效方法,因此交联度的大小直接决定胶膜的耐水性能。实验中研究了不同的硅烷偶联剂用量对胶膜的耐水性的影响,结果如图4所示。
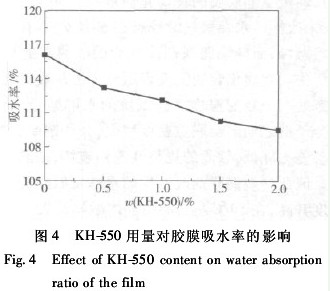
从图4可以看出,随着硅烷偶联剂用量的增加,胶膜的吸水率逐渐降低,耐水性能增强。本文所使用的硅烷偶联剂是KH-550,KH-550上的伯氨与聚氨酯预聚体中的—NCO端基反应活性很高,所以很容易将KH-550引入到聚氨酯的主链上。胶黏剂涂覆于薄膜基材表面后,随着水的挥发KH-550上的硅氧烷水解缩合反应加速,形成更多Si—O—Si的交联结构。研究发现,为了控制在乳液贮存过程中硅烷偶联剂的水解缩合反应速率,将乳液pH值调控在7左右,可以减缓该反应的发生。当胶黏剂涂覆于薄膜表面时,要经过70~80℃的烘烤,较高的温度会促使水解缩合反应的发生。从而保证了水性聚氨酯乳液在室温下较稳定,而在使用时又会快速的水解缩合产生交联结构。
2.4.3玻璃化转变温度Tg
对硅烷偶联剂改性的水性聚氨酯胶膜与未改性水性聚氨酯胶膜的玻璃化转变温度进行了测试,结果如图5所示。
2.4.3玻璃化转变温度Tg
对硅烷偶联剂改性的水性聚氨酯胶膜与未改性水性聚氨酯胶膜的玻璃化转变温度进行了测试,结果如图5所示。

从图5中可以看出,未加硅烷偶联剂的水性聚氨酯胶膜的玻璃化温度在-49℃,而加入硅烷改性的水性聚氨酯胶膜的玻璃化温度在-30℃左右;同时,未改性的水性聚氨酯胶膜在50℃左右有一个结晶熔融峰,而硅烷偶联剂改性后的胶膜在此处熔融峰消失。玻璃化转变温度表示分子链从玻璃态到高弹态的一个转变温度。硅氧烷的水解缩合,使聚氨酯分子链之间的交联点密度增大,分子链受到约束,运动能力降低,软段的规整性遭到破坏,结晶能力降低。因此硅烷偶联剂改性后的水性聚氨酯的玻璃化温度升高,在50℃左右的结晶熔融峰消失。
2.4.4粘接性能
硅烷偶联剂中的烷氧基脱水生成硅羟基,硅羟基既可以和聚氨酯分子链上的羟基进行缩合反应,增强了胶膜的内聚力。由于经过电晕处理后的薄膜表面有很多羟基、羧基等活性基团,硅羟基还可以与薄膜表面上的活性基团进行反应,增强了胶膜与薄膜的界面粘接力。研究了硅烷偶联剂含量对PET/CPP复合薄膜的粘接强度的影响,结果如图6所示。
2.4.4粘接性能
硅烷偶联剂中的烷氧基脱水生成硅羟基,硅羟基既可以和聚氨酯分子链上的羟基进行缩合反应,增强了胶膜的内聚力。由于经过电晕处理后的薄膜表面有很多羟基、羧基等活性基团,硅羟基还可以与薄膜表面上的活性基团进行反应,增强了胶膜与薄膜的界面粘接力。研究了硅烷偶联剂含量对PET/CPP复合薄膜的粘接强度的影响,结果如图6所示。
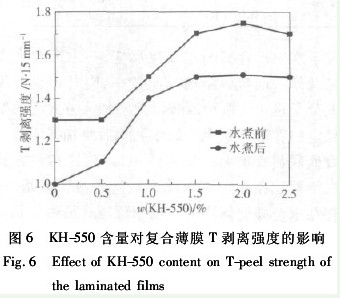
从图6看出,硅烷偶联剂确实起到了增强界面之间粘接强度的作用。随着硅烷偶联剂用量的增加,复合薄膜的粘接强度逐渐增强,耐100℃水煮性能也随之增大;但是当硅烷偶联剂用量大于预聚体质量的1.5%时,胶黏剂的粘接强度和耐100℃水煮性增加趋于平缓。原因是:随着偶联剂用量的增加,分子链之间的交联程度增大;硅烷偶联剂一端与基材作用,另一端与胶层作用,在胶层与基材之间形成化学键,从而增强胶层与基材的粘接力。过量的硅烷偶联剂不能再接入到大分子链上,就无法起到连接基材与胶层的作用,因此,当KH-550用量大于1.5%时,粘接强度不再继续增加。
3结论
KH-550的引入改善了水性聚氨酯胶膜的耐水性和粘接性。当KH-550用量为预聚体质量分数的1.5%时,乳液稳定性良好,胶膜耐水性有所提高,胶粘剂的粘接性能达到最佳,复合薄膜PET/CPP的T剥离强度由未改性前的1.3N/15mm增大至1.7N/15mm;经过100℃水煮后,粘接强度并未降低,反而由1.0N/15mm增加到1.5N/15mm。
3结论
KH-550的引入改善了水性聚氨酯胶膜的耐水性和粘接性。当KH-550用量为预聚体质量分数的1.5%时,乳液稳定性良好,胶膜耐水性有所提高,胶粘剂的粘接性能达到最佳,复合薄膜PET/CPP的T剥离强度由未改性前的1.3N/15mm增大至1.7N/15mm;经过100℃水煮后,粘接强度并未降低,反而由1.0N/15mm增加到1.5N/15mm。
相关文章
发布评论