涂料文集
高原高寒地区桥梁钢构件防腐涂料试验和涂装工艺
黄直久 邸建玄 李昌生 ( 中铁十二局集团有限公司 , 太原 030024) 季瑞峰 ( 海洋化工研究院 , 青岛 266071)
摘要 : 阐述了高原高寒地区桥梁钢构件所用防腐配套涂料的试验情况 , 并通过现场施工 , 建立健全了相应的施工工艺和质量控制措施。试验证明该配套涂层具有长效的防腐性和耐候性 , 可在高原高寒地区进行推广应用。
关键词 : 高原高寒地区 ; 防腐涂料 ; 配套涂层 ; 涂装工艺
1 前 言
青藏铁路地处高原高寒地区,周围环境气候恶劣,且紫外线照射强烈,昼夜温差大,风沙侵蚀严重,从维修养护困难和建立长效防护的角度出发,TB/ T1527 -1995 《铁路钢桥保护涂装》中规定的我国现有的四套铁路钢桥保护涂装体系,已无法满足在特殊的高原气候环境下使用的要求。随着新技术和新材料的不断出现,桥梁设计部门根据国内外的应用经验和施工案例,经过充分的调研, 对青藏铁路桥梁钢构件的涂装采用了新的防腐体系。该体系与现有钢桥保护涂装相比,底漆采用防锈性能优良的韩国生产的水性无机硅酸锌涂料;面漆采用室温固化的超耐候氟碳涂料 ;中间层仍为环氧云铁中间漆,该体系具有更长久的防腐性和耐紫外线性。鉴于该套涂装体系在铁路工程中尚无现行的行业标准,也没有在工程中配套应用的经验,青藏铁路工 程建设总指挥部委托中铁十二局集团有限公司和化学工业海洋涂料质量监督检验中心,于 2003年7月至2004年2月, 进行了室内原材料、复合涂层 试验和现场钢构件的防腐涂装工艺试验。试验的目 的是在原设计采用的材料种类及配套组合方案基础上,进一步进行的验证选择,以便确定适用于该套 防腐涂装体系的原材料和施工参数,建立该套防腐 涂装体系的施工工艺、技术条件及质量控制措施。 国内外重防腐涂料的应用和配套资料表明,水性无机富锌涂料与环氧云铁中间层和氟碳涂料的配套体系已被公认为目前最佳的重防腐涂料涂装体系。
2 涂料与涂装体系配套试验
2 . 1 涂料检验
2 . 1 . 1 涂料
(1) 底漆— 水性无机硅酸锌涂料 (IC531) 。
(2) 中间漆环氧云铁中间漆。
(3) 面漆—氟碳面漆。
2 . 1 . 2 涂料的复验
按照供应商提供的产品技术要求 , 参照 TB/ T2772 -1997 《铁路钢桥用防锈底漆供货技术条件》 和 TB/ T2773 -1997 《铁路钢桥用面漆供货技术条 件》 , 对产品进行复验 , 其结果见表 1 、表 2 、表 3 。
表 1 IC 531 水性无机硅酸锌涂料
表 1 IC 531 水性无机硅酸锌涂料
表 2 环氧云铁中间漆
表 2 环氧云铁中间漆
表 3 氟碳面漆
表 3 氟碳面漆
由表 1 、表 2 、表 3 可以看出 , 三种涂料的复验结果均符合相关技术指标要求。
2 . 2 复合涂层试验
根据氟碳面漆的种类 , 涂装两套复合涂层样板 , 第Ⅰ 套为 IC 531 底漆 75 μ m (2 道 ) — 环氧云铁中间漆 60 μ m (2 道 ) — 高飞氟碳漆 60 μ m (2 道 ); 第Ⅱ 套为 IC 531 底漆 75 μ m (2 道 ) — 环氧云铁中间漆 60 μ m (2 道 ) — 旭硝子氟碳面漆 60 μ m (2 道 ) 。
针对青藏高原紫外线照射强烈、昼夜温差大和强烈的风沙磨蚀的恶劣环境 , 经过全面的考虑 , 对现场制作的复合涂层样板主要进行如下几项具有代表性的试验 :
① 3 000h 人工加速老化试验 ( 紫外老化 );
② 50 次高低温循环试验 (-40 ~ + 60 ℃ );
③ 耐磨试验 ( 参照 GB/ T9261 -1988 《甲板漆通用技术条件》中耐磨试验的技术要求 , 700g / 500r , 失重小于 100mg) ;
④ 1 000h 的耐盐雾试验 , 以考查其防腐耐久性能。
方案Ⅰ 、Ⅱ 样板的制作均在高原施工现场 , 按照钢构件施工工艺 , 与钢构件同时进行表面处理和喷涂 , 然后送至化学工业海洋涂料质量监督检验中心进行检验 , 其结果见表 4 。
表 4 复合涂层样板检验结果
表 4 复合涂层样板检验结果
表 4 复合涂层样板检验结果
由表 4 的检验结果可以看出 , 两种复合涂层样板经 50 次耐高、低温冻融试验后,与标准样板对比基本无变化 , 说明复合涂层对温度变化的影响较小, 耐磨试验磨耗量均小于 20mg,大大低于甲板漆的技术要求,说明该复合涂层硬度较高 , 不易磨损;两套方案的底漆与中间层的涂料均相同,耐盐雾试验的结果一致,经 1000h 的盐雾试验后表面基本无变化, 划痕处有轻微锈痕, 漆膜表面无起泡现象 , 说明底漆具有较好的阴极保护和防腐性能 , 涂层配套优良 ; 人工加速老化试验进行到 1000h时, 第Ⅰ 套和第Ⅱ 套基本无变化,当进行到 1500h 时, 第Ⅰ 套开始出现失光和变色 ,到 3000h 时, 第Ⅰ 套已出现明显的失光和变色,而第Ⅱ 套仅出现 轻微的失光,基本不变色。单从人工加速老化试验的结果可以判断,第Ⅱ 组合方案的抗紫外线性明显 优于第Ⅰ 套,耐候性优异。综上所述,第Ⅱ套优于第Ⅰ套,相对完好。
在高原环境差的条件下 , 为保证施工质量 , 建 立了喷砂房、喷涂车间 , 配置了喷砂喷涂设备和必 要的检测仪器 ( 干湿膜测厚仪、温湿度仪、划格 器、粗糙度测定仪等 ) 。喷砂房施工对防护要求较 高 , 帐篷内四周采取了围钢板和装贴橡胶板的防护 方法 , 同时在平整硬化的地面上铺设钢板 , 防止高 压风砂对地面和帐篷的破坏。喷漆施工环境温度控 制在 (5 ~ 30) ℃ , 相对湿度小于 80 % , 施工时采 用燃煤锅炉供暖和通风机排烟尘。房内设挂杆、吊 钩 , 挂杆选用Φ 38mm 钢管 , 设置高度 1 . 6m , S 形 吊钩用 25cm 、长Φ 12mm 钢筋弯制 , 每 (30 ~ 50) cm 设 1 个。对于栏杆扶手角钢等长大构件 , 可以 搭焊简易支架 , 将其整齐排放进行喷涂。
4 钢构件施工工艺试验
4 . 1 喷砂试验
(1) 喷砂材料的选择
对 16/ 35 普通硅砂、 16/ 35 石英砂及 G-40 粗 钢砂三种砂进行喷砂对比试验 , 试验结果为 : 采用 普通硅砂平均每小时可喷人行道支架 (6 ~ 10) 个 , 采用钢砂可喷 (14 ~ 16) 个 , 石英砂可喷 (20 ~ 24) 个。由此可见 , 石英砂的效率最高 , 但石英砂 不能重复利用 , 且粉尘较大 ; 钢砂尽管成本高 , 但 可多次回收重复利用 , 硬度高 , 喷砂效果好 , 故主 要选用钢砂作为喷砂材料。
(2) 喷砂工艺
试验中选用电动遥控固定式磨料筒作为砂罐 , 容积 1m 3 ; 空压机选用 (6 ~ 12) m 3 的空压机 , 工 作压力 0 . 7MPa 。为提高喷砂效率 , 先将待喷涂构 件在地面上整齐摆放 , 然后打开空气控制阀、砂 阀 , 将高压砂颗粒喷射到钢构件表面 , 进行人工换 面 , 换面后再喷砂 , 特别注意构件死角及焊缝部 位。一批喷完后 , 进行下一批构件喷砂施工。除锈质量按《涂装前钢材表面锈蚀等级和除锈等级》 ( GB/ T8923 -88) 进行检验 , 不低于 Sa2 . 5 级。按《表面粗糙度比较样块 , 抛 ( 喷 ) 丸、喷砂加工表面》 ( GB/ T606005 -86) 标准进行喷砂粗糙度检验 , 达到 Rz (25 ~ 60) μ m 。
4 . 2 涂装工艺试验
喷漆施工时环境温度控制在 (5 ~ 30) ℃ 、相对湿度低于 80 % , 将喷砂完毕的钢构件分批吊装整齐 , 用高压风吹去表面浮尘 , 有油污时必须彻底清除干净 , 依次进行底漆、中间漆和面漆的涂装 , 各道喷涂严格按照工艺进行。
涂装工艺试验时 , 先进行了构件涂装试喷 ( 先各选 10 套钢构件 ), 再按相同方法现场制作标准样板 , 涂装试喷 , 然后选用第Ⅱ 套方案 , 对第六、十一标段人行道支架喷涂 25 900 件 ( 约 870t) 、避车台 350 件 ( 约 140t) 钢构件进行防腐涂装施工。通过涂装工艺试验 , 完成了前期人行道支架及避车台构件的防腐涂装施工 , 同时又进一步总结完善了第Ⅱ 套组合涂装方案的施工工艺及质量控制方法。
5 质量控制
5 . 1 表面喷砂处理
(1) 喷砂要全面彻底 , 不留死角 , 除锈质量按 GB/ T8923 -88 《涂装前钢材表面锈蚀等级和除锈等级》和 GB/ T6060 . 5-86 《表面粗糙度比较样块 , 抛 ( 喷 ) 丸、喷砂加工表面》标准进行检验。
(2) 涂装前用干净的压缩空气将表面的灰尘和砂粒吹净 , 如有油污 , 必须彻底清除 ( 用碱性或中性溶液 , 禁止用有机溶剂 ) 。
(3) 经表面处理后的钢构件在 8h 内涂装 IC 531 底漆 , 避免钢构件表面发生氧化。
5 . 2 IC 531 底漆涂装
(1) 用电动高速搅拌按规定比例混合底漆 , 并进行熟化 , 再用专用喷涂设备进行喷涂。
(2) 喷涂前测温度和湿度。底漆一般两次喷涂达到设计厚度。 IC 531 底漆两次喷涂时的时间间隔尽量减少 , 采用湿盖湿喷涂。
(3) 底漆涂装完毕并硬干后 , 检查涂层厚度。干膜厚度不够需要补涂 , 待涂表面如被污染必须打磨。
(4) 按《铁路钢梁保护涂装》 ( TB/ T1527 -1995) 第 3 . 2 . 3 . 1 及第 3 . 2 . 3 . 2 条检测涂层外观 , 涂层外观均匀平整 , 不允许有剥落、起泡、裂纹、气孔现象。
(5) 按《色漆和清漆漆膜的划格试验》 ( GB/ T9286 -98) 检查涂层附着力 : 划格法≤ 2 级 , 单层底漆的划线间距为 2mm 。
5 . 3 环氧云铁中间漆涂装
(1) 待底漆涂装完毕后 (24 ~ 168) h , 方可进行中间漆的涂装。
(2) 油漆和固化剂按比例混合后 , 充分搅拌均匀并熟化 0 . 5h 。
(3) 第一道中间漆涂 20 μ m 左右 , 加稀释剂 30 % ~ 40 % 。
(4) 两道中间漆施工时间间隔为 (6 ~ 168) h 。
(5) 涂层外观检查及涂层厚度测量 , 同底漆质量检查方法。
(6) 涂层附着力检查 : 划格法≤ 2 级 , 复合涂层的划线间距为 3mm 。
5 . 4 氟碳面漆的涂装
(1) 中间漆涂装完毕后 (24 ~ 168) h , 方可进行氟碳面漆的涂装。
(2) 将油漆和固化剂按比例混合后 , 充分搅拌均匀并熟化 0 . 5h 。
(3) 两道面漆施工时间间隔为 (4 ~ 168) h 。
(4) 涂层外观检查及涂层厚度测量 , 同底漆质量检查方法。
(5) 涂层附着力检查 : 划格法≤ 2 级 , 复合涂层的划线间距为 3mm 。
5 . 5 钢构件的标识、堆放、运输、安装防护
(1) 喷砂及涂装过程中 , 要表明各批构件数量、使用部位、上道工序名称、下道工序施工时间、下道工序名称等内容。
(2) 喷涂完的支架要选择位置较高的场地堆放 , 下面要垫起防潮 , 上面要覆盖并捆绑压实。
(3) 运输、安装施工过程中要轻搬轻放 , 防止损伤涂层。
(4) 如安装过程中有碰伤 , 应先清理表面 , 再补涂。
6 安全注意事项
(1) 喷砂施工人员要配备全套防护衣、防护镜 , 防止伤人事故发生。
(2) 喷漆施工中产生的有害气体对人体健康危害较大 , 需做好通风换气工作。
(3) 施工用电要注意配齐电闸盒 ( 箱 ), 经常检修电路 , 防止触电事故发生。
(4) 涂装现场严禁烟火。
(5) 各现场配有医务人员和必要的氧气、急救药品 , 做好高原病防治和突发事件的救治工作。
7 结论与建议
(1) 工艺试验两套组合方案选用涂料基本合理 , 所检项目的性能均符合技术要求 , 各组合方案所用涂料配套性良好 , 第Ⅱ 套样板耐紫外线性能优异。
(2) 涂装工艺试验施工中选用的施工设备及检测设备可满足施工要求 , 经过工艺试验和大量的构件涂装施工 , 进一步完善了施工工艺 , 健全了质量控制措施。
(3) IC 531 底漆对钢梁及钢构件表面处理要求十分严格 , 施工中必须加强质量监控 , 严格进行每一道工序的检查验收。
资料来源: hc360慧聪网
3 施工设施 中国艺术涂料网“转载文章,请注明:文章来源中国艺术涂料网”
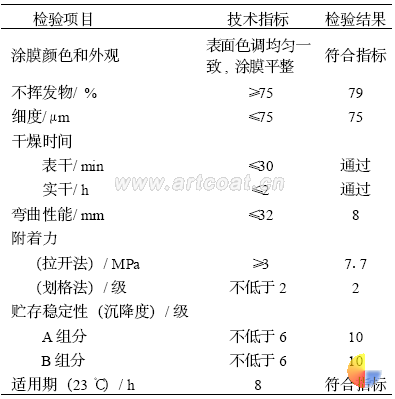
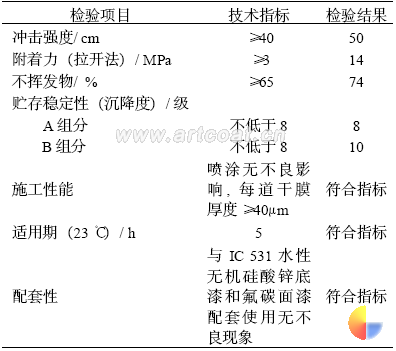
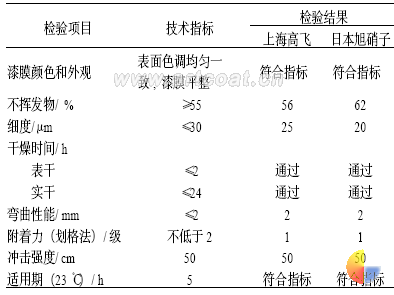
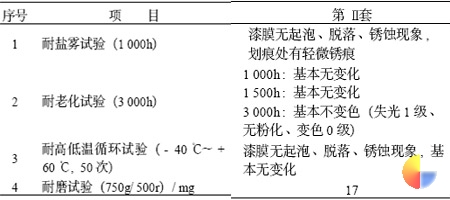
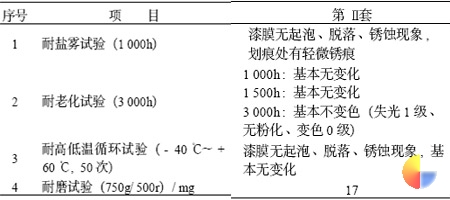
下一篇:E-20环氧树脂耐磨涂料的研制
相关文章
发布评论