涂料技术
研究超薄型防火涂料的实验制备
水平因素表见表5,考虑基本配方I的实干时间较长(大约为60h)和初期干燥抗裂性好,适当地减少了丙二醇的用量,为0.7mL;根据涂料中有小气泡的现象.减少了NP-10用量,为4滴;增加了消泡剂的用量,为0.5mL。结果涂料的实干时间和小气泡现象都得到了改善,涂料的涂布性能和漆面的装饰效果同配方I。对正交试验表中的各配方作耐火性能测试,以耐火时间最长的配方为第一次优化最佳配方,为表11中的配方Ⅱ,其耐火时间为28min。在第一次优化配方Ⅱ的基础上,为了定出配方中这4个因素的更精确的用量,以第一次优化的最佳配方Ⅱ为基础,进行第二次优化(细化),设计的四因素三水平分别为(g):
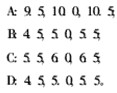
水平因素表见表6。
在漆膜表面不出现裂纹的情况下,继续减少丙二醇的用量,为0.5mL,同样对正交试验表中各配方涂板作耐火性能检测,测得配方中耐火时间最长为37min.该最佳配方为表10中的配方Ⅲ。对正交试验数据进行计算分析,结果A因素水平的最大值10.5g最好;B因素水平的中间值5.0g最好;C因素水平的两个较高值接近,C因素取6.5g较好;D因素的水平中间值5.5g最好。经优化后,耐火时间延长了16min,优化结果明显。
1.7单因素优化实验
在确定出优化配方的基础上,对基料、三聚氰胺、季戊四醇、这3种主要组分的用量对涂料耐火性能的影响进一步作了单因素考察,其他组分不变。实验步骤如上所述。
1.8涂料耐火时间检测[2]
防火涂料耐火时间的标准检测方法需要特殊的实验设备,除国家指定的检测中心外,一般实验室不具备这样的实验条件。对试验样品耐火时间的检测,采用的是自己设计的酒精喷灯燃烧法。
具体方法为:用酒精喷灯的火焰灼烧涂布涂料的木板,酒精喷灯上口距检测板垂直距离6.0cm,其稳定火焰最高温度可达到1000℃以上,该火焰温度及火焰冲击力与标准方法基本相符。它所存在的缺点是:喷灯火焰集中在一块小面积上,导致温度分布不均匀;火焰冲击力太大,涂层易被吹落。在测试时,调整好酒精喷灯上口与置于固定铁环上的测试板之间的距离,在固定铁环上放置好测试板,使其涂层朝下。然后点燃酒精喷灯,待其火焰稳定后,将火焰对准测试板的中央(注意不要让火焰从两侧窜到测试板的背面),此时开始计时,至检测终点(木版背面炭化并出现裂缝,上面看到火焰的时刻)所经历的时间为耐火时间。
2实验结论
2.1乳液合成实验结果讨论
2.1.1单体配比的选择
乳液中单体所占比例对乳液的黏度、附着力等性能以及反应时间和速度都有一定的影响,对不同单体配比所得乳液的性能的测试结果如表7,从表中可以看出,当单体所占比例为45%时,乳液各项性能良好,故最佳单体所占比例为45%。
在漆膜表面不出现裂纹的情况下,继续减少丙二醇的用量,为0.5mL,同样对正交试验表中各配方涂板作耐火性能检测,测得配方中耐火时间最长为37min.该最佳配方为表10中的配方Ⅲ。对正交试验数据进行计算分析,结果A因素水平的最大值10.5g最好;B因素水平的中间值5.0g最好;C因素水平的两个较高值接近,C因素取6.5g较好;D因素的水平中间值5.5g最好。经优化后,耐火时间延长了16min,优化结果明显。
1.7单因素优化实验
在确定出优化配方的基础上,对基料、三聚氰胺、季戊四醇、这3种主要组分的用量对涂料耐火性能的影响进一步作了单因素考察,其他组分不变。实验步骤如上所述。
1.8涂料耐火时间检测[2]
防火涂料耐火时间的标准检测方法需要特殊的实验设备,除国家指定的检测中心外,一般实验室不具备这样的实验条件。对试验样品耐火时间的检测,采用的是自己设计的酒精喷灯燃烧法。
具体方法为:用酒精喷灯的火焰灼烧涂布涂料的木板,酒精喷灯上口距检测板垂直距离6.0cm,其稳定火焰最高温度可达到1000℃以上,该火焰温度及火焰冲击力与标准方法基本相符。它所存在的缺点是:喷灯火焰集中在一块小面积上,导致温度分布不均匀;火焰冲击力太大,涂层易被吹落。在测试时,调整好酒精喷灯上口与置于固定铁环上的测试板之间的距离,在固定铁环上放置好测试板,使其涂层朝下。然后点燃酒精喷灯,待其火焰稳定后,将火焰对准测试板的中央(注意不要让火焰从两侧窜到测试板的背面),此时开始计时,至检测终点(木版背面炭化并出现裂缝,上面看到火焰的时刻)所经历的时间为耐火时间。
2实验结论
2.1乳液合成实验结果讨论
2.1.1单体配比的选择
乳液中单体所占比例对乳液的黏度、附着力等性能以及反应时间和速度都有一定的影响,对不同单体配比所得乳液的性能的测试结果如表7,从表中可以看出,当单体所占比例为45%时,乳液各项性能良好,故最佳单体所占比例为45%。
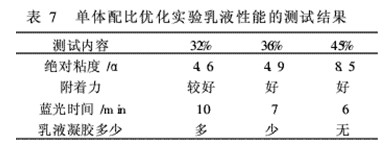
表7
2.1.2硬、软单体间比例的确定
本实验中硬单体是苯乙烯,能赋予聚合物良好的硬度、附着力、耐水性和抗污性;软单体是丙烯酸丁酯,能使乳液有良好的柔韧性。另外在实验中加入了甲基丙烯酸甲酯,可以提高乳液漆膜的附着力,以及丙烯酸,这样在丙烯酸酯上引入羧基,可是聚合物乳液有良好的稳定性和碱增稠性。从上一实验结果得到乳液制备的最佳单体比例为45%,对不同硬、软单体间比例所得乳液的性能的测试结果如表8,从表中可以看出,苯乙烯/丙烯酸丁酯=1/1时,是个较好的配比。
本实验中硬单体是苯乙烯,能赋予聚合物良好的硬度、附着力、耐水性和抗污性;软单体是丙烯酸丁酯,能使乳液有良好的柔韧性。另外在实验中加入了甲基丙烯酸甲酯,可以提高乳液漆膜的附着力,以及丙烯酸,这样在丙烯酸酯上引入羧基,可是聚合物乳液有良好的稳定性和碱增稠性。从上一实验结果得到乳液制备的最佳单体比例为45%,对不同硬、软单体间比例所得乳液的性能的测试结果如表8,从表中可以看出,苯乙烯/丙烯酸丁酯=1/1时,是个较好的配比。
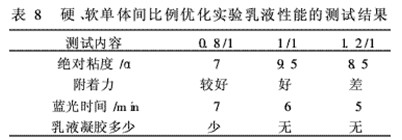
表8
2.1.3乳化剂含量的选择
目前使用的各种乳化剂的结构,都有一个共同点,即他们的分子中均含有2类性质截然不同的部分,亲水或疏油的极性基团与亲油或疏水的非极性基团。本实验采用复合型乳化剂:非离子乳化剂在水溶液中不会离解成例子,其效果与介质pH值无关,它会在聚合物表面形成吸附层,阻挡聚合物分子相互碰撞,从而提高聚合物粒子的分散未定性;阴离子形乳化剂十二烷基硫酸钠,水解生成阴离子基团的乳化剂,可使聚合物表面带负电荷,造成聚合物颗粒相斥降低粒径[3]。两种表面活性剂的混合物基本上是水不溶单体非常有效的乳化剂,改变两者的比例可以较好的控制乳液粘度。前人实验表明[1]:非离子乳化剂/阴离子乳化剂=4.0/1较为合适,对不同乳化剂含量所得乳液的性能的测试结果如表9。
目前使用的各种乳化剂的结构,都有一个共同点,即他们的分子中均含有2类性质截然不同的部分,亲水或疏油的极性基团与亲油或疏水的非极性基团。本实验采用复合型乳化剂:非离子乳化剂在水溶液中不会离解成例子,其效果与介质pH值无关,它会在聚合物表面形成吸附层,阻挡聚合物分子相互碰撞,从而提高聚合物粒子的分散未定性;阴离子形乳化剂十二烷基硫酸钠,水解生成阴离子基团的乳化剂,可使聚合物表面带负电荷,造成聚合物颗粒相斥降低粒径[3]。两种表面活性剂的混合物基本上是水不溶单体非常有效的乳化剂,改变两者的比例可以较好的控制乳液粘度。前人实验表明[1]:非离子乳化剂/阴离子乳化剂=4.0/1较为合适,对不同乳化剂含量所得乳液的性能的测试结果如表9。
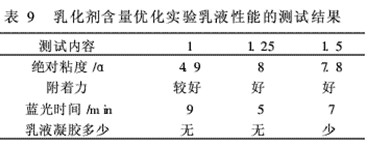
表9
从表中可以看出,乳化剂的含量为1.25%时,乳液黏度适中,在瓷砖背面附着力好,反应速度快、时间短、絮凝少。故确定乳化剂的含量为1.25%为最佳。
2.1.4引发剂的选择
本试验用过硫酸铵作引发剂,总含量为0.2%,中后期与单体同步滴加,滴加速度约为单体的1/4。实验反应温度控制在84~86℃时,有稳定的回流,并且有较快的反应速率。
2.1.5滴加速度
滴加速度过快,则乳液粒径大,稳定性差[4]。本实验中后期单体加入速度控制在1~3滴/s,入夜的稳定性较好,颗粒较细腻。
2.1.6反应过程中影响乳液性能的因素
(1)温度:温度过高,内部易产生粗离子,在较高温度下,反应快,乳胶粒的生长速度快,乳化剂不能迅速地吸附到乳胶里的表面以维持乳胶里的稳定。因此,乳胶粒易聚成粗粒子。最佳温度为84~86℃。
(2)拌速度:搅拌过快粒子相互凝结;过小,单体消耗不充分,易在高温下形成单体聚合,另外产生大量的热,散热不及时,反映自动加速,最终整个反应器凝聚。搅拌速度应在:120~400r/min。
2.1.4引发剂的选择
本试验用过硫酸铵作引发剂,总含量为0.2%,中后期与单体同步滴加,滴加速度约为单体的1/4。实验反应温度控制在84~86℃时,有稳定的回流,并且有较快的反应速率。
2.1.5滴加速度
滴加速度过快,则乳液粒径大,稳定性差[4]。本实验中后期单体加入速度控制在1~3滴/s,入夜的稳定性较好,颗粒较细腻。
2.1.6反应过程中影响乳液性能的因素
(1)温度:温度过高,内部易产生粗离子,在较高温度下,反应快,乳胶粒的生长速度快,乳化剂不能迅速地吸附到乳胶里的表面以维持乳胶里的稳定。因此,乳胶粒易聚成粗粒子。最佳温度为84~86℃。
(2)拌速度:搅拌过快粒子相互凝结;过小,单体消耗不充分,易在高温下形成单体聚合,另外产生大量的热,散热不及时,反映自动加速,最终整个反应器凝聚。搅拌速度应在:120~400r/min。
相关文章
发布评论