涂料技术
二氧化硅改性环氧树脂杂化涂料制备与特性
通过溶胶-凝胶法将γ-缩水甘油醚氧丙基三甲氧基硅烷硅烷(KH-560)改性SiO2硅溶胶,并用其掺混改性环氧树脂,制备有机-无机杂化涂料.利用红外光谱(FTIR)、接触角、热失重(TGA)和电化学交流阻抗谱(EIS)等对制备的涂层进行表征.结果表明:当改性SiO2硅溶胶与环氧树脂的质量配比为3∶2时,涂层的附着力、硬度、抗冲击和柔韧度性能最佳,同时涂层的耐酸、耐碱、耐汽油、耐蒸馏水和耐盐水效果也达到实际使用标准.杂化涂层中无机SiO2相与环氧树脂相间存在化学键及氢键作用,有机-无机杂化交联的结果提高了涂层的耐高温及防腐蚀性能.
关键词:环氧树脂;溶胶-凝胶法;二氧化硅;有机-无机杂化涂料
中图分类号:TQ630·4文献标志码:A文章编号:1673-4807(2010)05-0446-06
环氧树脂(EP)具有优良的粘结性、耐磨性、电绝缘性、耐高低温性、耐化学药品性,同时具有附着力好、力学性能优良以及收缩率低、易加工成型和成本低廉等优点[1],从而常作为金属防腐蚀涂层的材料.但纯环氧树脂固化后呈三维网状结构,交联密度高,存在内应力较大和质地硬脆、耐开裂性、抗冲击性、耐湿热性差及剥离强度低等缺点,因此在很大程度上限制了其在某些严酷环境中的应用[2].利用溶胶-凝胶法制备通过硅烷偶联剂改性的SiO2硅溶胶,并将其混掺入环氧低聚体,经热固化交联后,可得到有机-无机杂化涂料.硅烷偶联剂改性SiO2硅溶胶按照一定比例加入环氧树脂得到的杂化涂层具有很好的耐化学腐蚀性、高热稳定性和良好的机械加工性能.在这种杂化体系中,采用含有环氧基的硅烷偶联剂KH-560来偶联硅酸网络中的硅烷醇基团并组成末端带有环氧基团的有机-无机杂化网络,提高环氧相和无机SiO2溶胶相的相容性,提高涂层耐腐蚀能力和体系整体性能[3-5].
1实验
1.1实验材料
双酚A环氧树脂(WSR6101:环氧当量312-244g/eq),工业级(蓝星新材料无锡树脂厂);固化剂聚酰胺树脂,工业级(镇江柏穗化工有限责任公司);正硅酸乙酸乙酯(TEOS),分析纯(上海化学试剂采购供应五联化工厂);无水乙醇,分析纯(上海中试化工总公司);硅烷偶联剂KH-560(杭州沸点化工有限公司);蒸馏水;亚硝酸钠,分析纯(上海硫酸厂);助剂(广州市华夏奔腾实业有限公司);三聚磷酸铝,化学纯(中国医药(集团)上海化学试剂公司);硫酸钡,化学纯(上海泗联化工厂);氧化锌,化学纯(上海勒业化工厂);氧化铁红(安徽中意漆尔思防腐颜料厂).
1·2实验仪器及测试标准
BYKGardner型附着力测试仪(国营天津伟达测试机厂);GB6739-86涂膜硬度铅笔测定仪(国营天津伟达测试机厂);QTY-32型漆膜弯曲试验器(国营天津伟达测试机厂);Q153-3K1型冲击器;红外光谱仪(美国DIGILAB公司FT-5200);热分析仪(PE公司PyrisDiamondTG/TA);电化学综合测试系统(美国EG&G公司EG-GPARCM283).
1·3实验流程
1)溶胶-凝胶法制备KH-560改性SiO2硅溶胶按照TEOS∶KH-560=1∶4(摩尔比),将TEOS与KH-560加入三口烧瓶中,加入适量催化剂、乙醇和蒸馏水,78℃下反应6h.
反应结束后,抽真空加热,脱除副产物及溶剂乙醇.待副产物完全脱除后,得到澄清透明的KH-560改性SiO2硅溶胶.
2)改性SiO2硅溶胶/环氧树脂有机无机杂化涂料的配制及涂刷
将环氧树脂加入到正丁醇∶二甲苯=1∶1的溶剂中,然后按照不同比例将KH-560改性SiO2硅溶胶加入其中,混合搅拌均匀,再加入配方(见表1)所设定的各种填料,激烈搅拌分散均匀.将聚酰胺树脂溶解到正丁醇/甲苯混合溶剂中,溶解均匀.在其中加入KH-560改性SiO2硅溶胶/环氧树脂,搅拌均匀.放置半小时后,将其涂覆于打磨去油的马口铁板上.常温干燥后,再在80℃下固化2h,进行性能测试.
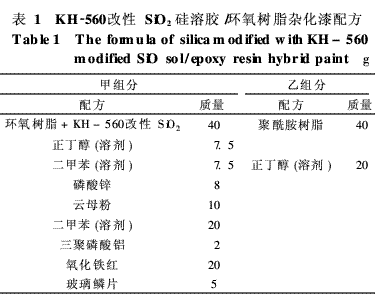
二氧化硅改性环氧树脂杂化涂料制备与特性
2结果与讨论
2·1红外图谱分析
通过红外光谱可以研究KH-560与SiO2硅溶胶的溶胶-凝胶反应,以及溶胶-凝胶的产物与环氧树脂交联固化后的反应情况.
TEOS水解后生成表面含羟基的SiO2无机同时网络,硅烷偶联剂发生了水解和部分缩聚,其水解产物与二氧化硅网络结构的表面羟基脱水缩合,起到了表面改性的作用;二氧化硅颗粒一经形成就被硅烷偶联剂改性,阻止了颗粒的进一步生长和团聚,从而提高了纳米粒子的分散度[6-7].
图1为KH-560改性SiO2硅溶胶的红外谱图,其中3397cm-1处为Si-OH吸收峰.它一方面可以与环氧基团发生交联缩合,另一方面,残留羟基与环氧树脂之间可形成氢键.在2936cm-1和2877cm-1处对应C-H伸缩振动峰,1250cm-1处为Si-O-Si和环氧化物环的骨架振动峰的叠加,912cm-1处为环氧基团中环的不对称伸缩振动.结果表明:KH-560中的环氧基在硅烷水解过程中并未发生破坏,可进一步发生化学交联.
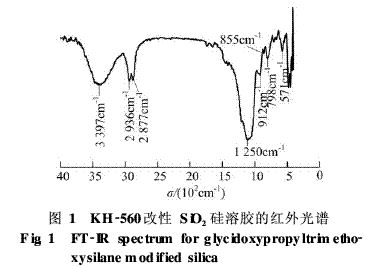
二氧化硅改性环氧树脂杂化涂料制备与特性
硅烷偶联剂在溶胶-凝胶过程中,与无机组分的前躯体共水解、共缩聚,使无机相得到有机化改性;硅烷偶联剂可参与有机聚合反应,将有机基体和无机粒子以桥梁的形式接在一起,使无机相与有机相以化学键结合,形成一个整体,成为真正的有机-无机杂化复合涂料[8].
图2为KH-560改性SiO2硅溶胶与环氧树脂复合固化涂层的红外光谱.在3500cm-1处附近存在较宽的吸收峰,为Si-OH和N-H等吸收峰的叠加.2935cm-1和2853cm-1处对应C-H伸缩振动峰.1608cm-1与1459cm-1处为环氧基团上苯环的骨架振动峰.1363cm-1处为C-N伸缩振动峰,表明聚酰胺树脂与KH-560/环氧树脂混合物发生交联固化反应.1250cm-1处附近为环氧树脂中聚醚的吸收峰,1040cm-1和850cm-1处对应Si-O-C的伸缩振动峰.图中未发现对应于环氧基团中的912cm-1不对称伸缩振动,这表明体系的环氧基团已开环,发生交联固化反应.
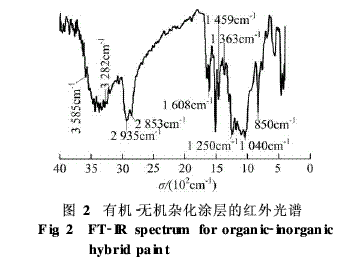
二氧化硅改性环氧树脂杂化涂料制备与特性
2.2TGA图谱分析
硅溶胶的特点是高温稳定性好,Si-O-Si的键能比C-O,C-C键高的多.图3为改性SiO2硅溶胶与环氧树脂比例在3∶2的条件下制备得到的有机-无机杂化涂层以及传统环氧涂层的热失重曲线图.从图中可以看出,环氧涂层在加热到100℃后就出现明显的热失重,残留率为70%,而有机-无机杂化涂层超过300℃才发生热分解,在320~500℃之间有一失重平台.对比曲线可以发现,加入KH-560改性SiO2硅溶胶后,热稳定性明显提高,这是因为,一方面Si-O-Si键能较强,另一方面无机SiO2网络与环氧树脂聚合物链形成相互交联的互穿结构,无机网络的形成抑制了聚合物分子链的运动,使得聚合物链段在热应力作用下的运动变得困难,从而显著提高了杂化涂料的耐热性.
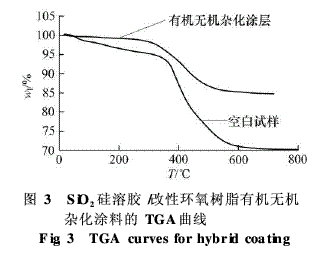
二氧化硅改性环氧树脂杂化涂料制备与特性
2·3涂层表面接触角分析
图4a),b)分别为环氧空白及环氧改性清漆涂层的接触角分析.环氧空白清漆涂层表面的接触角为45·56°,而环氧改性清漆涂层表面的接触角为65·38°.这表明加入KH-560改性SiO2硅溶胶后,水在涂层表面的接触角变大,明显具有憎水性.导致接触角变大的原因是改性SiO2硅溶液在固化过程中有向表面富集的趋势[9].
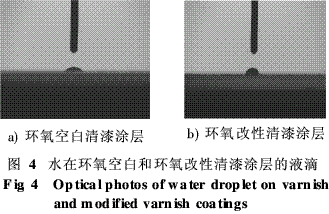
二氧化硅改性环氧树脂杂化涂料制备与特性
2.4漆膜力学性能测试
以环氧树脂为成膜树脂的涂层,其内应力大、质地硬脆,耐开裂性、抗冲击性、耐湿热性差及剥离强度低.硅氧烷的主链为无机Si-O键,其键能比C-C键高得多,具有高温稳定性.此外,Si-O-Si键角大,Si-O键的键长长,因此Si-O-Si旋转自由,分子链较为柔顺.KH-560改性SiO2硅溶胶,其带有可交联固化的环氧基团,与环氧树脂共混,一方面残留羟基与环氧树脂上的羟基发生脱水缩合;另一方面,环氧基与聚酰胺进行交联固化反应.有机-无机杂化相互作用,可提高以环氧树脂为基体树脂的涂层的韧性等力学性能.对TEOS与KH-560缩合物与环氧树脂的不同配比制备的SiO2硅溶胶/改性环氧树脂有机-无机杂化涂料进行比较,用马口铁板作为基材,测试结果见表2.
从表2可以看出,漆膜表干的速度从快到慢依次为1∶4<2∶3<1∶1<3∶2<4∶1.当配比为1∶4时,漆膜的成膜性很差,且表干时间很长,大多时候不符合工厂或工程流水线工作的需要.固化速度好的是3∶2和4∶1,涂膜的机械性能较好.虽然Si-O-Si键长较长,键角较大,柔韧性很好,但在一定比例下,体系硬度并不因为改性硅溶胶的加入而有所降低.
硅溶胶材料具有较低的表面张力,并有很好的电学性质.但由于分子间作用力小,其机械性能略低,耐油性差.根据表3的结果可证明这一点,KH-560改性SiO2硅溶胶在体系中比例过大,与环氧树脂比例达到4∶1和3∶2时,涂膜的耐酸、耐碱、耐汽油浸泡性能都很差.而当环氧树脂含量提高时,如配比1∶1,2∶3和1∶4时,涂层的耐酸、耐碱、耐蒸馏水、耐盐水、耐汽油浸泡性能都很好.
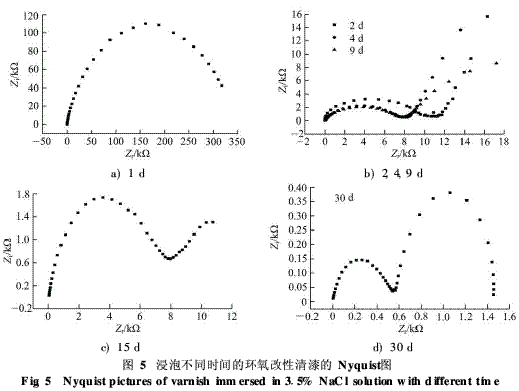
二氧化硅改性环氧树脂杂化涂料制备与特性
2·5交流阻抗图谱分析
图5为浸泡不同时间的KH-560改性SiO2硅溶胶掺混环氧清漆的Nyquist图.清漆由于涂层中未加任何填料,电解质溶液很容易穿透涂层,到达金属/涂层界面处.当电解质溶液浸透涂层,在浸泡初期电解质溶液从涂层孔道中进入涂层的速度远小于电解质在界面处生成腐蚀产物的速度,界面处不溶性腐蚀产物浓度高,要向溶液中扩散,此时扩散控制腐蚀过程.浸泡初期图的Nyquist图为一圆弧拖尾线性,随着浸泡时间的延长,拖尾消失,Nyquist图逐渐变为直径很大的容抗弧,进入浸泡中期.这是由于浸泡初期虽然水溶液通过涂层的溶胀在涂层表面的微孔缝隙向涂层内渗透,但只有极少的水分到达涂层金属基体界面.随着水不断渗入到涂层中,使得涂层孔道增大,扩散过程不再起控制作用,而是由电荷转移过程控制.溶液到达界面处,在界面处生成了钝化膜并加速了腐蚀产物的生成.到浸泡中期后,随着越来越多的电解质到达界面,此时电解质与腐蚀产物之间形成容抗模型,扩散特征消失.随着浸泡时间的延长,涂层电阻不断变小.浸泡到30d,涂层的阻抗值明显减小,明显小于105Ω·cm2,涂层已失去防护作用.这可能是由于随着电解质不断渗入到有机涂层中,大量的Cl-破坏了界面处生成的腐蚀产物膜导致腐蚀的加剧.