地坪涂料
厚膜型无溶剂环氧重防腐涂料的研究
蒋健明,陈正涛 (海洋化工研究院,山东青岛266071) 摘要:比较了不同环氧树脂、环氧固化剂、颜填料、助剂等的特性,制备了厚膜型无溶剂环氧涂料,并进行了各项性能的检测,结果表明,该涂料具有极低的VOC含量,符合环保要求,适用于要求长效防腐的钢构件。 关键词:无溶剂涂料;环氧涂料;重防腐涂料;厚膜型涂料 1引言 21世纪是海洋的世纪,国家对海洋的开发力度在逐步加大,以港口经济、海洋经济作为支柱经济。随着各种开发海洋的作业平台如港口、浮船、船舶、海上石油钻采平台、海洋勘探设备的建设,因其中大部分采用钢结构设施,且许多部位要求防腐期效与设备的使用期效相当,这些设施在使用过程中经常受到海洋盐雾、海水的侵蚀,阳光直射使表面温度高达6O℃。强烈紫外线的照射、一些机械的碰撞,致使材料被腐蚀破坏,影响设施的正常使用,甚至造成事故。采用溶剂型防腐涂料进行保护,要满足长期防腐的要求,往往需要涂装多次,每道施工间隔长,不但增加了施工成本和延长了工期,而且易造成涂装缺陷,使涂层防腐期效不理想,需定期进行重涂维修,尤其对于港口的钢管桩、海上石油钻采平台水下部位的维修需要潜水员进行水下作业,耗费巨大。在船舶、勘探设备的压载水舱等密闭狭小的部位进行涂装时,采用溶剂型涂料,往往因通风不良,易燃易爆的有机溶剂挥发,造成挥发性气体积聚形成火灾隐患,且有机溶剂对施工人员、船员的身体也造成不可弥补的损害。 用无溶剂涂料取代溶剂型涂料是防腐涂料的发展趋势。无溶剂涂料符合环保法规的要求,单道施工就能得到厚涂层,提高防腐效果,降低火灾隐患,缩短工期,提高设备的利用率。 涂料防腐期效与涂层特性的数学公式如下:
式中:L——涂层的防腐寿命; h——涂层厚度; D——水和氧气在涂层内的扩散系数; τ——水分透过后的涂层的寿命,是膨胀内部压力()和涂膜剥离层应力(σn)的函数。 从上式可以看出,涂层厚度、涂料密闭性对涂料的防腐寿命起着十分重要的作用。厚膜型无溶剂环氧涂料施工时基本无溶剂挥发,并可以减少涂层中的挥发性气孔,提高涂层密闭性,单道涂膜能达到400μm,具有长效防腐性。 2试验部分 2.1原料和试验仪器设备 液态环氧树脂616、618、6101,工业级,无锡树脂厂等;环氧固化剂聚酰胺140、T31等,天津延安化工厂;活性稀释剂5748、660、600、6360,上海树脂厂等;磷酸锌等防锈颜料;云母氧化铁、硫酸钡等填料;助剂。试验仪器设备:S-65三辊机、SFJ-400砂磨分散多用机、QCJ型漆膜冲击器、Q—FOG盐雾试验箱。 2.2配方设计 比较不同类型的环氧树脂、环氧固化剂,确定涂料树脂体系。添加不同的颜料和涂料助剂,按不同配比研磨制漆,进行性能评价。 2.3性能测试 性能测试结果见表1。
表 1 检测项目及指标 3结果与讨论。 3.1树脂基料对涂料性能的影响 3.1.1环氧树脂对涂料性能的影响 无溶剂环氧涂料重点需要解决涂料的常温施工性能与涂料韧性、防腐性能之间的综合平衡。环氧树脂随着其相对分子质量的变化和树脂类型不同,其特性也有较大的区别。对双酚A型616、6101、618的黏度、低温结晶性能、反应活性、防腐性能、机械性能进行了比较。双酚A型618等液态环氧树脂常温黏度大于12Pa-s,尤其在低温时618、616、6101等环氧树脂黏度增加较大,加工变得十分困难;双酚A型环氧树脂随其相对分子质量的降低,分子中的羟基含量降低,缺少羟基的催化作用,树脂的反应活性降低,与固化剂的胶化时间延长,更利于施工;双酚A型环氧树脂随其相对分子质量的降低,对应的防腐性能略有下降,但仍能满足目标的防腐要求;由于分子链的变短,涂层的柔韧性降低,脆性增大。双酚F型较双酚A型有更好的防腐效果,但它所得涂层的机械性能略差,尤其脆性较大。综合以上环氧树脂的特点,为得到具有良好的加工性能,较长的施工期效、防腐性能和低温可操作性,以618环氧树脂作为环氧涂料的主要基料。 3.1.2活性稀释剂对涂料性能的影响 为进一步降低树脂黏度,采用活性稀释剂来稀释环氧树脂。通过对单、双、三官能度的多种活性稀释剂进行比较,660、600类活性稀释剂气味较大,稀释效率高,但对涂料的增韧改性效果不明显,对胶化时间无明显影响。5748毒性小,稀释效率高,但与胺类固化剂的混容性差。最终采用聚醚型环氧树脂6360作为环氧树脂的稀释和增韧剂,延长体系的胶化时问。 将此活性稀释剂添加到树脂体系中,大大降低了涂料的体系黏度,同时提高了体系的柔韧性和抗冲击性能。添加5%聚醚型环氧树脂6360,清漆漆膜经50cm冲击,未见开裂脱落现象。随着颜料量的增加,色漆的抗冲击性能降低,相应的增韧剂的用量需要提高,当聚醚型环氧树脂6360占树脂总量的25%时,颜料体积浓度为20%的涂料漆膜仍有良好的柔韧性和抗冲击性(见图1,图2)。
图 1 活性稀释剂用量对清漆漆膜抗冲击性能的影响
图 2 活性稀释剂用量对色漆漆膜抗冲击性能的影响 3.1.3固化剂对涂料性能的影响 单纯依靠环氧树脂并不能使涂料的黏度降低到可进行刷涂或高压无气喷涂的要求,以618/6360环氧树脂为基料,筛选与其配套良好的固化剂。通过与多种固化剂进行配套试验,结果见表2。
表2 环氧树脂与不同固化剂的配套试验 从表2可以看出,前几种固化剂与液态环氧树脂固化所得涂膜的混容性差或胶化时间短,改性芳香胺因其本身具有致癌的嫌疑,不能使用。醚胺因其低温固化性差,涂层亲水性强,防腐效果差,不能选择。而脂肪胺加成物与选用的环氧树脂混合,黏度较小,无残留挥发气味,能低温固化。最终确定以脂肪胺加成物作为无溶剂涂料基料的固化剂组分。 3.2防锈颜料对涂料性能的影响 在确定基础组分前,先对添加磷酸锌防锈颜料的不同颜料体积浓度对涂料的综合性能的影响进行分析,结果见表3。
表 3 不同颜料体积浓度对涂料性能的影响 随着颜料体积浓度的增大,涂料的黏度增大,这将大大影响涂料的施工性能。涂料中的防锈颜料必须达到一定的用量,才能比较有效地发挥其防腐作用。在综合各项性能后,最终确定防锈底漆的颜料体积浓度为20%。对于高黏度涂料,为提高双组分的混合效率,涂料各组分之间黏度接近,混合效率最高,并分别进行着色处理,来显示涂料的混合均匀程度。 通过试验发现,用确定的基料树脂添加颜填料制成涂料,所得涂膜进行盐雾试验,由于此环氧防腐涂料的高封闭性,涂层未破坏前,无论采用何种颜料(如氧化铁红、云母氧化铁、磷酸锌、三聚磷酸铝等),其耐盐雾、耐盐水等性能差别不大。不同颜料对涂料的防腐性能几乎无影响,亦证明所选择的基料树脂有高的防腐性能。但划痕破坏以后,防锈颜料与其他颜料的区别就显现出来。防锈颜料涂层盐雾试验1000h后无鼓泡,仅在划痕处锈蚀,而采用其他颜料的涂层,200h就开始鼓泡。 对不同的防锈颜料,以不同的用量和比例复配成防锈颜料体系。采用复合防锈颜料体系,能综合不同颜料的防锈特点。试验中发现,单纯采用一种防锈颜料,磷酸锌对防止锈蚀扩散效果最好,涂层附着力最强,但早期防锈效果不佳,易形成点蚀;三聚磷酸铝和改性钛白粉能形成均匀腐蚀,改性钛白粉能增强漆膜的韧性,提高漆膜在湿态下的抗剥离性能,但成本较高。采用磷酸锌和三聚磷酸铝复合防锈颜料,涂料对基材有良好的附着强度,高的耐盐雾、耐海水性能。3.3涂料助剂对涂料性能的影响 高黏度厚膜型环氧防腐涂料的消泡问题、抗流挂性问题解决起来很困难。为了得到厚膜涂层,在涂料中添加高触变性的流变剂,增大涂料的黏度,但对涂料混合过程中搅入的气泡的逸出和破灭不利,需要在两者之间进行综合平衡。对国内外的近10种消泡剂、流变助剂进行了比较选择:BYK-085、066、065,德谦公司的6800、3200、2700、togo-900、NX,wacker-700、130莱阳的二甲基硅油等消泡剂,气相二氧化硅(R972、A200),氢化蓖麻油、聚酰胺蜡等流变助剂。按照每种消泡剂、流变剂的理论用量,进行了正交复配试验,发现无溶剂的togo-900具有高脱泡性能,且易于分散,适量用时表面不出油,不影响层间附着力,无论喷涂或刷涂,表面能观察到明显的脱泡和破泡现象。采用气相二氧化硅对提高厚膜涂料的抗流挂性较氢化蓖麻油好,但涂料的流动性差,消泡剂用量增多。添加总量的0.5%的消泡剂和2%的气相二氧化硅,能得到较好的漆膜外观。单道涂膜400μm,无流挂,无泡孔。 4结论 (1)厚膜型无溶剂环氧涂料,其涂料施工性能和机械性能主要决定于环氧树脂、环氧固化剂、颜料和助剂的类型。 (2)厚膜型无溶剂环氧涂料一次施工可得厚膜。减少施工道数,提高工作效率;涂料的密闭性高,大大提高了涂料的防腐寿命;由于极低的VOC,减少环境污染,尤其适用于一些密闭狭小、不易日常维护且需要长效防腐的钢构件。(来源:慧聪网)

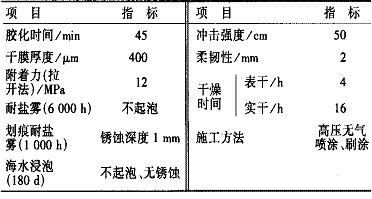
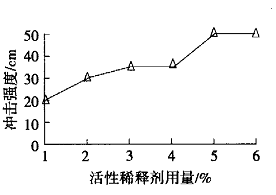
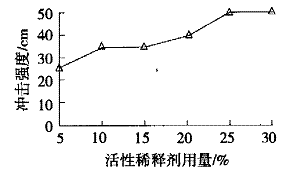
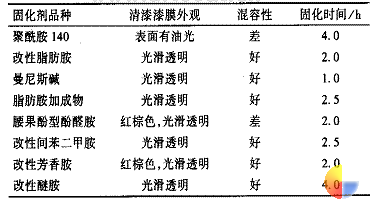
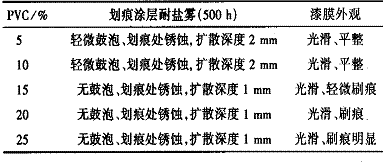
上一篇:介绍无溶剂防静电自流平地坪优点
下一篇:离子法双酚A工艺优化探讨
相关文章
发布评论