涂料技术
水性聚苯胺微乳液及其防腐涂料研究
水性聚苯胺微乳液及其防腐涂料研究
水性涂料具有无色、无味、无毒、低粘度、快干、
透明感强、高固含量、无有机挥发物、成本低、来源广
、可用水稀释和清洗、对操作要求相对较宽等特点,这
是其它溶剂型涂料所不具备的。近年来,由于人们对环
境保护的日益关注,许多国家相继颁发了有关控制挥发
性有机化合物(VOC)的法令,环保法规不断强化,促使
涂料工业加速向4个方向发展,即水性涂料、粉末涂料、
高固体分涂料和辐射固化涂料,其中由于溶剂价格的上
涨以及环境保护法规的限制使得以水作溶剂的水性涂料
成为涂料发展的一个热点。
聚苯胺作为一种导电高分子材料,由于原料便宜、合
成简便及抗氧化性能、防腐性能优良等特点,在许多方
面有着广泛的应用前景。目前国外已经研究并开发出多
种聚苯胺防腐涂料,并己商业化,如CORRPASSI
V、ORMECON、Versicon和Corep
air等。但是这些产品都是溶剂型涂料,在使用时由
于溶剂的挥发会污染环境。本文将自行合成的聚苯胺水
性微乳液直接与环氧树脂共混复合,试图在不使用任何
有机溶剂的前提下配制出水性防腐涂料,并从两个途径
考察了对金属的防腐能力。
1 试验部分
1.1 试验原料苯胺:
分析纯;十二烷基硫酸钠(SDS):化学纯;过硫酸铵(A
PS):分析纯;十二烷基苯磺酸(DBSA):化学纯;618
环氧树脂(EP);固化剂:C-2环氧树脂固化剂。其它试
剂均为市售产品,使用前未经任何处理。
1.2 聚苯胺水性微乳液的制备方法将一定量的乳化剂
SDS和氧化剂APS加入到一定量的酸性水溶液反应
介质中,搅拌1h左右,配制成乳化剂与氧化剂的混合溶
液。取一定量的苯胺单体配成相应的酸性水溶液,将其
按照不同的比例分两批滴加到上述混合溶液中,两批之
间的间隔时间约为1h,滴速保持在1滴/min。滴毕,
在20℃搅拌反应24h,即得聚苯胺水性微乳液。将该乳
液用丙酮破乳、洗涤数遍后再用去离子水清洗,即得聚
苯胺颗粒粉末。
1.3 聚苯胺微乳液及颗粒粉末的表征将一定量的聚苯
胺微乳液按1:10用去离子水稀释后,在25℃用乌氏粘度
计(0.6~0.7mm)测量其流出时间,以表征微乳液的相
对粘度。将一定量的聚苯胺颗粒粉末溶解在浓硫酸中,
利用0.6~0 7mm的乌氏粘度计在25℃下测量其特征粘
数。将一定量的聚苯胺颗粒粉压制成一定厚度的圆片,
利用UT70A型数字万用表测量其电导率。将一定量的
聚苯胺颗粒粉末置于试样架上,利用D/max2550型X射
线衍射仪测试其结晶性能。
1.4 聚苯胺水性微乳液防腐性能测试
首先将钢板用锉刀进行机械法除锈,再用0号砂纸打磨至
表面平整,达到St2级。然后用丙酮对钢板进行除油处
理,以提高涂料的附着力。分别用聚苯胺水性微乳液、
聚苯胺水性微乳液/EP混合乳液和环氧树脂乳液为涂
料,以不同的复合方式涂刷在钢板上,100℃下烘烤7天,
待干燥后将钢板浸入自来水中,以铂电极作为参考电极,
用PHS 2C型数显酸度计测试钢板的开路电位随时间
的变化,从而评价其防腐性能。
2 结果与讨论
2.1 基料选择
基料是涂料的主要组成部分,是获得良好力学性能的关
键,同时,基料的选择也影响到涂料的物理屏蔽性能从而
间接影响涂料的防腐性能。因此,选择合适的基料是制
备良好性能涂料的关键所在。在三大通用型热固性树脂
(环氧树脂、酚醛树脂和不饱和聚酯树脂)中,环氧树脂
以其独特的分子结构(含有环氧基,以及羟基、醚键等活
性基团和极性基团)而具有许多优异的性能。同时,它还
能被许多的固化剂进行固化,从而可得到各种不同性能
的涂料,配方设计非常灵活。在水性涂料中,环氧树脂系
涂料具有很高的附着力和耐腐蚀性能,且聚结剂、辅料
用量较少,相对安全性较好,它同时兼有溶剂型环氧涂料
诸多的优点。水性环氧涂料在20℃,5%相对湿度下,一般
2h就可达到表面指触干;最低固化温度为0℃;可与水性
丙烯酸涂料或溶剂型涂料配套使用;溶剂挥发少,属环境
友好型材料。故选用环氧树脂作为涂料的基料,选用能
溶于水的固化剂(多胺类)来固化环氧树脂,达到减少使
用乳化剂的目的。
而利用环氧树脂制备水性涂料通常有两种方式:(1)对环
氧树脂改性,在分子链上接亲水性的基团,制备自乳化环
氧树脂。这种方法所制备的乳液非常稳定,但是,由于要
对环氧树脂进行改性,因此制备过程复杂,不利于降低成
本。(2)利用乳化剂进行乳化制备环氧树脂乳液。这种
方法在一定的条件下也能制备稳定的环氧树脂乳液,而
且由于采用乳化剂进行乳化,在很多情况下都能实现,便
于推广使用。因此,本研究采用水乳化环氧树脂体系。
2.2 聚苯胺水性微乳液选择
将单体分批滴加到氧化剂和乳化剂SDS形成的水性微
乳液体系中,在不同的酸介质体系中合成出纳米聚苯胺
微乳液。微乳液性能及由其破乳后所获得的纳米粒子性
能见表1。可见除了在乙酸溶液中外,在盐酸、磷酸、硫
酸和DBSA稀水溶液中均可合成出性能稳定的微乳液
,放置至少半年不分层,且乳液粘度较低,流动性较好。
尤其在盐酸、磷酸情况下,不仅可以制得墨绿色的稳定
的聚苯胺微乳液,而且乳液体系相对粘度较低,易于后续
的涂料混合加工。相应地,其破乳后获得的纳米聚苯胺
的产率、分子量和导电性都较高。因此,由该法合成的
纳米聚苯胺有望用于高性能防腐涂料。
表1 不同的酸介质体系中合成的聚苯胺纳米微乳液
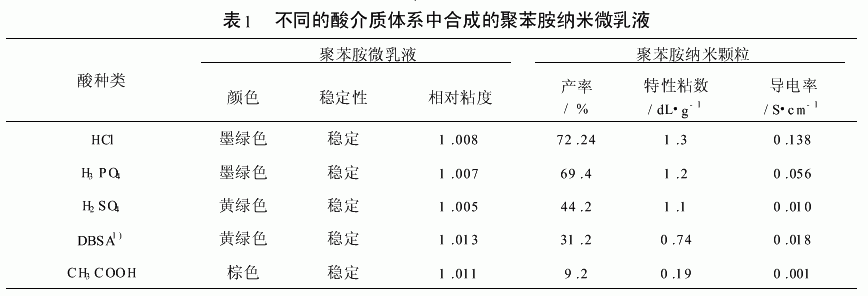
微乳液聚合中,水溶液中的酸作为聚苯胺的掺杂物质,
其离解能力将直接影响到聚苯胺分子链的排列。这样除
了对电导率产生影响外,掺杂剂还可能在分子链间起到
小分子的增塑作用[10],进而影响到聚苯胺的结晶性。
各种不同酸的微乳液中合成的聚苯胺颗粒WAXD图谱
见图1。从图1可以看出,这几种酸掺杂所得的聚苯胺的
结晶性从大到小依次为:DBSA>H2SO4>H3PO4>
HCl。
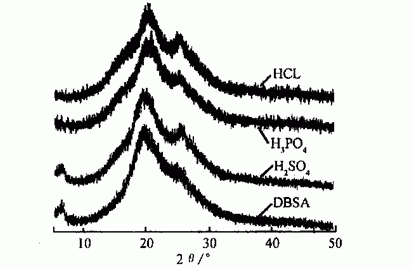
图1 各种不同酸的微乳液中合成的聚苯胺颗粒WAXD图谱
可见,DBSA掺杂所得的聚苯胺的结晶性最好,这主要是由于DBSA的增塑作用引起的。众所周知,DBSA作为一种有机酸,既可以作为掺杂剂,也可以作为乳化剂,虽然其酸性较弱,但是由于其独特的结构,可以参与
胶束的形成,与聚苯胺分子链的接触机会较多,非常容易掺杂到分子链中,然后,由于其乳化作用,可以使聚苯胺分子链产生一定程度的规整排列,因此可以提高聚苯胺的结晶性。H2SO4和H3PO4由于其酸根阴离子的空间位阻作用影响了聚苯胺分子链的整齐排列,因此其结晶性不如DBSA掺杂的。稀HCl与稀H2SO4相比由于酸浓度不够,生成的产物不能进行足够的掺杂,因此其结晶性不高。
DBSA分子量较大,而且较稳定,因此由它所掺杂的聚苯胺也较稳定,不易因为温度变化等不利因素而变化,由其制备的涂料的使用寿命较长,故本文以在DBSA水溶液中合成的纳米聚苯胺微乳液为例研究其防腐性能。
2.3 聚苯胺水性涂料的防腐性能
采用开路电位法来衡量涂料的防腐性能。利用达到平衡后的开路电位大小来估计涂料防腐性能的优劣,开路电位高,则防腐性能好。将合成的聚苯胺水性微乳液直接与环氧树脂乳液共混均匀,用以下几种不同的方式涂刷在钢板上,记录的开路电位随时间的变化见图2。
方式1:空白试样,不进行任何涂刷;
方式2:将聚苯胺水性微乳液直接与环氧树脂乳液共混后
涂刷;
方式3:仅涂刷一层聚苯胺水性微乳液;
方式4:仅涂刷一层聚环氧树脂乳液;
方式5:先将聚苯胺水性微乳液直接涂刷,再在其上涂刷
一层环氧树脂乳液;
方式6:在方式2的基础上再涂刷一层环氧树脂乳液。
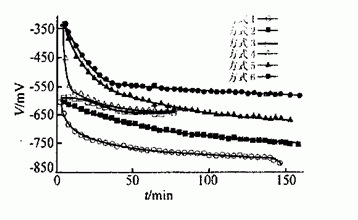
图2 各种涂装方式下的聚苯胺水性涂料在自来水中的
开路电位随浸泡时间的变化
从图2可看出,无论以何种方式涂装的钢板,其开路电位
均比无涂装的裸露钢板高,表明这些涂料对钢板均具有
一定的防腐功效。若从起始电位考虑,图2中的6条开路
电位曲线明显可分为两组:无环氧树脂面漆组(即方式1
、2、3)和有环氧树脂面漆组(即方式4、5、6),且后者
的起始开路电位明显高于前者,显示出了环氧树脂原有
的防腐能力,它能在最初阶段有效地阻碍腐蚀介质以及
腐蚀产物的扩散。然而,随着浸泡时间的延长,腐蚀介质
逐渐扩散进入涂层并与钢板接触腐蚀,使得这两组曲线
开路电位均逐渐下降并达到某一平衡值,而且起始开路
电位高的下降幅度也大。显然,最终的防腐性能应该由
平衡开路电位值决定。仅涂刷一层聚苯胺水性微乳液与
仅涂刷一层聚环氧树脂乳液具有同样的平衡开路电位值
(图2,方式3和4),说明了两者具有相似的金属防腐能力
。而方式5的平衡开路电位略低于它们,这主要是由于方
式5中PAN微乳液作底漆时与钢板的附着力差,在腐蚀
介质的作用下很容易脱落失效。方式6的平衡开路电位
最高,可达-550mV(vs.Pt),与裸露钢板的平衡开
路电位-817mV相比提高了235mV,显示出了最好的防
腐性能。这主要有两方面的原因,一方面,在由聚苯胺微
乳液和环氧树脂乳液混合而成的底漆中,其中的环氧树
脂能有效地提高底漆与钢板的附着力,减少腐蚀介质对
钢板的腐蚀作用;而其中的聚苯胺能有效地提供防腐作
用。另一方面,覆盖在底漆上的面漆具有一定的屏蔽作
用,可阻碍腐蚀介质和腐蚀产物在涂层中扩散,使防腐性
能进一步提高。因此,首先用聚苯胺微乳液和环氧树脂
乳液的共混乳液刷涂成底漆,然后在其上面覆盖一层环
氧树脂面漆,这种涂装方式具有最佳的防腐性能。水中
的浸泡情况。可以看出,纯聚苯胺微乳液可以将钢板的
生锈时间从60min提高到120min,增加了2倍,但是
由于PAN的附着力差,而且其中的乳化剂易于在水中
溶解,致使其在浸泡6min后涂层就出现了部分溶解脱
落现象。为了提高PAN微乳液底漆的附着力,我们将
PAN微乳液与环氧树脂进行共混复合,成功地将生锈
时间提高到31天,优于纯环氧树脂涂层的性能。再在其
上施加一层环氧树脂面漆,防腐性能进一步提高,在自来
水中至少浸泡90天,既不起泡,也不生锈。因此,所合成
的聚苯胺微乳液在水性金属防腐领域具有较大的应用潜
力。
3 结论
(1)以DBSA为酸性介质通过改进的微乳液聚合法合
成的纳米聚苯胺水性微乳液可以直接用作金属防腐涂料
。
(2)以聚苯胺水性微乳液与环氧树脂共混形成的乳液作
为底漆、以环氧树脂乳液作为面漆的涂装方式,可以获
得最佳的防腐性能,其防腐性能明显优于纯环氧树脂或
纯聚苯胺涂层的。

水性涂料具有无色、无味、无毒、低粘度、快干、
透明感强、高固含量、无有机挥发物、成本低、来源广
、可用水稀释和清洗、对操作要求相对较宽等特点,这
是其它溶剂型涂料所不具备的。近年来,由于人们对环
境保护的日益关注,许多国家相继颁发了有关控制挥发
性有机化合物(VOC)的法令,环保法规不断强化,促使
涂料工业加速向4个方向发展,即水性涂料、粉末涂料、
高固体分涂料和辐射固化涂料,其中由于溶剂价格的上
涨以及环境保护法规的限制使得以水作溶剂的水性涂料
成为涂料发展的一个热点。
聚苯胺作为一种导电高分子材料,由于原料便宜、合
成简便及抗氧化性能、防腐性能优良等特点,在许多方
面有着广泛的应用前景。目前国外已经研究并开发出多
种聚苯胺防腐涂料,并己商业化,如CORRPASSI
V、ORMECON、Versicon和Corep
air等。但是这些产品都是溶剂型涂料,在使用时由
于溶剂的挥发会污染环境。本文将自行合成的聚苯胺水
性微乳液直接与环氧树脂共混复合,试图在不使用任何
有机溶剂的前提下配制出水性防腐涂料,并从两个途径
考察了对金属的防腐能力。
1 试验部分
1.1 试验原料苯胺:
分析纯;十二烷基硫酸钠(SDS):化学纯;过硫酸铵(A
PS):分析纯;十二烷基苯磺酸(DBSA):化学纯;618
环氧树脂(EP);固化剂:C-2环氧树脂固化剂。其它试
剂均为市售产品,使用前未经任何处理。
1.2 聚苯胺水性微乳液的制备方法将一定量的乳化剂
SDS和氧化剂APS加入到一定量的酸性水溶液反应
介质中,搅拌1h左右,配制成乳化剂与氧化剂的混合溶
液。取一定量的苯胺单体配成相应的酸性水溶液,将其
按照不同的比例分两批滴加到上述混合溶液中,两批之
间的间隔时间约为1h,滴速保持在1滴/min。滴毕,
在20℃搅拌反应24h,即得聚苯胺水性微乳液。将该乳
液用丙酮破乳、洗涤数遍后再用去离子水清洗,即得聚
苯胺颗粒粉末。
1.3 聚苯胺微乳液及颗粒粉末的表征将一定量的聚苯
胺微乳液按1:10用去离子水稀释后,在25℃用乌氏粘度
计(0.6~0.7mm)测量其流出时间,以表征微乳液的相
对粘度。将一定量的聚苯胺颗粒粉末溶解在浓硫酸中,
利用0.6~0 7mm的乌氏粘度计在25℃下测量其特征粘
数。将一定量的聚苯胺颗粒粉压制成一定厚度的圆片,
利用UT70A型数字万用表测量其电导率。将一定量的
聚苯胺颗粒粉末置于试样架上,利用D/max2550型X射
线衍射仪测试其结晶性能。
1.4 聚苯胺水性微乳液防腐性能测试
首先将钢板用锉刀进行机械法除锈,再用0号砂纸打磨至
表面平整,达到St2级。然后用丙酮对钢板进行除油处
理,以提高涂料的附着力。分别用聚苯胺水性微乳液、
聚苯胺水性微乳液/EP混合乳液和环氧树脂乳液为涂
料,以不同的复合方式涂刷在钢板上,100℃下烘烤7天,
待干燥后将钢板浸入自来水中,以铂电极作为参考电极,
用PHS 2C型数显酸度计测试钢板的开路电位随时间
的变化,从而评价其防腐性能。
2 结果与讨论
2.1 基料选择
基料是涂料的主要组成部分,是获得良好力学性能的关
键,同时,基料的选择也影响到涂料的物理屏蔽性能从而
间接影响涂料的防腐性能。因此,选择合适的基料是制
备良好性能涂料的关键所在。在三大通用型热固性树脂
(环氧树脂、酚醛树脂和不饱和聚酯树脂)中,环氧树脂
以其独特的分子结构(含有环氧基,以及羟基、醚键等活
性基团和极性基团)而具有许多优异的性能。同时,它还
能被许多的固化剂进行固化,从而可得到各种不同性能
的涂料,配方设计非常灵活。在水性涂料中,环氧树脂系
涂料具有很高的附着力和耐腐蚀性能,且聚结剂、辅料
用量较少,相对安全性较好,它同时兼有溶剂型环氧涂料
诸多的优点。水性环氧涂料在20℃,5%相对湿度下,一般
2h就可达到表面指触干;最低固化温度为0℃;可与水性
丙烯酸涂料或溶剂型涂料配套使用;溶剂挥发少,属环境
友好型材料。故选用环氧树脂作为涂料的基料,选用能
溶于水的固化剂(多胺类)来固化环氧树脂,达到减少使
用乳化剂的目的。
而利用环氧树脂制备水性涂料通常有两种方式:(1)对环
氧树脂改性,在分子链上接亲水性的基团,制备自乳化环
氧树脂。这种方法所制备的乳液非常稳定,但是,由于要
对环氧树脂进行改性,因此制备过程复杂,不利于降低成
本。(2)利用乳化剂进行乳化制备环氧树脂乳液。这种
方法在一定的条件下也能制备稳定的环氧树脂乳液,而
且由于采用乳化剂进行乳化,在很多情况下都能实现,便
于推广使用。因此,本研究采用水乳化环氧树脂体系。
2.2 聚苯胺水性微乳液选择
将单体分批滴加到氧化剂和乳化剂SDS形成的水性微
乳液体系中,在不同的酸介质体系中合成出纳米聚苯胺
微乳液。微乳液性能及由其破乳后所获得的纳米粒子性
能见表1。可见除了在乙酸溶液中外,在盐酸、磷酸、硫
酸和DBSA稀水溶液中均可合成出性能稳定的微乳液
,放置至少半年不分层,且乳液粘度较低,流动性较好。
尤其在盐酸、磷酸情况下,不仅可以制得墨绿色的稳定
的聚苯胺微乳液,而且乳液体系相对粘度较低,易于后续
的涂料混合加工。相应地,其破乳后获得的纳米聚苯胺
的产率、分子量和导电性都较高。因此,由该法合成的
纳米聚苯胺有望用于高性能防腐涂料。
表1 不同的酸介质体系中合成的聚苯胺纳米微乳液
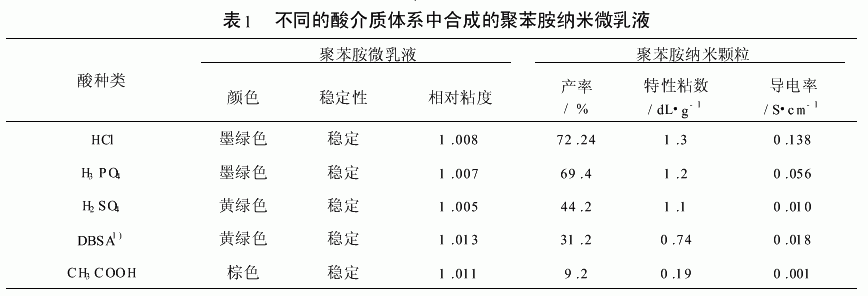
微乳液聚合中,水溶液中的酸作为聚苯胺的掺杂物质,
其离解能力将直接影响到聚苯胺分子链的排列。这样除
了对电导率产生影响外,掺杂剂还可能在分子链间起到
小分子的增塑作用[10],进而影响到聚苯胺的结晶性。
各种不同酸的微乳液中合成的聚苯胺颗粒WAXD图谱
见图1。从图1可以看出,这几种酸掺杂所得的聚苯胺的
结晶性从大到小依次为:DBSA>H2SO4>H3PO4>
HCl。
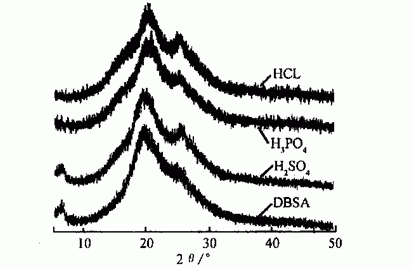
图1 各种不同酸的微乳液中合成的聚苯胺颗粒WAXD图谱
可见,DBSA掺杂所得的聚苯胺的结晶性最好,这主要是由于DBSA的增塑作用引起的。众所周知,DBSA作为一种有机酸,既可以作为掺杂剂,也可以作为乳化剂,虽然其酸性较弱,但是由于其独特的结构,可以参与
胶束的形成,与聚苯胺分子链的接触机会较多,非常容易掺杂到分子链中,然后,由于其乳化作用,可以使聚苯胺分子链产生一定程度的规整排列,因此可以提高聚苯胺的结晶性。H2SO4和H3PO4由于其酸根阴离子的空间位阻作用影响了聚苯胺分子链的整齐排列,因此其结晶性不如DBSA掺杂的。稀HCl与稀H2SO4相比由于酸浓度不够,生成的产物不能进行足够的掺杂,因此其结晶性不高。
DBSA分子量较大,而且较稳定,因此由它所掺杂的聚苯胺也较稳定,不易因为温度变化等不利因素而变化,由其制备的涂料的使用寿命较长,故本文以在DBSA水溶液中合成的纳米聚苯胺微乳液为例研究其防腐性能。
2.3 聚苯胺水性涂料的防腐性能
采用开路电位法来衡量涂料的防腐性能。利用达到平衡后的开路电位大小来估计涂料防腐性能的优劣,开路电位高,则防腐性能好。将合成的聚苯胺水性微乳液直接与环氧树脂乳液共混均匀,用以下几种不同的方式涂刷在钢板上,记录的开路电位随时间的变化见图2。
方式1:空白试样,不进行任何涂刷;
方式2:将聚苯胺水性微乳液直接与环氧树脂乳液共混后
涂刷;
方式3:仅涂刷一层聚苯胺水性微乳液;
方式4:仅涂刷一层聚环氧树脂乳液;
方式5:先将聚苯胺水性微乳液直接涂刷,再在其上涂刷
一层环氧树脂乳液;
方式6:在方式2的基础上再涂刷一层环氧树脂乳液。
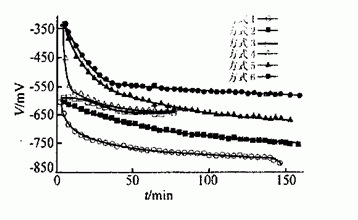
图2 各种涂装方式下的聚苯胺水性涂料在自来水中的
开路电位随浸泡时间的变化
从图2可看出,无论以何种方式涂装的钢板,其开路电位
均比无涂装的裸露钢板高,表明这些涂料对钢板均具有
一定的防腐功效。若从起始电位考虑,图2中的6条开路
电位曲线明显可分为两组:无环氧树脂面漆组(即方式1
、2、3)和有环氧树脂面漆组(即方式4、5、6),且后者
的起始开路电位明显高于前者,显示出了环氧树脂原有
的防腐能力,它能在最初阶段有效地阻碍腐蚀介质以及
腐蚀产物的扩散。然而,随着浸泡时间的延长,腐蚀介质
逐渐扩散进入涂层并与钢板接触腐蚀,使得这两组曲线
开路电位均逐渐下降并达到某一平衡值,而且起始开路
电位高的下降幅度也大。显然,最终的防腐性能应该由
平衡开路电位值决定。仅涂刷一层聚苯胺水性微乳液与
仅涂刷一层聚环氧树脂乳液具有同样的平衡开路电位值
(图2,方式3和4),说明了两者具有相似的金属防腐能力
。而方式5的平衡开路电位略低于它们,这主要是由于方
式5中PAN微乳液作底漆时与钢板的附着力差,在腐蚀
介质的作用下很容易脱落失效。方式6的平衡开路电位
最高,可达-550mV(vs.Pt),与裸露钢板的平衡开
路电位-817mV相比提高了235mV,显示出了最好的防
腐性能。这主要有两方面的原因,一方面,在由聚苯胺微
乳液和环氧树脂乳液混合而成的底漆中,其中的环氧树
脂能有效地提高底漆与钢板的附着力,减少腐蚀介质对
钢板的腐蚀作用;而其中的聚苯胺能有效地提供防腐作
用。另一方面,覆盖在底漆上的面漆具有一定的屏蔽作
用,可阻碍腐蚀介质和腐蚀产物在涂层中扩散,使防腐性
能进一步提高。因此,首先用聚苯胺微乳液和环氧树脂
乳液的共混乳液刷涂成底漆,然后在其上面覆盖一层环
氧树脂面漆,这种涂装方式具有最佳的防腐性能。水中
的浸泡情况。可以看出,纯聚苯胺微乳液可以将钢板的
生锈时间从60min提高到120min,增加了2倍,但是
由于PAN的附着力差,而且其中的乳化剂易于在水中
溶解,致使其在浸泡6min后涂层就出现了部分溶解脱
落现象。为了提高PAN微乳液底漆的附着力,我们将
PAN微乳液与环氧树脂进行共混复合,成功地将生锈
时间提高到31天,优于纯环氧树脂涂层的性能。再在其
上施加一层环氧树脂面漆,防腐性能进一步提高,在自来
水中至少浸泡90天,既不起泡,也不生锈。因此,所合成
的聚苯胺微乳液在水性金属防腐领域具有较大的应用潜
力。
3 结论
(1)以DBSA为酸性介质通过改进的微乳液聚合法合
成的纳米聚苯胺水性微乳液可以直接用作金属防腐涂料
。
(2)以聚苯胺水性微乳液与环氧树脂共混形成的乳液作
为底漆、以环氧树脂乳液作为面漆的涂装方式,可以获
得最佳的防腐性能,其防腐性能明显优于纯环氧树脂或
纯聚苯胺涂层的。

下一篇:纳米材料在汽车涂料中的应用
相关文章
发布评论