涂料技术
用于水性防锈涂料的交联苯丙乳液的合成及应用
[据涂料涂装资讯网报道]作者:黄兴 , 张宪康 , 郭江 , 张新宇 ( 上海大学材料科学与工程学院高分子材料系 )
摘 要 : 合成了含有缩水甘油基、羧基和氨基的三层核壳结构的交联苯丙乳液 , 研究了中间层厚度、官能团单体用量对乳液性能及其涂膜性能的影响 , 当中间层投料量为核壳层的 50% , 官能团单体甲基丙烯酸缩水甘油酯 (GMA) 、甲基丙烯酸 (MAA) 和甲基丙烯酸二甲氨基乙酯 (DMEMA) 分别为各层投料量的 3% 、 1 .5% 和 3% 时 , 乳液有最佳的综合性能。用该乳液制备的水性防锈涂料与普通苯丙乳液相比具有更好的防锈性能 , 涂膜耐 3% 盐水浸泡时间达 624 h 。
关键词 : 水性防锈涂料 ; 苯丙乳液 ; 交联 ; 甲基丙烯酸缩水甘油酯 ; 甲基丙烯酸二甲氨基乙酯
0 引 言
由于环境保护越来越受到人们的关注 , 对无毒、低毒的水性防锈涂料的研究已成为当前防锈涂料发展的重要方向 [ 1 - 5 ] 。
丙烯酸聚合物保光保色性能及耐老化性能好 , 价格相对较低 , 合成时加入苯乙烯得到的苯丙乳液价格更低 , 常被用作水性防锈涂料成膜体系 [ 6 - 7 ] , 但苯丙乳液涂膜致密性差、对水蒸汽和氧气的屏蔽性不好。乳液合成时采用交联方法可以很好地解决丙烯酸酯涂膜致密性差的问题 , Ivanchev 等利用 GMA 、 MAA 、甲基丙烯酸羟乙酯 (HEMA) 作为交联单体合成了一种高耐水性的两层核壳结构的苯丙乳液 [ 8 ] 。
笔者以 GMA 、 MAA 、 DMAEMA 为交联单体 , 采用在乳液聚合过程中分阶段加入交联单体 , 将交联官能团固定在不同层的方法 , 合成了一种三层核壳结构的交联苯丙乳液 , 研究了中间层厚度、官能团单体比例及用量对乳液聚合稳定性、贮存稳定性、涂膜交联密度和耐水性的影响 , 并用该乳液制备了一种防锈性能优异的水性防锈涂料。
1 实验部分
1. 1 交联乳液的制备
实验原料及配比见表 1 。
采用种子乳液半连续分段滴加不同功能单体预乳液的方法 [9 - 10 ] , 先将部分乳化剂、去离子水和单体分别制成预乳液Ⅰ、Ⅱ和Ⅲ , 其中Ⅰ含单体丙烯酸丁酯 (BA) 、苯乙烯 (St) 和 GMA, Ⅱ含单体 BA 、 St 和 MAA, Ⅲ含单体 BA 、 St 和 DMAEMA 。在装有温度计、冷凝管、滴加装置及搅拌的四口烧瓶中加入一定配比量的乳化剂、去离子水、 pH 调节剂、预乳液Ⅰ以及引发剂 , 升温至 78 ~ 81 ℃ , 保温 0 . 5 ~ 1 h; 然后滴加剩余预乳液Ⅰ和补加引发剂 , 滴完保温反应 0 . 5 h, 升温至 90 ℃ , 再保温反应 0 . 5 h 。同样的步骤先后加入预乳液Ⅱ和Ⅲ , 待保温反应完成 , 降温至低于 50 ℃ , 用氨水调体系 pH 值为 8 ~ 9, 过滤 , 出料待用。
配方 src="/uploadfile/201008/20100827125552488.gif" border=0>
表 1 乳液合成典型配方
1. 2 水性防锈涂料的制备
将分散剂 ( 六偏磷酸钠和 T - 731) 、润湿剂、部分消泡剂、颜填料 ( 复合磷酸锌、二氧化钛、硫酸钡、滑石粉 ) 、去离子水等在高剪切乳化机下混合均匀 , 制得色浆。然后将色浆、聚合物乳液、成膜助剂、剩余消泡剂、 pH 调节剂 ( 氨水或 AMP - 95) 和复合增稠剂在搅拌机中分散均匀 , 经过滤出料。水性防锈涂料配方见表 2 。
配方 src="/uploadfile/201008/20100827125601349.gif" border=0>
表 2 水性防锈涂料典型配方
1. 3 性能测试
1. 3. 1 乳液性能测试
(1) 乳液粒径 : 用 B I - 90 + 型粒径分析仪 ( 美国 BrookhavenItruments Corporation) 测定。
(2) 凝聚率 : 将聚合时产生的凝胶烘干至恒质量 , 凝聚率 = ( m 1 /m 2 ) × 100% , m 1 为凝聚物烘干后质量 , m 2 为单体总质量。用凝聚率来表示乳液的聚合稳定性 , 凝聚率越小 , 聚合稳定性越好。
(3) 涂膜耐水性 : 将制得的乳液加入 5% 的成膜助剂搅拌均匀后 , 涂于聚四氟乙烯板上 , 室温干燥后 , 剥下 , 称取干膜质量 m 1 , 完全浸入去离子水中 , 24 h 后取出 , 用滤纸吸干表面的水 , 称取质量为 m 2 , 则涂膜的吸水率 = ( m 2 - m 1 ) /m 1 × 100% 。用涂膜的吸水率来表征涂膜的耐水性 , 吸水率越高 , 耐水性越差。
(4) 贮存稳定性 : 称取 20 g 乳液置于 100 mL 密闭容器中 , 放入 60 ℃ 烘箱 , 观察结块或絮凝现象出现的时间 , 时间越长 , 贮存稳定性越好。
(5) 交联密度 : 涂膜的交联密度采用溶胀法测试 [ 11 ] 。制膜过程同 (3) , 将涂膜从聚四氟乙烯板上取下 , 剪成适宜用显微镜观察的试样 , 用光学显微镜观察其在用溶剂氯苯溶胀前后尺寸的变化 , 根据以下公式求取涂膜的交联密度
f 为涂膜的溶胀比 , V 2 为平衡溶胀后聚合物在溶胀涂膜中所占的分率 , L 1 为涂膜在溶胀前的某边长度 , L 2 为溶胀后此边的长度。 V 1 为氯苯的摩尔体积 , 取 97 . 1 cm 3 /mol, X 1 为氯苯和涂膜的相互作用参数 , 取 0 . 3, V e 为交联密度。
1. 3. 2 涂膜性能测试
耐盐水性 : 参照 GB /T10834 — 1989, 将制备的涂料涂覆在处理过的马口铁上 , 厚度为 40 ~ 50 μ m, 室温干燥 1 周 , 用蜡封好后放入 3% 的氯化钠溶液中浸泡 , 观察试样起泡、生锈、开裂、剥落等的时间 , 并用 H IROX KH 3000 VD 型三维视频显微镜观察涂膜情况。
2 结果与讨论
2. 1 乳液的结构确定及交联反应原理
基于乳液合成设计思路 , 分别测试乳液 ( 典型配方 ) 合成各阶段的乳胶粒粒径 , 结果如表 3 。
表 3 乳液合成各阶段的平均粒径
由表 3 数据可以看出 , 随着聚合反应的进行 , 乳液各阶段的粒径增加 , 说明加入的新预乳液是在原有乳胶粒上反应 , 形成新的层 , 乳胶粒的理论结构示意图如图 1 。
乳液成膜过程中 , 当水分挥发至乳胶粒相互接触后 , 乳胶粒的结构开始变形 , 并发生塌陷 , 各层聚合物由于扩散和黏性流动而相互混合 , 当聚合物链节所含的官能团相遇时 , 由于氨基可作为环氧基的交联剂 , 也可以作为环氧基和羧基反应的催化剂 , 且都可在室温下进行 , 所以可发生如下交联反应 , 从而使涂膜的强度和性能得以提高。
图 1 乳胶粒结构示意图
2. 2 中间层厚度对乳液性能的影响
由于环氧基和氨基非常容易反应 , 所以用一个中间层来阻隔。当乳胶粒无中间层或中间层较薄时 , 达不到阻隔效果 ; 而当中间层较厚时 , 环氧基和氨基反应十分困难 , 达不到交联提高乳液性能的效果 , 所以中间层的厚度对核壳乳液的制备是至关重要的。 在制备预乳液时先固定各层中官能团单体 ( GMA 、 MAA 、 DMAEMA) 的用量 , 然后改变其他原料的投料量来控制中间层的厚度 , 研究其对乳液聚合稳定性和贮存稳定性以及涂膜交联密度的影响。三层的投料质量比为 : 1 ∶ X ∶ 1, 其中 X 为中间层的投料量相对于核壳层的投料量的百分率 , 实验结果如图 2, 乳液贮存稳定性见表 4 。
图 2 中间层厚度对乳液及涂膜性能的影响
图 3 GMA 用量对乳液及涂膜性能的影响
表 4 X 值对乳液贮存稳定性的影响
由实验结果可知 , 当 X 为 0, 即无中间层时 , 凝胶很多 , 反应失败 , 证明 DMAEMA 单体与环氧基的可反应性 ; 随着 X 值的增加 , 即中间层厚度的增加 , 凝聚率明显下降 , 乳液的稳定性提高 ; 当 X 大于 0.5 后 , 凝聚率下降趋势不明显 , 说明当 X 达到 0 .5 后 , 此时中间层的厚度已经能够较好地阻隔核层和壳层之间官能团的接触。随 X 值的增加 , 涂膜交联密度则是先增加后减少 , 当 X 为 0 .5 时达到最大 , 这是因为当中间层较薄时 , 在聚合过程中官能团频繁接触 , 因反应而消耗掉一部分 , 使得乳液成膜时可发生交联反应的官能团减少 , 交联密度降低 ; 而中间层较厚 , 成膜阶段阻隔官能团间的接触 , 使得交联反应发生困难 , 从而交联密度降低。当中间层预乳液的投料量为核壳层的 50% 时 , 所得到的中间层厚度使乳液的综合性能最好。
2. 3 GMA 单体用量对乳液性能的影响
在确定了中间层厚度后 , 为了提高交联密度 , 进行了官能团单体用量对乳液性能的影响实验。在各层官能团单体比例 (GMA ∶ MAA ∶ DMAEMA = 2 ∶ 1 ∶ 2) 相同的情况下 , 增大各层官能团单体占该层总单体的百分率 ( 以 GMA 为例 ) , 研究其对乳液聚合稳定性、贮存稳定性 , 涂膜的耐水性和交联密度的影响。实验结果如图 3 和表 5 。
由实验结果可见 , 随着官能团单体 ( 表现为 GMA) 用量的增加 , 乳液凝聚率增加 , 贮存稳定时间减小 , 说明聚合稳定性和贮存稳定性均下降。这是因为官能团单体增多 , 聚合过程、贮存过程中易发生反应的官能团之间接触的机会就增大 , 交联凝聚倾向增大。成膜时也是如此 , 官能团越多 , 交联密度就越大 , 机械性能提高 , 耐水性也提高。当 GMA 用量占预乳液投料量的 3% 时 , 乳液有较好的综合性能。
表 5 GMA 用量对乳液贮存稳定性的影响
图 4 DMAEMA 用量对乳液及涂膜性能的影响
2. 4 DMAEMA 单体用量对乳液性能的影响
在确定了核层和中间层官能团单体 (GMA 占核层单体总量的 3% 和 MAA 占中间层单体总量的 1 . 5% ) 用量的情况下 , 为了进一步确定乳液的最佳配方 , 对 DMAEMA 单体的用量对乳液聚合稳定性、贮存稳定性 , 乳胶膜的耐水性和交联密度影响进行了研究。图 4 和表 6 分别显示了 DMAEMA 的用量对乳液的聚合稳定性、贮存稳定性 , 涂膜交联密度和耐水性的影响。
表 6 DMAEMA 用量对乳液贮存稳定性的影响
壳层单体 DMAEMA 作为环氧基团的交联剂 , 其用量增加 , 必然促使交联反应几率的增大 , 如上所示 , 随着 DMAEMA 用量的增加 , 乳液聚合稳定性和贮存稳定性下降 , 涂膜的交联密度提高。由图 4 还可以看出 , 随着 DMAEMA 用量的增加 , 涂膜吸水率增加 , 即耐水性降低 , 这是由于 DMAEMA 含有氨基 , 是亲水性单体。当 DMAEMA 用量占投料量的 3% 时 , 乳液的综合性能较好。
综上所述 , 三种官能团单体的用量分别为占各层单体总量的 : 3% 、 1 . 5% 、 3% 。
2. 5 防锈涂膜耐盐水性
防锈涂膜耐盐水浸泡实验结果如图 5, 其中样品 1 采用商品苯丙乳液 ; 样品 2 为自制交联苯丙乳液。
图 5 盐水浸泡不同时间后涂膜的表面形貌
由图 5 可以看出 , 采用自制的交联苯丙乳液制备的水性防锈涂料与采用商品苯丙乳液制得的涂料相比具有优异的防锈性能 , 浸泡 720 h 后 , 前者只有轻微腐蚀 , 而后者腐蚀十分严重。实际上 , 采用普通苯丙乳液的防锈涂料经盐水浸泡 120 h 起泡 , 168 h ( 实际出锈点时间 ) 出现小锈点 ; 采用交联苯丙乳液 , 624 h ( 实际出锈点时间 ) 才出现了小锈点。说明采用在合成时分阶段加入官能团单体 , 合成的交联苯丙乳液大大提高了涂料的防锈性能 , 主要是因为乳液交联后 , 形成的涂膜致密 , 减少了水分的渗透 , 涂膜的机械性能和耐水性明显增加 , 从而提高涂膜的防锈性。
3 结 语
(1) 采用种子乳液半连续分段滴加不同功能单体预乳液的方法 , 合成了一种交联的苯丙乳液 ; 研究了中间层厚度以及各功能单体的用量对乳液聚合稳定性、贮存稳定性 , 涂膜交联密度和耐水性的影响 , 当中间层单体投量为核壳层的一半 ,GMA 用量占核层单体总量的 3% ,MAA 占中间层单体总量的 1 . 5% ,DMAEMA 占壳层单体总量的 3% 时 , 乳液及涂膜的综合性能最佳。
(2) 解决了普通苯丙乳液涂膜交联不够致密、耐水性差的问题 , 用该苯丙乳液制备的水性防锈漆膜耐 3% 盐水浸泡时间达到 624 h, 说明该乳液是一种适用于水性防锈涂料的乳液。
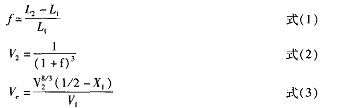
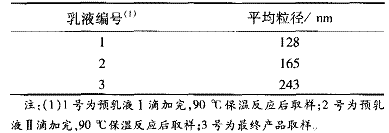
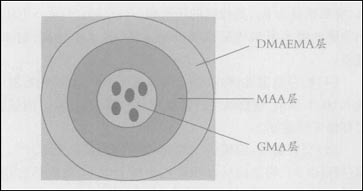
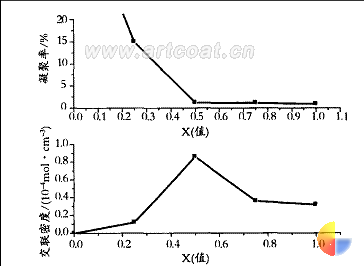
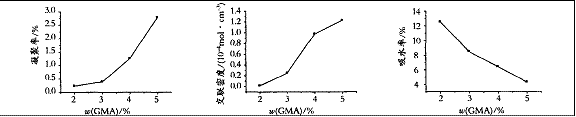
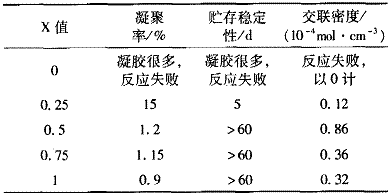
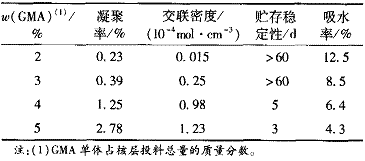
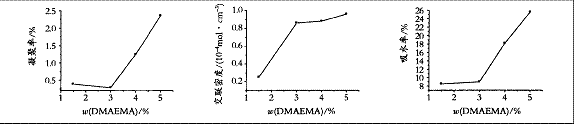
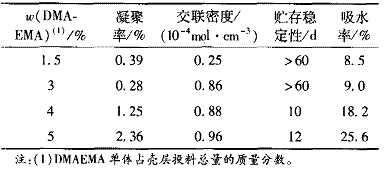
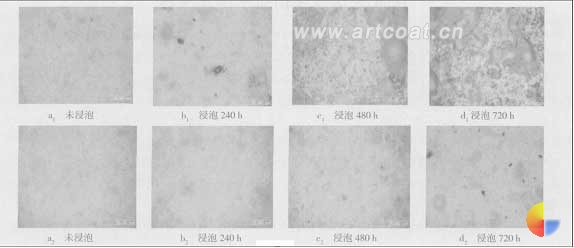
相关文章
发布评论