涂料文集
丙烯酸酯水溶胶树脂的研制
于雄,张鹏 ( 四川理工学院材料与化学工程系,四川自贡 643000)
摘要:介绍了一种在酸性、碱性条件下稳定的水性丙烯酸水溶胶的制备;研究了乳化荆、引发剂、反应温度、中和刑、助溶剂等因素对水溶胶性质厦其涂膜性能的影响。
关键词:丙烯酸酯;水溶胶;水性涂料
1引言
随着人类对环境保护要求的提高,现代人对省能源、少污染、高附加值、高功能化产品的呼声日益高涨。为了人类的健康安全,在涂料领域应大力发展水性、高固体分和粉末等环保型涂料。在水性涂料中应用最多的是丙烯酸酯类,丙烯酸酯乳液的研发成功为涂料水性化奠定了基础。
水溶胶型丙烯酸系树脂是介于水溶性和乳液树脂之间的超微胶态分散体,呈半透明状,有优良的光泽。粒子微小、均匀,且含有少量极性基团和表面活性剂,相对分子质量适中,兼具水溶性和乳液树脂的性能的优点,如渗透性好、易成膜、有良好的耐水性、稳定性和流平性,因而在水性胶黏剂、涂料、油墨及其他方面有很好的发展前途。
2试验方案的设计
2.1试验配方
试验配方见表1。
2.2试验操作
将苯乙烯、丙烯酸丁酯、丙烯酸羟乙酯混合并适当搅拌,分别用10份水溶解过硫酸钾和丙烯酰胺。将K12、OP-10、聚丙烯酸钠水溶液(提前24h溶解)加入反应瓶中,搅拌加热到60℃,加入1/3溶解好的过硫酸钾、1/3亚硫酸钠、20%混合单体,在80℃下保温30min,观察到体系泛蓝,开始滴加剩余的混合单体和引发剂、丙烯酰胺水溶液,2~3h滴加完,反应温度控制在78~82℃。滴完后用30min升温到95℃,保温30min,即得淡黄色黏稠乳液,降温到69~72℃,用0.5~1h滴加中和剂三乙醇胺和乙基溶纤剂的混合物,调pH在7~8,在70~80℃保温,高速搅拌1~3h到体系呈半透明状,过滤出料。
表1 试验配方
3性能测试与结果
成膜温度:采用低温烘箱,测其成膜所需的最低温度。
干燥时间:将其涂于打磨好的试片上,测其在常温、常压下的表干时间。
固含量:测试不挥发物对树脂样品的百分含量。将其置于110℃的烘箱中干燥2h,计算固含量。
氯化钠稳定性:在水溶胶中加入其10%质量的3%氯化钠溶液,不破乳为通过。
磷酸稳定性:在水溶胶中加入其10%质量的5%磷酸溶液,不破乳为通过。
测试结果见表2。
表2 性能检测试验结果
由表2可知,3号样品在乳化剂含量较低的情况下结果比较理想。以3号样品做重复试验,测试结果见表3
表3 性能检测重复试验结果
取少量6号样品,稀释后用SPA400到扫描探针显微镜的DFM模式扫描其颗粒,其外观形貌见图1。
由图1可以看出:本方法制得的水溶胶颗粒大小较为均匀,分布在0.1μm左右,分散良好,为半透明状态;颗粒表面较为规则、平滑,说明苯乙烯和内烯酸厂酯等有着很好的共聚,实现试验没计要求。
图1 6号样品的DFM扫描
另取少量6号样品干燥成膜,用肉眼观察其外表,见图2、3。用NIKONEPIPHOT200显微镜扫描其膜表面,见图4、5。
由图2、3可以看出:涂膜韧性优,成膜完整,外观平整,无流挂现象,颜色均一,光泽良好,表面没有气泡等,视觉感官良好。由图4、5扫描图分析,高聚物在水分子的表面张力的作用下成膜致密、连续、无裂痕,表面有极少量的小孔,可能是涂膜底层水蒸气蒸发时所留下的,亦有可能是揭膜时的损伤;从涂膜微观图来看,表面亦很平整。
图2 涂膜外观
图3 涂膜外观
图4 在100倍模式下扫描效果
图5 在200倍模式下扫描效果
4讨论
4.1单体的选择
本试验选用了苯乙烯、丙烯酸羟乙酯、丙烯酰胺等单体。苯乙烯带有苯基,为硬单体,主要作用是改进涂层的硬度、耐磨性和耐冲击性等;丙烯酸丁酯为软单体,主要作用为改进涂料的柔韧性和耐久性;功能性单体,如丙烯酸羟乙酯、丙烯酰胺作为亲水单体,提供功能性基团,主要是羧基、羟基和胺基等。羟基的存在可提高交联乳液涂膜的综合性能,羧酸基团可以提高胶膜对金属的附着力,并使乳液黏度的控制较为容易。
对丙烯酸酯单体而言,增加软单体,如增加丙烯酸丁酯用量,会提高涂层的耐水性;但另一方面,软单体用量过大,也会使乳液聚合反应受到影响r”。通常会使乳胶粒子的粒径增大,粒径分布变宽,成膜性能有所降低,而成膜性能的好坏必然影响涂层的耐候性等性能。因此,只有适当调整软、硬单体的比例,才能得到耐冲击性好、成膜性好的涂层。本试验选用的软、硬单体比以1:1~1:1.2为宜。
4.2反应温度对产品性能的影响
水溶胶涂料的性能主要取决于所用基料的性能,反应温度对其合成也有一定的影响。为了使反应稳定,提高转化率,需要控制好反应温度,其初期反应温度为80℃,在滴加完单体后需升温反应,因为反应是放热反应。所采用的温度不同,其结果也有所不同。表4即为温度对产品性能的影响。
表4反应温度对产品性能的影响
4.3乳化剂对水溶胶合成的影响
在乳液聚合中,乳化剂降低单体和水的表面张力,增加单体在水中的溶解度,形成胶束和乳化的单体液滴,乳化剂体系及用量对合成水溶胶的稳定性及质量有很大影响。对于水溶胶合成,在不影响乳液稳定性的前提下应尽量减少乳化剂,增加水溶胶的透光性。一般表明将2种乳化剂复配使用所形成的混合胶束,其乳化稳定性和乳化效果比单用一种乳化剂所研制的乳液性能更为优良。因为这两者合理并用或作为复合物使用,可使两种乳化剂分子交替吸附在乳胶粒的表面,降低同一胶粒上离子间的静电斥力,增强乳化剂在胶粒上的吸附牢度,降低乳胶粒表面的电荷密度,使带负电的自由基更易进入乳胶粒中,提高乳液聚合速度J。在本试验中,乳化剂体系选用阴离子型乳化剂(K12)和非离子型乳化剂(OP-10)复配,能在聚合物粒子表面形成吸附层,阻挡聚合物粒子问融合,以提高聚合物粒子的分散稳定性。适当调节2种乳化剂用量比,可以得到符合要求的乳化剂体系,为水溶胶的合成及稳定性提供了良好的条件。在乳化过程中应加大搅拌强度。乳化剂用量对水溶胶合成的影响见表5。
表5 乳化剂用量对水溶胶合成的影响
4.4氨化反应对粒径的影响
在水溶胶的制备中,氨化反应是获得高质量水溶胶的关键步骤之一。由于聚合物粒内部和表面存在羧酸基团,通过一定温度下的氨化反应,可使胶粒表面逐步水溶化,并经机械剪切,达到减小粒径的目的。增大聚合物的水溶性,提高聚合物的自乳化能力。中和剂一般采用弱碱性物质,如氨水、三乙醇胺等,其用量通过计算控制在能中和共聚物分子链上80%~100%的羧基,使水溶胶能稳定分散。试验比较了两种中和剂:氨水和三乙醇胺的中和效果,结果见表6。
表6 中和剂对水溶胶及其涂膜性能的影响
4.5搅拌强度对产品质量的影响
在乳液聚合中,在稳态范围内搅拌转速大,单体被分散成更小的单体珠滴,每1cm3水中单休珠滴的表面积就更大,致使1cm3水中胶束数目减少,故生成的乳胶粒数减少,所以初始单体量一定,乳胶粒径就会减小。但过于激烈的搅拌,会使乳液产生破乳,从而失去稳定性。
5结论
本试验采用单体预乳化工艺,以苯乙烯、丙烯酸丁酯、丙烯酸羟乙酯为单体制备水溶胶,软、硬单体比为1:1.1,引发剂用量为单体的0.5%,乳化剂用量为2.5%,阴离子型乳化剂与非离子型乳化剂比为1.7:0.8。采取以上工艺可以制出透光性佳、稳定性好,成膜性能优良的丙烯酸水溶胶。
资料来源: hc360慧聪网
从表6可以看出,用三乙醇胺作为中和剂制得的水溶胶清澈、透明。而用氨水制得的水溶胶则带黄色,黏度较大。 当乳化剂用量较少时就会发生破乳,而较高时泡沫就会增加很多。当非离子型乳化剂量大于阴离子乳化剂时,对水溶胶合成有很好的效果,其表现在反应中蓝光出现时间早,蓝光足,说明乳胶粒径小,乳胶较稳定。 由表4可以看出,反应温度低,反应不够完全,转化率低,因此固含量低,势必使黏度降低,温度宜稍高,能使反应完全。但温度过高,会局部受热,反应物有时会暴聚,而伴有大块凝胶出现,反应很难控制,笔者在试验中就多次出现暴聚现象。因此78~84℃为适宜的反应温度,并注意回流。
黏度:采用NDJ-1旋转黏度计测其剪切黏度。中国艺术涂料网“转载文章,请注明:文章来源中国艺术涂料网”
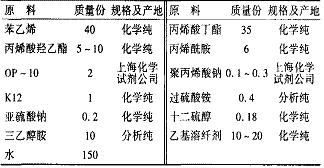
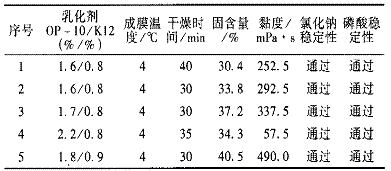
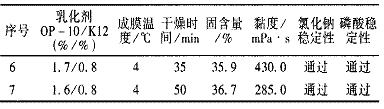
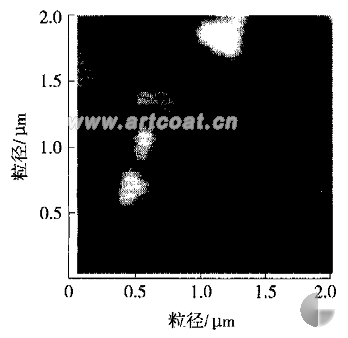
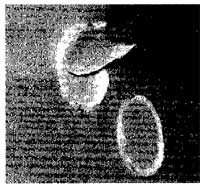
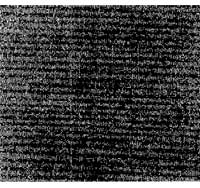
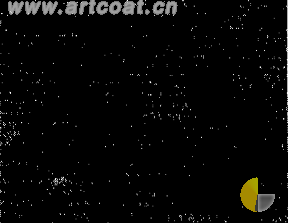
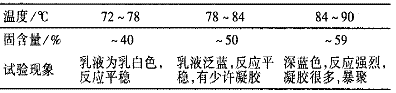
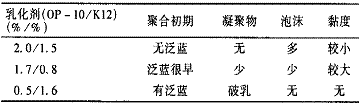
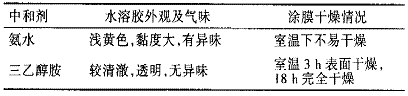
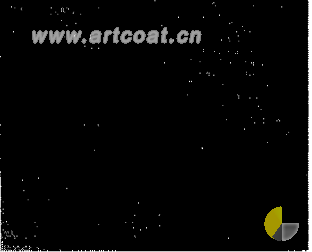
下一篇:WFZ-151粉末腻子的性能研究
相关文章
发布评论