涂料文集
超微聚苯乙烯有机刚性粒子的合成工艺研究
郝留成 1, 2 , 冯焕丽 1 (1 . 河南平高电气有限责任公司 , 平顶山 467001; 2 .浙江工业大学化学工程与材料学院 , 杭州 310014)
摘 要 : 研究了超微聚苯乙烯 ( PS) 有机刚性粒子的合成工艺 , 采用激光粒径分析仪对合成 PS 有机刚性粒子的粒径及其分布进行了表征 ; 并采用萃取的方法研究了有机刚性粒子的交联度与交联剂添加量的关系。实验结果证明 : 通过控制合成工艺 , 可制备出可控粒径最小在 0 . 39 ~ 0 . 46 μ m 范围内的 PS 有机刚性粒子 , 粒径分布窄。
关键词 : 乳液聚合 ; 聚苯乙烯 ; 有机刚性粒子 ; 合成工艺 ; 粒径分布
0 引 言
近年发展起来的刚性粒子 (Rigid Filler, 简称 RF) 增韧聚合物 , 不但可使材料的韧性得以提高 , 同时也可使其强度、模量、耐热性、加工流动性能等得到改善 , 显示了增韧增强的复合效应。目前 , RF 改性聚合物已引起人们的高度重视 , 其研究逐渐深入 , 取得了许多实质性的进展 [ 1 ] 。 RF 主要包括有机刚性粒子 (Rigid Organic Filler, 简称 ROF) 和无机刚性粒子 (Rigid Inorganic Filler, 简称 R IF) 。常用的 ROF 有聚甲基丙烯酸甲酯 ( PMMA) 、聚苯乙烯 ( PS) 、甲基丙烯酸甲酯 / 苯乙烯共聚物 (MMA /St) 及苯乙烯 / 丙烯腈共聚物 ( SAN) 等 , 而最为常用的 R IF 为 CaCO 3 、 BaSO 4 等。刚性粒子增韧技术是制备兼具高刚性和高韧性的聚合物复合体系的有效手段 , 不仅具有重要的理论研究价值 , 而且具有广阔的应用前景和商业价值。
自 1984 年 Karachi 和 Ohta 明确提出了脆性塑料粒子分散于韧性基体中能提高基体的耐冲击性能以来 [ 2 ] , 人们陆续研究了很多混合体系 , 如 PS 、 PMMA 、 SAN 对 PVC /CPE 、 PVC /ABS 以及用 PS 直接对 PVC 韧性体系的进一步增韧等 [ 3 ] 。采用有机粒子代替无机粒子对 PVC 增韧的研究较多 [ 4 - 5 ] , 而用有机粒子增韧 PP 的研究国内目前研究较少。 PS 与 PP 的相容性较好 , 本文重点研究了超微 PS 有机刚性粒子的常规乳液聚合合成工艺 , 为下一步研究 PS 增韧 PP 奠定基础。
1 实验部分
1. 1 主要原料
苯乙烯 ( St) : 试剂级 ; 二乙烯苯 (DVB) : 工业级 ; 过硫酸钾 ( KPS) : 试剂级 ; 磷酸二氢钠 (Na 2 H 2 PO 4 ) : 试剂级 ; 乳化剂 A 、 B 、 C: 工业级。
1. 2 主要仪器
激光粒径分析仪 ,OMEC LS - POP ( III) 。
1. 3 有机刚性粒子的合成
分别称量一定量的水、单体、交联剂、乳化剂在一定的温度下预乳化 , 备用。剩余部分水、乳化剂在一定温度下乳化 , 乳化后加入部分引发剂和缓冲剂的水溶液 , 升温至反应温度 , 然后滴加单体预乳液 , 同时均匀滴加剩余引发剂和缓冲剂的水溶液 , 滴加结束后保温一定时间 , 升温熟化 , 降温、破乳、洗涤、过滤、真空干燥至恒质量。
1. 4 性能测试
1. 4. 1 粒径及其分布
把不同工艺条件下合成的乳液样品用蒸馏水稀释一定倍数后 , 用激光粒径测试仪测试每个样品的粒径及其分布。
1. 4. 2 交联度的测定
将合成的有机刚性粒子乳液样品破乳 , 80 ℃ 真空干燥至恒质量 , 取出置于干燥器备用。用电子天平准确称滤纸的质量 , 取 2 ~ 3 g ( 精确至 1 mg) 待测试样 , 用干燥滤纸将样品包好 , 并准确称质量 , 然后放入索氏萃取室的中部。用二甲苯作为萃取剂 , 萃取 24 h, 每分钟回流 7 ~ 8 次。然后将样品包自然风干 , 并真空干燥至恒质量 , 准确称量 , 计算交联度 [ 6 ] 。交联度为萃取后剩余物的质量占试样原始质量的百分含量 , 又称凝胶含量。其计算公式如下 :
交联度 = ( m 3 - m 1 + m i ) / ( m 2 - m 1 )
式中 m i —滤纸损失质量 ; m 1 —滤纸质量 ; m 2 —样品包质量 ; m 3 —萃取后样品包质量。
2 结果与讨论
2. 1 乳化体系对乳液性能的影响
乳化剂的种类和浓度直接影响引发速率及链增 长速率 [ 7 ] 。它同时会影响决定聚合物性能的聚合物 的相对分子质量及相对分子质量分布 , 以及影响与乳 液性质有关的乳胶粒浓度、乳胶粒的粒径及粒径分布等。因此 , 乳化剂对产品的性能起着至关重要的作用。所以乳液聚合中乳化剂的选择是否合理 , 关系到乳液体系是否稳定 , 生产过程能否正常进行 , 以及贮存是否稳定及应用是否安全可靠 , 同时也关系到生产成本 , 因此选择一个好的乳化体系是乳液聚合顺利进行的关键。
阴离子型乳化剂合成的乳胶粒子小 , 聚合物易结块 ; 非离子型乳化剂对电解质的化学稳定性好 , 但聚合速度慢 , 聚合中易发生凝聚。而阴离子乳化剂和非离子乳化剂具有协同作用 , 因此选择阴离子型和非离子型乳化剂的复配体系制得稳定性好的乳液。
当所采用的乳化剂体系的 HLB 值与单体的相符时 , 才可达到最佳效果。依据 HLB 值 , 通过一系列的试验 , 从通用的乳化剂中找到了 PS 的一个较好的乳化剂体系 , 试验结果见表 1 。
表 1 乳化剂的选择
由表 1 结果最终选择了 3 # 乳化体系。本实验如没有特殊说明 , 乳化剂的用量和比例不变。
2. 2 工艺条件的影响
聚合工艺一定程度上影响着乳液聚合结果 , 不同的反应体系应选择不同的工艺条件。聚合工艺的影响如表 2 所示。
表 2 工艺条件的影响
搅拌速度过大过小都不好 , 这与乳液聚合的基本规律一致 ; 而加入交联剂后 , 普通乳液聚合和种子乳液聚合都易产生结块 , 乳化液全部滴加时结果较好。这是因为大量的单体乳化液在交联剂的存在下引发聚合容易导致乳胶粒聚并 , 而把乳化液逐滴均匀加入反应器中 , 在适当的温度下 , 单体马上被大量反应掉 , 并把热量散开 , 这样局部不会过热而导致暴聚。部分水和乳化剂作为底料 , 一定程度上起到稀释乳液的作用 , 降低了刚开始聚合时的反应速率。因此 , 根据交联聚合反应的具体情况 , 选择了合适的工艺条件 :(1) 搅拌速度为 300 r/min, (2) 采用部分乳化剂水乳液作底料 , (3) 预乳液全部滴加 , (4) 在聚合过程中均匀滴加引发剂和缓冲剂的水溶液 , 70 ℃ 下引发聚合。
2. 3 乳化剂用量对粒径及其分布的影响
根据乳液聚合的机理可知 , 乳化剂用量决定着形成胶束量的多少 , 而胶束的量又影响最终乳胶粒径的大小及分布。乳化剂用量与乳胶粒径并不完全成正比。随着乳化剂量的增加 , 形成的胶束量加大 , 因而会生成更多的乳胶粒 , 到一定的程度时 , 随着乳胶粒径的减小粒子表面积增大 , 乳化剂补给不足 , 由于表面能的加大 , 会导致乳胶粒团聚 , 乳胶粒径反而会增大。表 3 为乳化剂用量对刚性粒子粒径及其分布的影响。
从表 3 可以发现 , 随着乳化剂用量的增加 , 刚性粒子的粒径先减小后增大 , 乳化剂用量为 5 .2% 时乳胶粒径达到最小值 , 这与理论分析相一致。因此 , 通过控制乳化剂的用量一定的程度上可以控制单位体积内乳胶粒质量以及乳胶粒径的大小。
表 3 乳化剂用量对刚性粒子粒径及其分布的影响
2. 4 引发剂用量对粒径及其分布的影响
本实验选择过硫酸钾 ( KPS) 作为引发剂 , 根据 KPS 的半衰期与温度的关系以及工艺的影响 , 选择在 70 ℃ 下进行聚苯乙烯超微刚性微球的合成。固定其他反应条件不变 , 通过改变引发剂的用量考察了引发剂对超微刚性粒子粒径及其分布的影响 , 如表 4 所示。
表 4 引发剂用量对刚性粒子粒径及其分布的影响
随着引发剂的增加 , 刚性粒子粒径逐渐减小 , 最小达到 0 .39 ~ 0 . 46 μ m ( 如图 1) , 且粒径分布也略变窄 , 然后随着引发剂用量的增加 , 粒径又增大。对比乳化剂和引发剂对 PS 有机刚性粒子粒径及其分布的影响可以发现 : 引发剂的影响更大 , 促使生成的 PS 有机刚性粒子粒径更小、分布更窄。
图 1 引发剂含量为 1 .6% 时刚性粒子粒径及其分布
2. 5 固含量对乳胶粒径及其分布的影响
乳液固含量对乳胶粒的大小及其分布的影响与乳化剂用量的影响类似 , 结果见表 5 。
表 5 固含量对刚性粒子粒径及其分布的影响
从表 5 可知 , 随着固含量的增加 , 单位体积内的乳化剂含量增加 , 形成的胶束量增大 , 引发聚合时就会形成更多的乳胶粒。因此 , 乳胶粒径先增大后又减小 , 在蒸馏水用量为 70 份时 , 乳胶粒径达到最小值。这与增加乳化剂起到相同的作用 , 因此其影响与乳化剂类似。
从上述 PS 有机刚性粒子的合成工艺讨论中可以看出 : 在 PS 有机刚性粒子的制备过程中 , 对其粒径及其分布影响最大的是引发剂和乳化剂浓度 , 且引发剂浓度和乳化剂浓度的大小对于刚性粒子粒径增大或减少的影响并不总是一致 , 有时相反 ; 有机刚性粒子粒径及其分布是与整个反应体系及其反应过程密切相关的。
2. 6 选择上述最佳条件合成有机刚性粒子
选择乳化剂和引发剂最佳用量来合成刚性粒子 , 粒径和粒径分布结果如图 2 。
从图 2 可以看出 , 选择乳化剂和引发剂最佳用量来合成的刚性粒子并没有导致粒径及其分布减小 ; 而当选择乳化剂、引发剂以及固含量三者的最佳条件来合成刚性粒子时发现有大量的结块 , 其结果并不好。这是因为随着刚性粒子粒径减小 , 表面能增大 , 导致粒子聚并。
图 2 乳化剂和引发剂选择最佳用量时刚性粒子的粒径及其分布
2. 7 交联剂的用量与交联度的关系
有机粒子只有具备一定的刚性才能用来增强塑料。但刚性又不能太强 , 这样会导致刚性粒子与基体的界面相容性变差 , 易于脱粘 , 降低了刚性粒子与基体间的相互作用。因此 , 有机刚性粒子交联度的对刚性粒子改性塑料结果的影响较大。表 6 为交联剂的加入量与交联度的关系。
表 6 交联剂的用量与交联度的关系
从表 6 数据可以得出这样的结果 , 交联剂的加入量与粒子交联度并不成线性关系。而且 , 试验中也发现 , 太多的交联剂容易导致微粒聚并。至于有机刚性粒子的最佳交联剂用量还要根据改性后复合材料的性能确定 , 同时还会受到有机刚性粒子的用量、粒径及其分布的影响。
3 结 语
(1) 引发剂和乳化剂对 PS 有机刚性粒子乳液的合成稳定性及其粒子粒径分布的影响最大。
(2) 通过控制合成工艺条件 , 可以制备 0 . 39 ~ 1 .28 μ m 范围内小粒径、窄分布的 PS 有机刚性粒子 , 最小范围可达 0.39 ~ 0 . 46 μ m 。
(3) 交联剂用量与有机刚性粒子的交联度并不完全成正比关系。
如转载, 请注明: 资料来源"中国艺术涂料网"
中国艺术涂料网“转载文章,请注明:文章来源中国艺术涂料网”
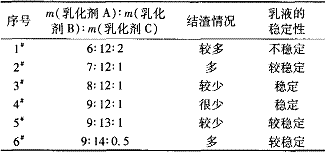
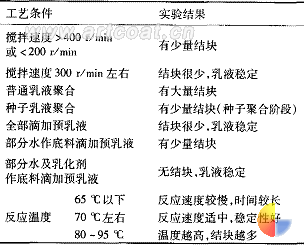
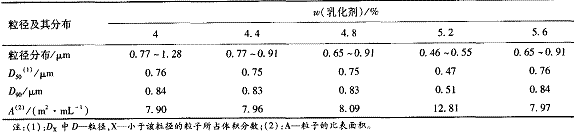
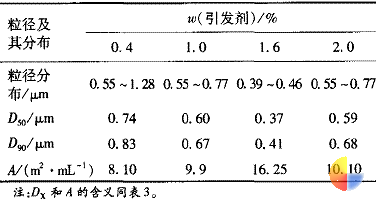
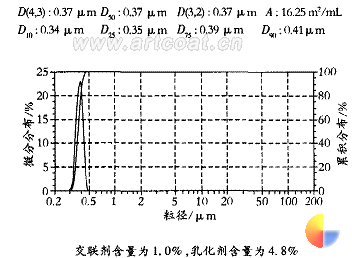
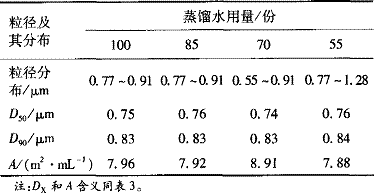
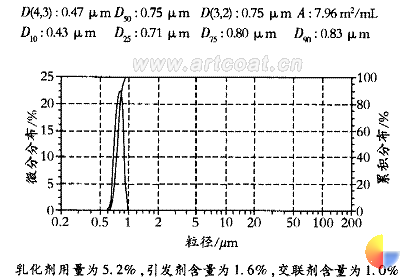

下一篇:无溶剂环氧涂料在重防腐领域的应用
相关文章
发布评论