汽车涂料
研究汽车车身阴极电泳涂膜质量控制
控制汽车车身阴极电泳涂膜质量主要有3个方面:改善磷化膜与阴极电泳漆膜的配套性;监控漆液工艺参数;严格检测涂膜性能。提出漆液和涂膜的检测方法。
1引言
磷化是汽车车身阴极电泳前处理中最重要的一道工序,它可以使车体表面洁净,并在车体内外表面形成一层均匀的磷化膜,以保证涂膜具有良好的防腐蚀性能和附着力。磷化膜与阴极电泳漆膜配套性是否良好,是影响整体涂膜性能的关键所在。为此,阴极电泳涂装对磷化膜提出基本要求:①磷化膜外观好,均匀致密;②磷化膜的膜重小(2~3g/m2);③磷化膜的晶粒尺寸小(10μm以下);④磷化膜的P比高(大于85%);⑤涂膜(磷化膜+涂层)耐冲击性好(杯突大于5mm);⑥涂膜附着力强(划圈法达到1级);⑦涂膜耐盐雾腐蚀性好(耐盐雾试验1000h,单边腐蚀宽度小于2mm)。
某汽车车身制造厂选择05-02-5磷化剂与WB821型灰色阴极电泳涂料配套使用,用于2条阴极电泳涂装自动线(连续式和间隙式),经多年批量生
产考验,工艺稳定,质量良好,涂膜耐中性盐雾试验达1200h,超过目标200h。有关本工艺的应用情况见文献[1]介绍。本文介绍车身涂膜质量控制问题。
2改善磷化膜与阴极电泳漆膜的配套性
2.1磷化膜与阴极电泳漆膜配套性不良的主要原因
⑴磷化过程中不易形成高P比的磷化膜。
⑵阴极电泳涂装过程中,往往产生磷化膜的溶解(反应式2H2O+2e→H2↑+2OH-,磷化膜与电泳漆界面的pH为12~13,膜层受到碱腐蚀,且溶解下来的PO43-对涂料的稳定性有危害),因而,导致磷化膜与阴极电泳漆膜配套性不良。
⑶涂膜附着力低、耐腐蚀性差。
2.2优化磷化剂与阴极电泳涂料性能的措施
⑴添加复合元素配制磷化剂。05-02-5磷化剂系低锌高锰镍多元素复配,可获得锌-锰-镍复合磷化膜(Zn30%+Fe5.8%+Mn4.2%+Ni5.8%),其特点:①膜层组织结构细腻紧密(粒状晶粒非常小),光洁无挂灰(磷化沉渣量约为3g/m2)。②膜层高P比(P比大于85%),耐碱性强(磷化膜溶出量为1.4%~5.0%)。正因为本磷化膜性能优良,决定了与阴极电泳涂料的配套性好,也是阴极电泳涂层耐盐雾性强的原因之一。
⑵运用特殊技术改性阴极电泳涂料。①引入新的季胺盐分散树脂,使槽液稳定性好;②以高效Sn类作催化剂,降低固化温度(180℃);③利用软/硬树脂匹配技术,使槽液泳透力高(达到20cm以上);④涂层厚(标准膜厚达到30μm以上);⑤添加特制丙烯酸树脂,使涂层具有很强的抗缩孔能力(抗燃油烘干室油污染的能力),避免涂层产生缩孔。同时耐候性也有明显地提高。⑥添加特种防锈颜料,使涂层的耐盐雾性由原来的800h提高到1000h以上。⑦调整涂料黏度,提高了边角覆盖能力。
本涂料不足之处是涂层抗粉化能力偏低(车身电泳涂层抗室外粉化能力仅1个月)。
3监控漆液工艺参数
3.1固体含量
用烘干称量法检测,称取2.0~2.5g电泳槽液,在120℃下烘烤1h,称量。

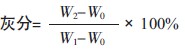
1引言
磷化是汽车车身阴极电泳前处理中最重要的一道工序,它可以使车体表面洁净,并在车体内外表面形成一层均匀的磷化膜,以保证涂膜具有良好的防腐蚀性能和附着力。磷化膜与阴极电泳漆膜配套性是否良好,是影响整体涂膜性能的关键所在。为此,阴极电泳涂装对磷化膜提出基本要求:①磷化膜外观好,均匀致密;②磷化膜的膜重小(2~3g/m2);③磷化膜的晶粒尺寸小(10μm以下);④磷化膜的P比高(大于85%);⑤涂膜(磷化膜+涂层)耐冲击性好(杯突大于5mm);⑥涂膜附着力强(划圈法达到1级);⑦涂膜耐盐雾腐蚀性好(耐盐雾试验1000h,单边腐蚀宽度小于2mm)。
某汽车车身制造厂选择05-02-5磷化剂与WB821型灰色阴极电泳涂料配套使用,用于2条阴极电泳涂装自动线(连续式和间隙式),经多年批量生
产考验,工艺稳定,质量良好,涂膜耐中性盐雾试验达1200h,超过目标200h。有关本工艺的应用情况见文献[1]介绍。本文介绍车身涂膜质量控制问题。
2改善磷化膜与阴极电泳漆膜的配套性
2.1磷化膜与阴极电泳漆膜配套性不良的主要原因
⑴磷化过程中不易形成高P比的磷化膜。
⑵阴极电泳涂装过程中,往往产生磷化膜的溶解(反应式2H2O+2e→H2↑+2OH-,磷化膜与电泳漆界面的pH为12~13,膜层受到碱腐蚀,且溶解下来的PO43-对涂料的稳定性有危害),因而,导致磷化膜与阴极电泳漆膜配套性不良。
⑶涂膜附着力低、耐腐蚀性差。
2.2优化磷化剂与阴极电泳涂料性能的措施
⑴添加复合元素配制磷化剂。05-02-5磷化剂系低锌高锰镍多元素复配,可获得锌-锰-镍复合磷化膜(Zn30%+Fe5.8%+Mn4.2%+Ni5.8%),其特点:①膜层组织结构细腻紧密(粒状晶粒非常小),光洁无挂灰(磷化沉渣量约为3g/m2)。②膜层高P比(P比大于85%),耐碱性强(磷化膜溶出量为1.4%~5.0%)。正因为本磷化膜性能优良,决定了与阴极电泳涂料的配套性好,也是阴极电泳涂层耐盐雾性强的原因之一。
⑵运用特殊技术改性阴极电泳涂料。①引入新的季胺盐分散树脂,使槽液稳定性好;②以高效Sn类作催化剂,降低固化温度(180℃);③利用软/硬树脂匹配技术,使槽液泳透力高(达到20cm以上);④涂层厚(标准膜厚达到30μm以上);⑤添加特制丙烯酸树脂,使涂层具有很强的抗缩孔能力(抗燃油烘干室油污染的能力),避免涂层产生缩孔。同时耐候性也有明显地提高。⑥添加特种防锈颜料,使涂层的耐盐雾性由原来的800h提高到1000h以上。⑦调整涂料黏度,提高了边角覆盖能力。
本涂料不足之处是涂层抗粉化能力偏低(车身电泳涂层抗室外粉化能力仅1个月)。
3监控漆液工艺参数
3.1固体含量
用烘干称量法检测,称取2.0~2.5g电泳槽液,在120℃下烘烤1h,称量。

上限为好)。固体含量过低,漆液稳定性差。
3.2灰分
用烘干称量法检测,准确称坩锅质量(W0)。称取2.5~3.0g电泳漆液置于坩锅,称量(W1),在120℃下烘烤1h,冷却后称量至恒量。样品放入马弗炉中,从200℃加热至800℃,恒温30min至恒量(W2),10d检测1次,要求灰分在18%~22%。
3.2灰分
用烘干称量法检测,准确称坩锅质量(W0)。称取2.5~3.0g电泳漆液置于坩锅,称量(W1),在120℃下烘烤1h,冷却后称量至恒量。样品放入马弗炉中,从200℃加热至800℃,恒温30min至恒量(W2),10d检测1次,要求灰分在18%~22%。
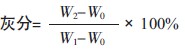
3.3pH
用酸度计检测,重复3次,取其平均值。一般测定温度为25℃,2d检测1次,要求pH为6.0~6.6。
3.4电导率
用电导率仪检测,重复3次,取其平均值。一般测定温度为25℃,2d检测1次,要求电导率在1000~1600μS/cm。槽液的电导率取决于固体含量的高低和杂质的多少。
3.5泳透率
采用钢管法检测,3个月检测1次(委托外部实验室),要求泳透率大于90%。并做试板重叠点焊电泳试验(点距50mm),要求点焊处全部电泳上漆,15d试验1次。
4严格检测涂膜性能
4.1物理性能
⑴外观。平整光滑,不允许存在缩孔、花纹、颗粒、橘皮等缺陷,对轻微缺陷在不影响面漆涂装和外观的前提下可视为合格。
⑵厚度(20~25μm)。用数字式覆层测厚仪检测。每天现场抽检2次,每次2台车身。
⑶光泽(60°)(40%~60%)。现场用便携式镜面光泽度计检测。15d检测1次,每次2台车身。
⑷附着力(0级)。用锐利的刀片在随车试板上(2块)划10组相互垂直交叉的透底的切割线,间距为1mm,贴透明胶带撕扯,目测漆膜的撕裂程度。2个月检测1次。
⑸铅笔硬度(≥1H)。现场用1H~3H铅笔检测,以目测检验漆膜划痕的深浅及明显程度。2个月检测1次,每次2台车身。
⑹抗冲击性(≥50cm)。用漆膜冲击试验器检测,以重锤的质量与其落于随车试片上面不引起漆膜破坏之最大高度的乘积表示。2个月检测1次。
4.2化学性能
⑴耐盐雾性(涂层厚度不小于20μm)。要求耐盐雾试验不小于1000h。经国家涂料质量监检中心检测耐盐雾试验1200h,漆膜划线处单向锈蚀0.9mm(国标不大于2mm)。制随车试板2块(200mm×150mm,下同),每年由涂料供应商委托外部实验室检测1次。
⑵抗粉化性。部分客户要求车身只涂电泳不涂面漆(因为在运输过程中有可能碰伤面漆),面漆则由客户自行施工。因此,车身电泳后,在室外需要放置几个月后才能发运。要求电泳涂层必须具有一定的抗粉化能力。制随车试板2块,悬挂室外曝晒,观察漆膜粉化变色情况。2个月检测1次,6个月为1周期。
⑶耐酸碱性。制随车试板各2块,分别浸泡于50g/LNaOH溶液中8h,要求漆膜外观无明显变化。6个月检测1次。
⑷耐汽油性。制随车试板2块,浸泡汽油48h,要求漆膜无明变色及失光。
4.3配套性
⑴与面漆配套。制随车试板2块,湿碰湿面漆2道,要求与面漆无不良反应。
⑵与原子灰配套。制随车试板2块,涂刮腻子后在140℃下烘20min,要求电泳涂层不随腻子脱落,满足客户要求。现场技术检验人员每隔5d检测1次。
这里所谈的并非是通常指的电泳层与原子灰附着力差,因为原子灰自干时,原子灰与电泳涂层附着力牢。如果固定其它条件不变,仅更换磷化剂,却发现电泳涂层与原子灰附着力良(无论原子灰层自干或烘烤)。可见还是因为磷化膜与电泳涂层配套性差而引起原子灰与电泳涂层附着不牢。这种现象很少引起人们的注意,一旦出现这种故障,往往误解为车身前处理不良(最好的前处理质量也无法消除这种故障)。实践表明,有些市售磷化剂确实与电泳涂料配套不良会引发此类故障。
用酸度计检测,重复3次,取其平均值。一般测定温度为25℃,2d检测1次,要求pH为6.0~6.6。
3.4电导率
用电导率仪检测,重复3次,取其平均值。一般测定温度为25℃,2d检测1次,要求电导率在1000~1600μS/cm。槽液的电导率取决于固体含量的高低和杂质的多少。
3.5泳透率
采用钢管法检测,3个月检测1次(委托外部实验室),要求泳透率大于90%。并做试板重叠点焊电泳试验(点距50mm),要求点焊处全部电泳上漆,15d试验1次。
4严格检测涂膜性能
4.1物理性能
⑴外观。平整光滑,不允许存在缩孔、花纹、颗粒、橘皮等缺陷,对轻微缺陷在不影响面漆涂装和外观的前提下可视为合格。
⑵厚度(20~25μm)。用数字式覆层测厚仪检测。每天现场抽检2次,每次2台车身。
⑶光泽(60°)(40%~60%)。现场用便携式镜面光泽度计检测。15d检测1次,每次2台车身。
⑷附着力(0级)。用锐利的刀片在随车试板上(2块)划10组相互垂直交叉的透底的切割线,间距为1mm,贴透明胶带撕扯,目测漆膜的撕裂程度。2个月检测1次。
⑸铅笔硬度(≥1H)。现场用1H~3H铅笔检测,以目测检验漆膜划痕的深浅及明显程度。2个月检测1次,每次2台车身。
⑹抗冲击性(≥50cm)。用漆膜冲击试验器检测,以重锤的质量与其落于随车试片上面不引起漆膜破坏之最大高度的乘积表示。2个月检测1次。
4.2化学性能
⑴耐盐雾性(涂层厚度不小于20μm)。要求耐盐雾试验不小于1000h。经国家涂料质量监检中心检测耐盐雾试验1200h,漆膜划线处单向锈蚀0.9mm(国标不大于2mm)。制随车试板2块(200mm×150mm,下同),每年由涂料供应商委托外部实验室检测1次。
⑵抗粉化性。部分客户要求车身只涂电泳不涂面漆(因为在运输过程中有可能碰伤面漆),面漆则由客户自行施工。因此,车身电泳后,在室外需要放置几个月后才能发运。要求电泳涂层必须具有一定的抗粉化能力。制随车试板2块,悬挂室外曝晒,观察漆膜粉化变色情况。2个月检测1次,6个月为1周期。
⑶耐酸碱性。制随车试板各2块,分别浸泡于50g/LNaOH溶液中8h,要求漆膜外观无明显变化。6个月检测1次。
⑷耐汽油性。制随车试板2块,浸泡汽油48h,要求漆膜无明变色及失光。
4.3配套性
⑴与面漆配套。制随车试板2块,湿碰湿面漆2道,要求与面漆无不良反应。
⑵与原子灰配套。制随车试板2块,涂刮腻子后在140℃下烘20min,要求电泳涂层不随腻子脱落,满足客户要求。现场技术检验人员每隔5d检测1次。
这里所谈的并非是通常指的电泳层与原子灰附着力差,因为原子灰自干时,原子灰与电泳涂层附着力牢。如果固定其它条件不变,仅更换磷化剂,却发现电泳涂层与原子灰附着力良(无论原子灰层自干或烘烤)。可见还是因为磷化膜与电泳涂层配套性差而引起原子灰与电泳涂层附着不牢。这种现象很少引起人们的注意,一旦出现这种故障,往往误解为车身前处理不良(最好的前处理质量也无法消除这种故障)。实践表明,有些市售磷化剂确实与电泳涂料配套不良会引发此类故障。
相关文章
发布评论