涂料文集
双组分聚氨酯塑料清漆快干探讨
汤京强(上海交通大学化学化工学院201108)
摘要:通过实验确定了有利于双组分聚氨酯塑料清漆加快固化的催化剂及其组合,在不影响涂膜性能和施工使用时间的前提下,适应不同烘烤温度和烘烤时间的塑料件涂装生产线。
关键词:双组分塑料清漆;聚氨酯;快干;催化剂
0前言
现代汽车中,塑料部件的比重越来越大,塑料部件的供应商愈来愈多,对涂装的要求也越来越高,为了适应不同的塑料件涂装生产线,适应不同的材质,我们在双组分聚氨酯塑料清漆部分做了很多研究,以期对不同的涂料生产商和使用厂商有良好的借鉴和参考。
1问题的提出及解决途径
某些北方保险杠厂家使用双组分聚氨酯清漆(丙烯酸树脂/HDI体系)施工时,因其烘烤时间短或者烘烤温度低,导致产品出烘房后指触不干,易吸附灰尘,更影响打磨或者装配。要求提供适应其生产条件的快干型塑料清漆。从聚氨酯理论可知,—NcO和—OH的反应从混合后就已开始,但当—NCO的反应率超过35%时,才开始表现出漆膜的特性。所以要加速—NCO的反应来获得快干漆膜。通过以下途径可以改良聚氨酯的干燥固化进程:A.使用软化点、玻璃化温度(Tg)高的异氰酸酯树脂和多羟基组分;B.拼人物理干燥型树脂;c.利用其它反应;D.提高烘烤温度;E.添加催化剂;F.选择官能团位阻小的多羟基树脂。因产品基础配方的调整需要很长时间,故考虑选择E方式,即添加合适的催化剂(促进剂),对固化工艺进行改进,降低活化能,促进异氰酸酯的反应,缩短固化干燥时间,以便达到客户的个性化需求。
2催化剂的选择
可用于聚氨酯涂料的催化剂很多,常用的有3大类:叔胺类、金属化合物、有机磷类。但就—NCO/OH型双组分聚氨酯清漆干燥而言,由聚氨酯键产生的桥键结构的形成是最重要的因素。作为促进—NCO与—OH反应的方法,可选择碱、有机酸、金属化合物等催化剂,尤以胺类、锡和锌的金属化合物特别见效,但必须同时考虑催化剂的加入对双组分清漆的适用期(potlife)以及对产品性能的影响。
塑料件用双组分聚氨酯清漆以NCO/ROH型反应为主。主要反应如下:
2.1催化剂介绍
2.1.1DBTL(二丁基二月桂酸锡)
二丁基二月桂酸锡,其催化活性要比大多数过渡金属有机化合物强。同时它与异氰酸酯单体有非常好的相容性,不需加入助催化剂,减少固化树脂的水解反应,提高树脂的耐湿热性能。用量小于0.02%,若添加量过多,会明显降低涂料的活化期,而且固化膜发软,耐候性变差。
2.1.2DABCO(三亚乙基二胺)
1,4-重氮二环(2.2.2)辛烷,即三亚乙基二胺,使用时由33%的三乙烯二胺与67%醇混合而成,醇一般选择异丙醇或异丁醇。它在反应过程中有利于质子从—OH向—NCO转移。质子从—OH脱去可以发生在与—NCO反应的过程中,因此避免了在氧原子上形成正电荷,降低了反应中间体的活化能,从而促进了反应的进行。其用量不高于1.0%。
2.1.3环烷酸锌或辛酸锌
作为助催干剂,主要用于脂肪族聚氨酯漆,对芳香族聚氨酯漆的催化作用较弱。其毒性低于DBTL,且施工时限亦比DBTL稍长,有利于漆膜内部的固化干燥,提高了涂膜的耐水性和耐候性。用量约为基料的0.2%。
2.2催化剂的催化作用及选择
不同的催化剂催化作用也不同,所以催化剂的选择和组合使用是关键,这也与涂料本身的树脂体系紧密相关。催化剂与凝胶时间的关系见表1。
表 1 催化剂与凝胶时间的关系 min
从表1可以看出:(1)3种催化剂中DBTL的催化性能最强,DABCO次之,辛酸锌最弱。(2)DBTL与DABCO的混合物比单纯的DABCO或DBTL作用强,有增效催化作用,原因是胺促进了羟基中的质子转移,锡则是与羟基生成了络合物而促进了反应。
根据上述分析,我们决定混用DBTL,DABCO和辛酸锌3种催化剂,以达到催化效果好、施工时间长、毒性小、固化内外均匀,后遗症少的目的。
2.3从粘度变化来确定催化剂组合
催化剂对双组分清漆适用期试验如下:
将A组分(丙烯酸树脂)、B组分(1,6-己二异氰酸酯,即HDI)以及稀释剂C按实际配比A:B:C=100:30:30(质量比)混合。在清漆中加入催化剂,混合均匀,密封在塑料杯中,放置在23℃,55%的恒温恒湿环境中。每隔1h取出,测其粘度变化,如粘度明显增大,则这个时间即为适用期极限。根据产品配方设计和一般生产线施工要求,适用期要不小于4h,即产品配好放置4h后粘度还在要求的规格内。清漆施工规格要求:17~21s/22~24℃(粘度测量仪器采用ERICHSEN243,DIN53211甜粘度杯,即下文中提到的DIN4#,粘度单位:s)。
图 1 是清漆中未加催化剂时粘度随时间的变化 曲线
从图1可以看出:在规定的温度范围内,原漆放置4h以后,粘度才有比较明显的变化,即此清漆产品的适用期为4h。
根据催化剂的特点做以下4组试验,观察加催化剂后施工适用期的变化(表2~表5)。
表 2 DBTL 的影响
从表2可以看出:添加DBTL后,适用期缩短很快,放置2h后粘度就变化很大,故DBTL的用量要尽量少,小于0.015%,但又不能降低催化效果,所以在减少DBTL的同时需补加另外的催化剂。
表 3 复合催化剂的影响
从表3粘度变化数据可看出:减少DBTL,增加DABCO后,适用期增加,有利于现场施工。但还是不够理想。考虑再减少DBTL,提高DABCO的用量,增加异辛酸锌。异辛酸锌的补加,让内外干燥速度差异变小,在成品下线后的一段时间内,利用湿气固化继续加速反应(表4)。
表 4 复合催化剂的影响
从表4可看出:适用期有改善,但不是很明显。还需再次调整催化剂组合配比来优化(表5)。
表 5 复合催化剂的影响
由表5看出:催化剂配比如下:DBTL0.004%,DABCO0.13%,异辛酸锌0.03%时,产品适用期为4h左右,达到产品的规格要求,也能满足生产线的正常生产需求。
2.4从硬度和实际施工效果来确定催化剂组合
按A:B:C=100:30:30的比例调制好施工粘度的清漆,在其中加入不同类型和不同比例的催化剂,在PP—EPDM上施工,先按正常工艺喷涂塑料底漆,色漆,然后再罩光清漆,闪干时间5min,然后烘烤。采用ERICHSEN299漆膜摆杆试验仪来测试硬度,科尼可摆杆的质量是200g,摆动周期1-4s,阻尼时间250s(计算方式:T=摆动次数×摆动周期,测试环境:温度21~25℃,湿度45%~50%o催化剂的影响分别见表6、7。
表 6 催化剂的影响
由表6可见:加催化剂后,烘烤时间从30min缩短到20min,干燥性、可打磨性明显改善。但催化剂的加入量和加人种类的组合对漆膜外观有影响,尤其是桔皮。所以,要同时考虑漆膜外观和性能的变化,特别是耐低温冲击性(因为北方冬天气温低)
表 7 催化剂对外观的影响
由表7可见:控制催化剂的量在适当范围内,对漆膜外观没有明显影响。而且表干快,可以很快进行下一道工序,抛光打磨或是包装。
3催化剂选择后的应用试验
按照表5中的催化剂组合配比,做以下试验,观察清漆粘度的变化对现场施工的影响(表8)。
表 8 清漆粘度变化对施工性的影响
随着清漆粘度的提高,即固化程度的增加,施工性变差,外观变差,表面干燥程度变差。实际生产中要严格控制清漆的施工时间,在规定的清漆适用期内使用才能得到良好的效果。当然,对机器人的A、B组分喷嘴即混型,不存在适用期的问题。选择表7中4号催化剂组合配比来调漆施工,观察不同烘烤条件下固化的速率(摆杆硬度变化)和最终结果,并与不加催化剂的试验结果做比对(表9)
表 9 不同烘烤条件下的摆杆硬度
对比催化剂添加与否,烘烤条件不同对固化程度的影响,发现添加催化剂后可适当减少烘烤时间或降低烘烤温度。室温放置7d后,硬度稳定,固化趋于完全,性能测试无显著差异。
4保险杠生产线应用
经过实验室的模拟和分析论证,选用DBTL0.004%、DABCO0.13%、异辛酸锌0.03%作为催化剂组合来促进双组分聚氨酯清漆的固化。实践证明:加催化剂的油漆在生产线调配好以后,4h内使用没有任何问题,喷好清漆的保险杠经8O℃,20min烘烤,出烘箱后2min就可以打磨抛光,返线或是装配包装,克服了原先因漆膜软而需要放置很长时间才能进行下道工序的缺点,提高了生产效率。
实际应用过程中因为催化剂用量微少,建议把催化剂提前加到稀释剂中(C组分)或是清漆中(A组分)。试验证明,与—OH化合物(A组分)混容1年没有问题。
5结语
通过实验室探索、模拟以及生产线的实际使用情况,选用优化的催化剂组合既保证原有双组分聚氨酯清漆的性质,又能快速干燥固化,达到客户特别的要求,实现了预期的目的。
如转载, 请注明: 资料来源"中国艺术涂料网" 中国艺术涂料网“转载文章,请注明:文章来源中国艺术涂料网”
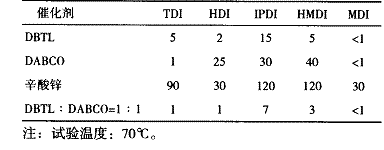
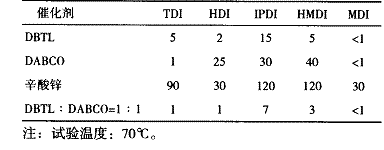

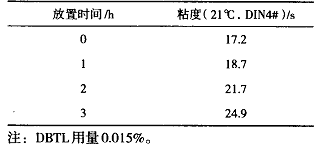
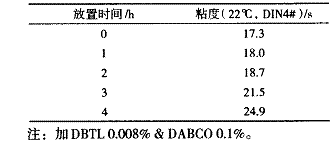
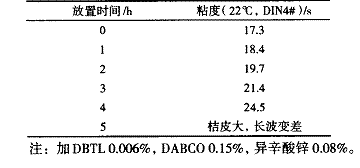
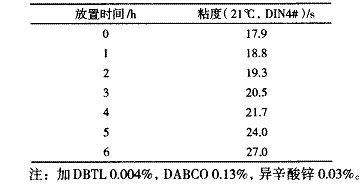
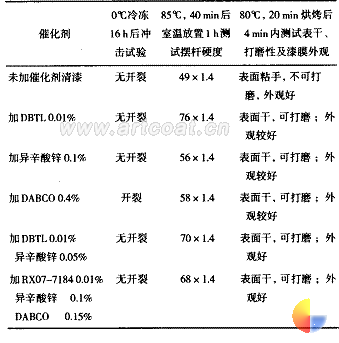
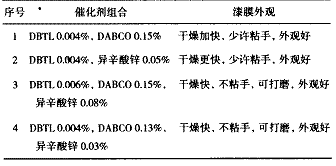
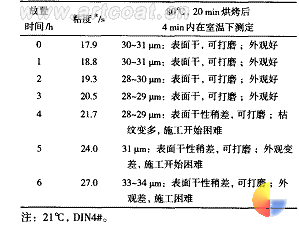
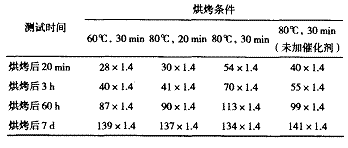
下一篇:小议聚氨酯涂料中分离游离异氰酸酯
相关文章
发布评论