涂料技术
脂肪酸酯在制漆中的应用
作者:王其超 , 马喜顺 , 黄新竹 , 陈广明 , 孙胜民 ( 石家庄市油漆厂 )
[据涂料涂装资讯网报道]摘 要 : 本文简述了脂肪酸酯的历史 , 提出了将此原料应用于制漆时应采用的方法 , 分析了这种方法的可行性。例举了用脂肪酸酯制备白色氨基烘漆、蓝色聚氨酯漆及浅灰色自干醇酸磁漆的配方及涂料性能。
0 引 言
人们采用植物油 ( 包括不干性油、半干性油和干性油 ) 制漆已有十分悠久的历史。近几年来 , 采用油酸、合成脂肪酸制漆已成为发展趋势。随着工业化产品的丰富 , 植物油经过提纯、精制等特殊处理越来越多地用在食用油中 , 如色拉油、调和油。植物油在贮存、运输中 , 因时间过久或受环境因素影响会降解、酸败或轻微聚合 , 颜色加深 , 酸值升高 , 杂质增多 , 我们称此为酸化油 ; 其中也不乏来自各种渠道的二次回收的油。将酸化油直接用于制漆常用两种方法 : 其一是脂肪酸 - 油法 , 其二是酯交换反应 , 但酯化反应后期稠度增长过快 , 不易控制 ; 且这两种方法制得 - 半成品树脂颜色很深 , 最深达 18 # ( Fe 2 Co) 色 , 制漆后外观不佳。为此 , 有些涂料原料供应商将酸化油经过预处理、脱胶、脱色、酯交换、蒸馏等步骤去掉杂质 , 制成脂肪酸酯 , 其主要是脂肪酸甲酯 , 颜色很浅 , 小于 3 # 色。混合脂肪酸甲酯的成分见表 1 。
表 1 混合脂肪酸甲酯的成分 ω /%
1 脂肪酸酯的制备
1. 1 原理
最为常用的是由酸化油与甲醇反应生成脂肪酸甲酯 , 酸化油通常含有油脂和油酸 2 种成分 , 它们均要与甲醇反应 , 实质上是酸化油的单元醇 - 醇解 , 反应如式 1 。
1. 2 影响脂肪酸酯制备的因素 [ 1]
1. 2. 1 预处理
制备之前必须将酸化油用硫酸脱胶 , 硫酸的用量为 0 . 5% ~ 1% ( 质量分数 ) 。质量差的酸化油可以增加硫酸用量 , 硫酸的用量不可过多 , 过多引起磺化等副反应。如果酸化油颜色较深 , 要用活性白土脱色。甲醇最好是无水的 , 含水时则抑制脂肪酸甲酯生成速度。
1. 2. 2 催化剂
甲醇钠是很好的催化剂 , 可将固体氢氧化钠溶于无水甲醇得到甲醇钠 , 一般苛性钠的用量为甲醇的 0 .2% ~ 1. 5% ( 质量分数 ) , 甲醇钠不易长期放置 , 因其易与空气中的 CO 2 及水反应 , 降低催化效率。
1. 2. 3 反应条件
甲醇用量一般为理论量的 1 .6 倍 , 即甲醇比酯化所用脂肪酸基过量 , 反应温度一般在 70 ~ 80 ℃ , 甘油作为反应副产物因与脂肪酸酯混容性不佳而沉降下来。
2 脂肪酸酯在制漆中的应用
脂肪酸酯用于制漆主要是脂肪酸 18 碳链结构组分 , 按碘值高低分为半干性脂肪酸酯 (B) 和不干性脂肪酸酯 (A) 。此材料直接用于合成树脂的不足之处是其结构中的羧基已被甲醇的羟基酯化掉 , 在制备中必须采取适宜的酯交换剂在适宜的反应温度 ( 一般为 210 ~ 235 ℃ ) 下 , 将甲醇置换出来 , 并将甲醇冷凝、收集。剩余的脂肪酸与甘油或季戊四醇形成多元醇单酯 , 继而与有机多元酸 ( 如苯酐、顺丁烯二酸酐 ) 缩聚 , 制成树脂半成品。根据脂肪酸酯碘值不同 , 可分别用于聚氨酯漆、氨基漆 ( 如用 A 类 ) 和自干漆 ( 如用 B 类 ) 。
2. 1 树脂合成的反应原理 [ 2]
脂肪酸酯与多元醇在加热状态下 , 采用酯交换剂 , 一般有 2 种酯交换剂 , 其一是金属氧化物催化剂 , 其二是金属有机化合物催化剂 , 发生酯交换反应 , 本试验中采用的是金属有机化合物 MeY, 反应式如式 2:
其中 Me: 金属元素 ; Y: 有基基团 ; R: 有机脂肪链。 ( 式 2)
生成的 CH 3 OH 在高温反应条件下为气态逸出 , 通过横式冷凝器、水分离器回收 , 从而避免对人的伤害和环境污染。催化剂 MeY 在酯交换中形成金属脂肪酸盐 , 再与多元醇交换基团形成 MeOH 结构 , 继续发生 ( Ⅲ ) 式反应又重新恢复原来的结构 , 推动酯交换向均相平衡移动 , 继而与多元酸酯化、缩聚。
2. 2 短油度不干性醇酸树脂的合成
2. 2. 1 原料及配方
不干性短油度醇酸树脂 CA - 01 所用原料及配方见表 2 。
2. 2. 2 制备工艺
将脂肪酸酯 A 、甘油投入四口反应瓶 , 搅拌并升温到 125 ~ 140 ℃时加入催化剂 1, 继续升温 , 同时打开冷凝器冷却水 , 升温到 223 ~ 230 ℃ 并保温 1 h 左右 , 注意收集升温及保温阶段馏出物 , 当馏出物达到或略超过理论值时 , 测试合格后降温 , 加入苯二甲酐及回流二甲苯溶剂 , 保持酯化反应 , 温度控制在 190 ~ 200 ℃ 间 , 指标合格后降温、兑稀 , 备用。
配方 src="/uploadfile/201008/20100827010201737.gif" border=0>
表 2 CA - 01 配方
2. 3 羟基醇酸树脂 SA - 01
方法参照 2. 2, 不同的是物料配比有所变化 , 根据性能需要适当添加少量苯甲酸、顺丁烯二酸酐。
2. 4 自干性醇酸树脂的合成
2. 4. 1 原料及配方
自干性长油度醇酸树脂 C - 01 的原料及配方见表 3 。
表 3 C - 01 配方
2. 4. 2 制备工艺
将脂肪酸酯 B 投入四口瓶 , 升温并开搅拌 , 升温到 125 ~ 140 ℃时加入催化剂 2, 再升温到 230 ℃ 加入季戊四醇 , 升温到 227 ~ 234 ℃并保持 50 min, 注意观察馏出物的多少 , 当接近或略低于理论值时 , 测试合格后 , 降温 , 加入有机酸酐、回流溶剂 , 并于 200 ℃ 保持酯化 2 ~ 3 h 后逐步升温到 230 ℃ , 指标合格后降温 , 兑入松香水 , 调整指标 , 备用。
2. 5 色漆
2. 5. 1 白色氨基烘漆的配制白色氨基烘漆配方见表 4 。
2. 5. 2 蓝色聚氨酯漆的配制
蓝色聚氨酯漆配方见表 5 。
表 4 白色氨基烘漆配方
表 5 蓝色聚氨酯漆配方
2. 5. 3 浅灰自干醇酸磁漆
浅灰自干醇酸磁漆配方见表 6 。
表 6 浅灰自干醇酸磁漆配方
3 结果与讨论
3. 1 涂料及涂膜性能
上述 3 种色漆测试结果如表 7 所示。
由表 7 可见 , 白色氨基烘漆综合性能优异 , 符合行业标准 HG/T2594 — 1994, 耐冲击性 50 cm , 60 °光泽≥ 93 。蓝色聚氨酯磁漆综合性能优异 , 开罐效果佳 , 符合行业标准 HG/T2660 — 1995 。浅灰色自干漆除表干略慢外 , 其余性能符合行业标准 HG/T2576 — 1994
表 7 3 种色漆测试结果
3. 2 树脂半成品颜色问题
如果酸化油不经酯化处理 , 直接用来合成树脂 , 颜色很深 , 可达铁 - 钴比色计中最深色号 18 # , 甚至还要深 , 并且缩聚反应后期极不易控制 , 易胶化 ; 将酸化油处理得脂肪酸酯后 , 就可以在处理过程中 , 除去易产生副反应的杂质 , 再合成树脂 , 颜色可浅至 11 ~ 12 # , 可用于要求不高的白漆或浅色漆。如果将酸化油直接加入脱色剂 , 则脱色效果很不理想。
3. 3 白色氨基烘漆的耐候性
将白氨基烘漆样板放置室外 , 在阳光充足地方自然曝晒 , 3 个月后略有失光 , 无开裂。经分析 , 是树脂合成时金属催化剂所致 , 调整酯交换催化剂用量从 0 . 95% 降至 0 .045% ~ 0. 052% 后 , 失光现象大为缓解。然而酯交换剂用量也不是越少越好 , 因为当用量继续减少时 , 前期酯交换不充分 , 后期缩聚反应无法正常进行 , 因此要平衡考虑。
3. 4 浅灰自干漆的表干问题
在制漆过程中多次发现脂肪酸酯用于自干漆中表干问题较难解决 , 表干较慢 , 基本上当表干完成时 (9 h 左右 ) , 实干已基本完成。这可能是由于树脂合成第一步酯交换时虽已将副产物馏出 , 但尚有微量脂肪酸酯未反应完全 , 而随着第二步反应进行溶于醇酸树脂中 , 难于挥发的少量脂肪酸酯在形成涂膜时 , 充当了外增塑剂 , 致使表干延缓。虽尝试继续将树脂合成第一步反应更加充分 , 以期加快表干 , 但效果不十分理想。
3. 5 蓝色聚氨酯磁漆的性能
将 SA - 01 与以往羟基醇酸树脂 ( 如蓖麻油、蓖麻油酸醇酸树脂 ) 对比 , 分别与 TD I - TMP 加成物配漆 , 用 SA - 01 制得的涂料其样板的鲜映性 (DO I) 和耐候性均很好 , 这主要是在合成树脂阶段添加的酯交换催化剂滞留于树脂中 , 对后来配漆— OH 与— NCO 的交联起促进作用 , 使交联更加充分、高效。
4 结 语
用脂肪酸酯分别合成了短油度不干性醇酸树脂、羟基醇酸树脂及自干性醇酸树脂 , 并以此配制了白色氨基烘漆、蓝色聚氨酯磁漆及浅灰色自干漆。经性能检测基本符合行业标准 , 为拓展脂肪酸酯的应用进行了有益的尝试。
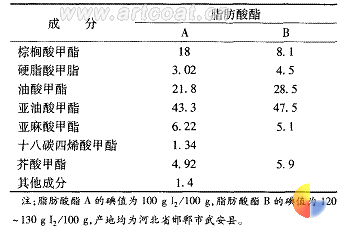
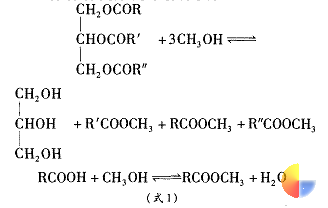
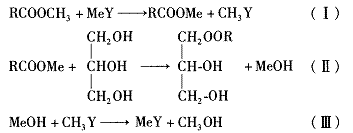
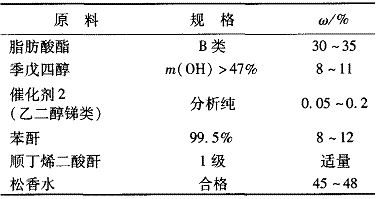
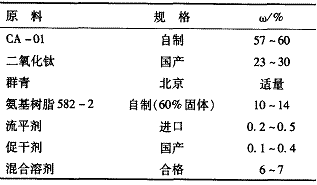
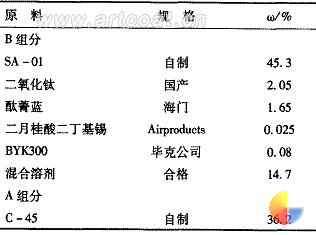
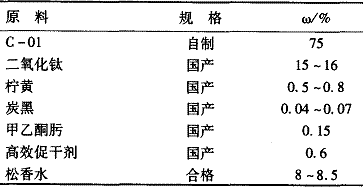
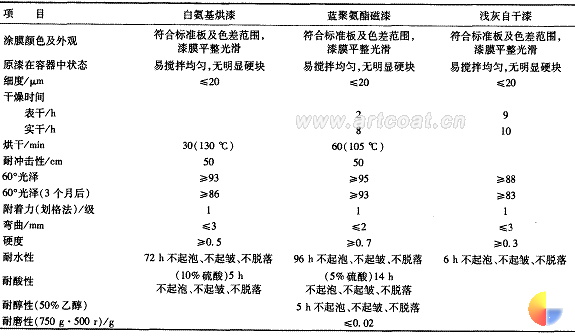
相关文章
发布评论