涂料技术
液化天然气船压载舱涂装工艺
作者:贾恒涛 王毅军 ( 沪东中华造船集团设计二所,上海 )
[据《上海涂料》报道]摘要:介绍了 147 210 m3 液化天然气船压载舱涂装工艺,讨论了不同液化天然气船压载舱的涂装方案。
关键词:液化天然气船;压载舱;涂装工艺
O 概述
沪东中华造船集团建造的 147 210 m 3 液化天然气 (LNG) 船是国内首次建造的 LNG 船,用于装载 -163 ℃ 液化天然气。由于该船是典型的“三高” ( 高难度、高要求、高附加值 ) 船舶,而且使用寿命 要求长 ( 设计寿命长达 4O 年 ) ,这就给涂装质量,尤其是压载舱的涂装质量提出了很高的要求。该船压 载舱的涂装有如下特殊性:①涂装面积大,超过 15 万 m2 ,涂装工作量大;②液货舱绝缘层基座烧焊影响压载舱涂层质量,压载舱涂装工艺复杂;③质量 要求高,涂装配套和涂装工艺要遵循 TSCF 准则 ( 压 载舱涂装配套和表面处理准则 ) ;④压载舱涂层设 计寿命长达 25 年。
1 压载舱涂装配套
该船共有 13 只压载舱,舱容约为 56 080 m 3 ,面积约为 154 460 m 2 ,采用上海国际油漆公司生产的涂层配套:
Intershield 300 ENA300 / A( 青铜色 ) 150 μ m
Intershield 300 ENA301 / A( 铝色 ) 预涂
Intershield 300 ENA300 / A( 青铜色 ) 预涂
Intershield 300 ENA301 / A( 铝色 ) 150 μ m
Intershield 300 是一种浅色纯环氧耐磨漆,具有 B 1 级压载舱涂料证书 ( 经 DNV / Marintek 测试 ) 。最低膜厚要求:在所有测量点中, 85 %的测量点的干膜厚度要达到规定膜厚,其余 15 % 的测量点的干膜厚度至少要达到规定膜厚的 85 %。最高膜厚要求:按油漆商推荐。
2 压载舱涂装工艺
2 . 1 钢板预处理
2 . 1 . 1 氧化皮去除
钢板必须没有轧制杂物、迭片、飞溅等,如果有,必须在钢板预处理前清除。钢板的腐蚀程度不能超过 B 级板 (ISO- 8501 . 1 — 1988) ,并且没有点 蚀发生。
在除锈之前,钢材表面需进行清理、干燥,去除油脂、腐蚀盐和硫酸盐。
所有要进行涂装的 6 mm 及以上厚度的钢板和型钢,都要进行抛丸除锈,达到 ISO-8501 . 1 — 1988 标准 Sa 2 . 5 级,其表面粗糙度要达到 4O ~ 75 μ m 。小型钢质件的表面 ( 例如小管径的管子,管子支撑件,基座等 ) 一般进行化学清理或动力工具清理,如用动力钢丝刷或动力砂纸盘去除表面锈蚀和松动的氧化皮。但不管用什么预处理方法,在涂装前,其表面粗糙度至少要达到 30 μ m 。
2,1 . 2 车间底漆
涂装车间底漆前,钢材表面含盐量不大于 80 mg / m 2(ISO 85O2 — 9)
在抛丸除锈之后,应立即涂装无机硅酸锌车间底漆。
2 . 2 结构性处理
结构性处理等级为 P2(ISO 8501 — 3) ,结构自由边倒圆到 r= 2 mm 。
2 . 3 分段阶段二次除锈
所有焊缝和车间底漆烧损区域喷砂至 sa 2 . 5 级,其表面粗糙度要达到 40 ~ 75 μ m 。剩下完整车间底漆的表面用扫砂的方式清除原底漆 70 %。
2 . 4 分段涂装
在涂装或复涂之前,去除所有表面污染物,如盐分、油脂和灰尘等,钢材表面含盐量不大于 80 mg / m2(ISO 8502 — 9) ,灰尘为 2 级 (ISO 8502 — 3) ,为了达 到要求,分段应尽量在涂装房内进行涂装,如选择 在室外涂装,必须采取合适的措施,以确保被涂表面不被污染,在整个清洁、油漆、处理和干燥过程中,要注意控制湿度和通风。
全面喷涂第 1 道漆,膜厚为 150 μ m ,第 1 次全面涂装后,对开孔自由边缘等难以涂装和膜厚难以保证的部位进行第 l 道预涂装,然后再进行第 2 道预涂装,最后进行第 2 道全面喷涂,膜厚为 150 μ m 。涂层总膜厚不得低于 255 μ m 。
2 . 5 合拢后的二次除锈
所有船体大接缝喷砂至 sa 2 . 5 级,对于其余大 面积烧损处喷砂至 sa 2 . 5 级,局部小面积烧损处打 磨至 St 3 级。应当指出的是,由于液货舱绝缘层基座烧焊是在合拢后进行的,焊接时钢板背面 ( 压载 舱侧 ) 的温度达到 145 ~ 210 ℃ ,已经超过了压载舱涂层环氧涂料的耐温极限,所以此处的压载舱烧损涂层需重新喷砂至 sa 2 . 5 级,然后进行涂装。为了既能提高喷砂效率,又要减少喷砂作业对周围涂层 的破坏,我们采用了小型喷砂设备。
2 . 6 损坏处油漆修补
按涂装配套逐道修补。在涂装或复涂之前,去除所有表面污染物,如盐分、油脂和灰尘等,钢材表面含盐量不大于 80 mg / m 2(ISO 8502 — 9) ,灰尘为 2 级 (ISO 8502 — 3) 。在整个清洁、油漆、处理和干燥过程中,要注意除湿、控温和涂装安全。
2 . 7 海水浸泡试验
漆膜完全干燥后,压载舱需进行海水浸泡试 验,如使用淡水,应保证 48 h 后开舱检查,如发现缺陷,需进行修补。
3 讨论
关于 LNG 船压载舱涂装工艺方案值得进行一下探讨。
由于不同 LNG 船液货舱绝缘层采用的基座形式不一样 ( 有采用 Mark 3 式的,也有采用 No96 式 或其它形式的 ) ,而它们各自的焊接工艺也不一样, 这样它们焊接时产生的温度对压载舱涂层的影响就不同,所以压载舱涂装就需要采取相应的工艺进行,总的来说, LNG 船压载舱涂装工艺方案通常有 3 种,如表 1 所示。
在日本和韩国的许多船厂,液货舱绝缘层基座 的形式采用的是 Mark3 式的,由于这种形式的基座焊接时间短,产生的热量少,不会对压载舱的涂层产生影响,所以压载舱的涂装工艺大多采用方案 1 ;也有船厂液货舱绝缘层基座的形式采用 No96 式,这种形式的基座焊接时间长,焊接电流大,产生的热量多,高温可能会对压载舱的涂层产生影响,但由于他们大部分基座焊接可在分段阶段涂装前完成,所以也不会对涂层产生影响,所以压载舱的涂装工艺基本采用方案 1 。
表 1 LNG 船压载舱涂装工艺方案
在法国大西洋船厂,液货舱绝缘层基座的形式采用的是 No96 式,压载舱的涂装工艺采用方案 2 。 沪东中华造船集团建造的 LNG 船液货舱绝缘 层基座的形式采用的也是 No96 式,在实船涂装前, 我们做了一些试验来研究液货舱基座焊接所产生 的温度对压载舱涂层的影响,从而选择合适的压载舱涂装配套和涂装工艺,试验程序如下:
(1) 准备 20 mm × 400 mm × 400 mm 和 16 mm × 400mm × 400mm 试板各 1 块。
(2) 试板两面喷丸到 Sa 2 . 5 级 (ISO8501-1) ,然后涂装油漆:
一面:压载舱环氧漆 2 × 150 μ m ;
另一面:车间底漆 15 μ m 。
(3) 待涂层完全干燥后,测量其膜厚。
(4) 在涂车间底漆的一面焊接 3 只基座,要求 如下:
① 焊接处焊接前打磨去除车间底漆;
② 焊接同时,测量背面温度。
(5) 观察背面涂层状况。
(6) 进行涂层的附着力试验。
试验结果分析:
(1) 对于 16 mm 厚钢板,背面温度达到 203 ℃ ,涂层明显被烧坏。
(2) 对于 20 mm 厚钢板,背面温度在 145 ~ 152 ℃ ,涂层未发现损坏,再进行涂层附着力试验, 涂层结合力符合要求。分析:虽然通过试验未发现 涂层损坏,但考虑到钢板背面温度已经超过了环氧涂料的理论耐温极限 150 ℃ ,所以此试验结果还不能确认涂层未被损坏。
(3) 应当指出的是,钢板背面温度与多种因 素有关,如:焊接时的电流、焊接时间、钢板厚度、 钢板是否涂装油漆、漆膜厚度、环境温度、钢板起 始温度、相邻 2 个基座的距离、相邻 2 个基座焊接 时的时间间隔等等,所以实验测出的钢板背面温度有一定的波动。
基于以上试验结果,我们压载舱的涂装工艺采用方案 3 。实船液货舱绝缘层基座焊接时发现:对 于边压载舱,由于液货舱基座焊接处的钢板厚度较 薄 ( 一般在 16 mm 左右 ) ,压载舱涂层被烧坏现象明显,颜色发黄,易于观察发现;对于双层底压载 舱,由于液货舱基座焊接处的钢板厚度较厚 ( 一般 在 20 mm 以上 ) ,压载舱涂层被烧坏现象不明显,很难被发现,修补时需通过测量确定修补点的位置。
4 结语
LNG 压载舱的涂装与船体、舾装的建造工艺关系密切,应牢牢树立“壳舾涂一体化”的造船理念,通过深化设计,提高分段的预舾装率,降低合拢后 涂层的烧损面积,减少涂装的二次除锈率,不断提 高涂装质量和涂装效率,为成功建造优质 LNG 船打下良好的基础。
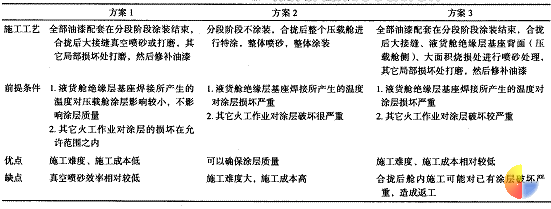
关键词:
压载
相关文章
发布评论