涂料技术
高固体分丙烯酸改性聚氨酯涂料的研制
关键词:高固体分涂料;聚氨酯涂料;高固高羟低黏树脂;环保
1.引言
自20世纪60年代以来,世界各国日益重视有机挥发物对大气的污染,普通溶剂型涂料在施工时含有较多的有机溶剂,这些溶剂在涂膜干燥过程中全部挥发进入大气,造成严重的污染问题。因此工业发达国家均成立了专门的管理机构,制定各种法令对涂漆时的溶剂挥发量加以严格的限制。70年代以来各种低污染的涂料应运而生,高固体分涂料就是其中的一种。丙烯酸聚氨酯涂料是双组分常温固化涂料,具有涂层干燥速率快,施工周期短,漆膜机械性能、耐老化性、耐化学品性优良等特点,广泛应用于各种金属制品、塑料制品的表面涂装,还可以作为修补漆使用。目前现有的丙烯酸聚氨酯涂料固体含量为50%~60%,加入稀释剂后,其施工固体含量一般为30%~40%,对大气污染较大。本文以高固高羟低黏的羟基丙烯酸树脂和合成脂肪酸树脂为主要原料制备高固体分丙烯酸改性聚氨酯涂料,并对影响涂料性能的几个主要因素,如羟基丙烯酸树脂、合成脂肪酸树脂、固化剂、几种助剂和有机溶剂等进行了讨论,制得综合性能良好、施工方便的高固体分聚氨酯涂料,具有较好的环保意义。
2.试验部分
2.1原料与仪器设备
原料:羟基丙烯酸树脂,荷兰DSM;高分子分散剂,荷兰EFKA;合成脂肪酸醇酸树脂,上海高点;HDI三聚体(N3390),德国Bayer;所有有机溶剂,深圳江海天;丙烯酸类流平剂、有机硅类流平剂,德国BYK;消泡剂、金属锡催干剂,台湾德谦;气相二氧化硅,德国Degussa;钛白粉R-706,美国杜邦;稀释剂,自制。仪器设备:VFS-230高速分散机,上海上微金丽电机有限公司;SK-2立式砂磨机,江苏武进市八方机械厂;303A-2电热鼓风干燥箱,上海浦东荣丰科学仪器有限公司;涂-4#黏度杯、刮板细度计,天津材料试验机厂;QUV老化仪,美国Q-PANEL公司。
2.2主体树脂的性能指标
试验采用羟基丙烯酸树脂、合成脂肪酸醇酸树脂和N3390制备涂料,它们的性能指标见表1。
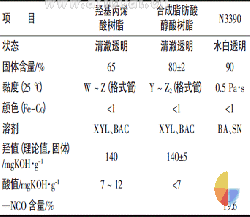
表1主体树脂的性能指标
表2钛白色浆制备参考配方
生产工艺分2个步骤:①在低速搅拌下把气相二氧化硅加入合成脂肪酸醇酸树脂中,添加完毕后高速分散30min,制成母液备用;②把高分子分散剂均匀地溶解在溶剂中,再加入钛白粉分散均匀,最后加入①制成的母液,高速搅拌均匀,静置24h后上砂磨机研磨,要求细度不大于15μm。
2.4高固体分丙烯酸改性聚氨酯涂料的制备
高固体分丙烯酸改性聚氨酯涂料的配方见表3。
表3高固体分丙烯酸改性聚氨酯涂料参考配方
生产工艺(甲组分):按配方量依次加入树脂、助剂及钛白色浆搅拌均匀,用稀释剂调整涂料黏度到合适范围,过滤、包装。甲组分与固化剂分开包装,否则会胶化。使用时再按规定比例混合,稍微稀释后即可喷涂。
2.5性能检测
将甲组分与固化剂以4∶1均匀混合,用稀释剂稀释到黏度为20~25s[涂-4#杯,(25±1)℃],空气喷涂,底材为已用600目砂纸打磨好的普通冷轧钢板,流平10min后放入80℃烘箱烘烤30min(也可常温干燥24h),取出静置。7d后测试性能,结果见表4。
表4丙烯酸改性聚氨酯涂料性能测试结果
注:涂料状况、贮存稳定性检验的是涂料的甲组分;原漆黏度、固体含量指的是甲组分与固化剂混合后,未用稀释剂稀释时的黏度和固体含量;胶化时间指的是甲组分与固化剂混合并稀释后至二者胶化的时间,也就是涂料的使用时间。
3.结果与讨论
3.1成膜树脂的选择
高固体分涂料要求原漆具有较高的固体含量(一般要求固体含量不低于70%),同时黏度不能过高。这是因为,如果原漆黏度过高,在涂装施工时必须加入较多的稀释剂,一来这些稀释剂在漆膜干燥过程中挥发到大气中去,这样高固体分涂料就失去了环保意义;二来稀释剂大量加入,必然会造成涂料的施工固体含量下降,要达到规定的漆膜厚度,必须增加喷涂遍数,这样降低了劳动效率,也增加了溶剂的挥发,同样不利于环保。另外,成膜树脂的固体含量越高,羟值越高,所需要的固化剂量也就越多,由于固化剂的固体含量一般都很高,所以制成的涂料固体含量也越高。因此在选择成膜树脂时,在保证涂料性能的基础上,应尽量选择高固体分、高羟值、低黏度的树脂。经过多次试验比较,成膜树脂选择荷兰进口的羟基丙烯酸树脂和国产的合成脂肪酸醇酸树脂。二者都是高固含高羟低黏的树脂,且混容性良好,前者干燥快速,耐黄变性、机械性能、耐化学品性佳,但是若单用它制备涂料,在漆膜光泽、丰满度等方面还略显不足,因此加入合成脂肪酸醇酸树脂对其改性,后者的光泽高、丰满度好,对颜料的润湿性好,缺点是硬度和耐候性稍差。二者配合使用,取长补短,可制得综合性能良好的涂料。试验表明,当羟基丙烯酸树脂和合成脂肪酸醇酸树脂固体含量比为(1.9~2.2)∶1.0时,漆膜的综合性能最佳,满足技术指标的要求。在本试验配方中,二者固体含量比:(44×65%)/(50×35%×80%)=2.04。
3.2成膜树脂/固化剂配比
涂料用固化剂选用德国Bayer公司产的N3390,这是业界较常用的HDI异氰酸酯固化剂。该固化剂也是高固低黏的树脂,其干燥速率快,所得漆膜机械性能好,具有良好的耐候性和耐化学品性。对于聚氨酯涂料中甲组分与固化剂的配比,有一个计算式:
—NCO%=—OH%×N×2.47×Z
式中,—NCO%指的是固化剂中的异氰酸根含量;
—OH%指的是甲组分中成膜树脂的羟基含量;N指的是甲组分与固化剂的配比(N=1表示1∶1,N=2表示2∶1等);Z指的是交联密度,理论取值为1。
—OH%=羟值(理论值,固体)×X%×Y%/33式中,羟值(理论值,固体)可以在树脂的性能指标中查到;X%指的是树脂固体含量;Y%指的是该树脂在甲组分中的含量。
根据以上2个公式,可以计算出甲组分与固化剂的理论配比,但是实际数据要通过试验确定。在配方确定的情况下,—NCO%、—OH%都是确定的,N的大小取决于Z的取值。研究表明,Z取值低,则N大,固化剂用量少,漆膜的耐溶剂性、耐水性、耐化学品性及硬度均下降,甚至漆膜发软;Z取值高,则N小,固化剂用量多,则可提高耐溶剂性、耐化学品性,延长活化期。一般情况下,聚氨酯涂料中Z取值大都略高于1,如1.05~1.10。在本试验中,Z值取1.10,算出N=4,再用4∶1这个配比试验,漆膜的综合性能良好,满足技术指标的要求,因此最后确定甲组分与固化剂配比为4∶1。
3.3助剂的影响
3.3.1流平剂
高固体分涂料在施工中常出现缩孔问题。缩孔大多是由尚未干燥的漆膜上的杂质颗粒所引起,颗粒使其周围液态涂层的表面张力降低,使之向外围的较高表面张力的涂层流去而形成凹形缩孔,孔内中心为杂质颗粒。高固体分涂料中所用树脂和溶剂的极性一般比常规涂料大,与杂质颗粒的表面张力相差就更大,在有颗粒存在时,其周围产生的表面张力差更易导致缩孔。因此要在高固体分涂料中加入流平剂。流平剂一般是利用与涂料体系的一种可控制的不相容来降低涂料体系的表面张力,促使漆膜流平,消除漆膜的表面缺陷。常用的流平剂有2种,丙烯酸类流平剂和有机硅类流平剂。本试验中这2种流平剂都有采用,它们进口自德国,其中的丙烯酸类流平剂可以降低漆雾敏感性,适用于高质量的工业色漆和清漆,与大多数成膜物混容性优异,在清漆中不会引起浑浊,在色漆中不会产生雾影;有机硅类流平剂则可以增进表面滑爽,防止贝纳德旋窝,改进流平和增加光泽,给予防粘连性质,降低表面张力,并因而提供更好的底材润湿功能。它们对高固体分涂料性能的影响见表5。
表5流平剂对高固体分涂料性能的影响
从表5可以看出,单一的流平剂很难达到理想的流平效果,当2种流平剂配合使用时,能起到协同增效作用,达到较好的流平效果,同时漆膜的光泽也有所提高。经多次试验,当丙烯酸类流平剂添加量为0.4%,有机硅类流平剂添加量为0.1%时,涂料的流平效果最佳。需要注意的是,该有机硅类流平剂添加量很少,为了准确添加,最好把它预先溶解在溶剂中,本试验是将其预先溶解在二甲苯中制成10%溶液再添加的。另外,市场上有的有机硅类流平剂会对漆膜层间附着力产生不良影响,使用前要通过试验仔细鉴别。
3.3.2催干剂
聚氨酯涂料是基于多异氰酸酯与多羟基树脂之间__的反应,加入微量的催干剂可以降低活化能,促进异氰酸酯的反应,并引导反应沿着预期的方向进行。聚氨酯涂料中常用的催干剂有叔胺类、金属化合物和有机膦3类,其中金属化合物中的锡催干剂最常用。本试验中采用台湾产的金属锡催干剂制备甲组分,调配到合适黏度后放入(50±1)℃烘箱中贮存2周,测定黏度变化情况;并把甲组分与固化剂以4∶1混合并稀释后制板,80℃烘烤30min。7d后测试性能,结果见表6。
表6金属锡催干剂对涂料性能的影响
从表6可以看出,随着金属锡催干剂添加量的增加,漆膜表干时间变短、耐水性变差,涂料贮存稳定性变差(黏度增加程度变大),而机械性能无明显变化。比较来看,当金属锡催干剂添加量为0.04%~0.06%时漆膜综合性能最佳,可满足技术指标的要求,本试验配方中添加量为0.05%。需要注意的是,该金属锡催干剂添加量很少,为了准确添加,最好把它预先溶解在溶剂中,本试验中是将其预先溶解在二甲苯中制成5%溶液再添加的。
3.3.3触变剂
与常规涂料相比,高固体分涂料更容易出现贮存过程中颜料沉淀和施工应用时流挂的情况:①前者主要是因为涂料黏度较低,而高固体分涂料由于遮盖力的需要,其颜料体积比一般不低于常规型涂料,固体含量越高,单位体积中颜料的质量也越大,在贮存期间较易出现颜料沉淀问题。②后者不仅会出现在喷涂施工过程中,更严重的是出现在进炉烘烤后的加热期间。经验数据表明,高固体分涂料的施工固体含量虽然比常规涂料高很多,但是喷涂在物面上时二者的固体含量却相差不大,从而高固体分涂料的黏度比常规涂料低不少,更容易出现流挂现象。在加热烘烤过程中,溶剂挥发会使涂层黏度增高,加热升温则会降低涂层黏度,常规涂料中,二者的作用基本上相互抵消,不会出现问题;但是在高固体分涂料中,加热升温时所导致的黏度下降十分严重,溶剂挥发所引起的黏度增高远不能与之相抵,从而引起严重的流挂现象。因此高固体分涂料需要加入触变剂来解决以上问题。常用的触变剂有气相二氧化硅、有机改性膨润土、氢化蓖麻油、聚乙烯蜡和酰胺蜡类等。本试验中采用德国进口的气相二氧化硅,它属于胶体粒子,比表面积为175~225m2/g,表面有硅醇基。气相二氧化硅在涂料中经充分搅拌分散后,硅醇基间形成氢键,产生立体网状结构,赋予涂料一种结构黏性。该结构黏性具有触变性,即在涂装时的高剪切速率下,结构黏性很低,有利于涂膜流平;涂装结束或涂料贮存期间,剪切速率接近零,结构黏性很大,起到防止涂膜流挂和涂料沉淀的作用。需要注意的是,要使气相二氧化硅起到良好的触变作用,又要不明显地降低光泽,必须把它分散得极好。气相二氧化硅常规添加方法是先与成膜树脂高速分散均匀制成母液,再把母液分散到涂料中,这样效果较为理想。试验表明,该气相二氧化硅添加量为1%~2%时效果最佳。在本试验配方中,其添加量为1.5。
3.3.4消泡剂
聚氨酯涂料经常有起泡的弊病,需要添加消泡剂,通常分为非硅树脂类消泡剂和有机硅类消泡剂。树脂类消泡剂是热塑性共聚树脂,例如乙烯基异丁醚和丙烯酸酯的共聚体等,其特性是与涂料不相容,能将存在于漆膜中的小气泡表面层破坏,使小气泡逐渐合并成大气泡。按Stoke定律,气泡上升的速率与其直径的平方成比例,气泡越大,上升越快,升至漆膜表面而消除之。有机硅类消泡剂也有消除漆膜气泡的功能,气泡一旦升至表面,由于有机硅体系的表面张力很低,能在泡的表面展布而使泡破裂。有机硅类消泡剂消泡能力优良,但使用不当容易出现副作用,如引起缩孔、层间附着力变差等。一般而言,树脂类消泡剂适用于底漆,有机硅类消泡剂适用于面漆。本试验配方选用台湾产的改性有机硅类消泡剂。该消泡剂对聚氨酯涂料因反应生成的气泡的消泡效果极为显著,同时兼具改善涂料的流动性和漆膜的平整性与光泽的功能。试验表明,该消泡剂添加量为0.3%~0.5%时,效果最佳。本试验配方添加量为0.4%。
[page 3.4有机溶剂的影响
高固体分聚氨酯涂料在施工时需加入少量稀释剂,它由多种有机溶剂配制而成。选择溶剂时要注意以下几点:①不能含有能够与异氰酸酯(R—N=C-O)反应的物质使漆变质。因为异氰酸酯的活性很高,能与__醇类、水等反应,所以聚氨酯涂料中不能用醇、醚醇类溶剂,而且所用的溶剂里不能含水。②要求既能保持涂料施工时有较高的固体含量,又能降低涂料的黏度。经验数据表明,在降低涂料黏度及提高固体含量方面,酮类溶剂优于酯类溶剂优于烃类溶剂,因此应多用酮酯类溶剂,烃类溶剂适当采用。③要平衡下列各项要求:挥发速率合适、流平性好、无缩孔、无起泡等。一年四季气温相差较大,夏季气温高时,溶剂的挥发速率大大加快,使漆膜的表干时间缩短,流平性能变差,导致漆膜产生许多表面缺陷,如橘皮、针孔等,因此应选用挥发速率较慢的溶剂,以减少漆膜的表面缺陷,相反冬季气温低时,应选用挥发速率较快的溶剂,春秋季作适当调整。综合以上几点,通过试验得出较好的高固体分聚氨酯涂料用稀释剂配方,结果见表7。
表7高固体分聚氨酯涂料用稀释剂参考配方
4.结论
以高固高羟低黏的羟基丙烯酸树脂和合成脂肪酸树脂为主要原料制备高固体分丙烯酸改性聚氨酯涂料,并对影响涂料性能的几个主要因素进行讨论,结果制得漆膜干燥速率快、光泽高、丰满度、机械性能、耐化学品性、耐候性和贮存性好的高固体分聚氨酯涂料。该涂料装饰性强,施工方便,应用广泛,并且溶剂挥发少,具有较好的环保意义。