涂料技术
聚苯胺涂料的防腐蚀机理及应用前景
作者:王光国(邯郸市峰峰矿务局 河北邯郸 056201)
1 前言
140年前化学家就报导了聚苯胺,但认识到聚苯胺是一种导电高分子材料才只有20多年。聚苯胺在抗静电、电磁屏蔽、有机发光二极管及抗金属腐蚀等方面有诱人的应用前景,因此,是一个热门的研究领域。聚苯胺防腐蚀涉及聚苯胺化学和金属腐蚀科学,现在世界每年发表的有关论文超过一千篇。本文简要介绍聚苯胺涂料防腐蚀机理研究的进展,首先介绍金属防腐蚀的有关知识,然后介绍聚苯胺防腐蚀的氧化膜机理及“双极性涂层”机理,最后讨论聚苯胺涂料的应用前景。
2 有机涂层电阻与其防腐性能的关系
有机涂层的防腐蚀作用曾被认为是将金属表面与环境中的氧气及水隔开。但是半个多世纪以来金属腐蚀研究表明,有机涂层的防腐作用在于阻挡离子的穿透[1,2]。当有机涂层浸在水溶液中时,其电阻越高则离子越难穿透。Baco等人[3]测定了碳钢上300多种有机涂层在海水中的直流电阻R(R=每平方厘米浸没面积的电阻,W)。他们发现,在浸入海水的最初5至10分钟内各种涂层log R约为9。浸泡过程中电阻的变化可分为三类(见图1)。若log R能保持在8以上者,涂层防腐效果良好,若电阻直线迅速下降,则防腐蚀效果差,电阻变化介于上述二者之间的,防腐蚀效果一般。改变成膜物质,改变颜料以及改变涂层厚度,其防腐蚀能力与电阻之间皆服从图1的关系。例如成膜物质为聚乙烯缩丁醛,底材为碳钢,颜料为二氧化钛(体积浓度22%),浸两天后涂层电阻降至log R<4,浸泡两周后即观察到大量锈蚀及起泡。若颜料改为红铅(体积浓度16%)浸泡50天log R仍高于8,浸泡6个月也没有观察到腐蚀迹象。
后来其它作者研究了钢表面上有机涂层在NaCl、KCl、稀盐酸、稀硝酸、海水等介质中涂层电阻与腐蚀的关系,所得结果与图1相符[4]。现在一般认为若涂层logR能保持在8以上该涂层防腐性能良好,若log R在6以下防腐性能就不好[1,4]。
3 聚苯胺防腐蚀的“氧化膜机理”
自从1984年发现聚苯胺有防腐蚀作用以来,许多作者先后观察到聚苯胺涂层能使铁、铜等金属的电位明显上升,而且在一定条件下聚苯胺涂层与金属界面之间可生成一层致密的氧化膜(内层为Fe3O4,外层为Fe2O3)。基于以上实验结果,一般认为聚苯胺的优良防腐性能是由于这层氧化膜保护了金属,使其免于生锈。本文称之为聚苯胺涂料防腐蚀的“氧化膜机理”。
在“氧化膜”的共识之下,不同的学者间也有分歧。有人认为导电型聚苯胺(ES)的金属性导致表面电位上升,而且在ES的催化作用下生成了氧化膜[5]。但另外一些学者发现不导电的聚苯胺(EB)[6],甚至苯胺三聚物[7,8]都能使金属电位升高,并生成氧化膜。
4 聚苯胺涂层的电阻及防腐性能
由于可提供较多信息,常用交流阻抗法研究聚苯胺涂层。 当交流阻抗测定结果用Nyquist图表示时,第一个半园直径即代表涂层电阻[9]。若交流阻抗结果用Bode图表示,低频时的交流阻抗即近似等于涂层直流电阻[10]。
Ormcon公司的聚苯胺涂料在NaCl溶液中的logR约4~5[12],单独使用时效果并不好,需要与面漆配合使用[5,11]。 与好的面漆相配合,在5%NaCl溶液中浸140小时涂层log R仍高于7。与差的面漆配合使用,浸泡三小时后log R就低于7。经一千小时浸泡后,前者无可见腐蚀迹象,后者有起泡现象[13]。
面漆好并不意味它的电阻值就高。例如面漆在NaCl溶液中浸了8天之后log R降至5,品牌为PANDA的可溶性聚苯胺涂层log R为3。但二者配合使用,浸8天后log R为8,浸51天后仍高于6[12]。
虽然适当的面漆能大大提高聚苯胺涂料的防腐效果,但是若将其与聚苯胺底漆混合均匀,然后涂于铁表面,则防腐效果大减,比无面漆的聚苯胺涂层还差[14]。
上述结果说明聚苯胺底漆与面漆之间不是简单的加合作用,而是一种“协同作用”(Synergism)[11]。
根据氧化膜机理,聚苯胺涂层本身防腐蚀性能就该很好,难以解释上述种种实验结果。传统腐蚀界对聚苯胺防腐的质疑与此不无关系[15]。有人认为聚苯胺底漆提供氧化膜,而面漆提供对离子及水的高度屏蔽能力。但实验结果显示,面漆本身的电阻不高,因而对离子的屏蔽作用并不强[11,13]。
5 双极性涂层机理
导电聚苯胺是由带正电荷的高分子骨架与带负电荷的掺杂阴离子组成[16],符合阴离子交换剂的结构特征。导电聚苯胺具有阴离子交换性能也已广为人知。最近有人提出聚苯胺在防腐涂料中起阴离子交换剂的作用。聚苯胺涂层是阴离子交换膜,若与阳离子交换膜相配合,形成双极性涂层(Bipolar Coatings),这种涂层对离子穿透具有高度屏蔽能力,具有优良的防腐蚀性能[17]。现简介于下:作者在冷轧板上涂三种不同的涂层:
(1)双极性涂层:底漆用聚苯胺涂料,面漆为含阳离子交换剂的涂料。
(2)单极性涂层:面漆、底漆皆相同,均为聚苯胺涂料。
(3)非极性涂层:面漆、底漆皆相同,为双极性涂层的面漆与底漆的均匀混合物料。
上述三种涂层浸在3.5%NaCl溶液中19天后,用交流阻抗法测出它们的电阻如下:双极性涂层logR=7.8,单极性涂层logR=6.2,非极性涂层logR=3.5。双极性涂层与非极性涂层二者所含成份相同,但一个是聚苯胺底漆与面漆分别涂,另一个是聚苯胺底漆与面漆混合均匀后再涂,二者电阻竟相差2万倍,这说明聚苯胺涂层是阴离子交换膜。因为阳离子交换膜只允许阳离子通过而拒绝阴离子通过。同样,阴离子交换膜只允许阴离子通过而不允许阳离子通过。若两种膜组合在一起(双极性涂层),则阴阳离子皆通 不过,所以电阻最高。若二者均匀地混合在同一涂层内(非极性涂层)则阴、阳离子皆可以通过,所以电阻最低。
作为阴离子交换膜,聚苯胺涂层不允许阳离子通过,所以阻止金属的溶解,从而抑制了腐蚀的阳极反应。由于它允许阴离子通过,环境中的氯离子等阴离子达到金属表面后会加速腐蚀反应,若原来有氧化膜,也会被氯离子破坏[18]。为了阻止阴离子达到金属表面,就必须用一层阳离子交换膜为面漆。在双极性涂层中,这种阴离子膜与阳离子膜之间的相辅相成导致了稳定的高电阻及优良的防腐蚀作用,这就是聚苯胺底漆与面漆间的“协同作用”。
Wessling指出“面漆应具有一种足够的屏蔽能力,而这种屏蔽能力是聚苯胺底漆所不具备的”[5]。根据双极性机理,面漆屏蔽的是阴离子,聚苯胺底漆是阴离子交换膜,显然不可能有这种屏蔽能力。基于聚苯胺涂层的阴离子交换膜性质,作者还讨论了金属表面电位上升及氧化膜的生成等问题。有兴趣的读者,可参考原文。不导电的聚苯胺(EB),及苯胺三聚体均有阴离子交换能力[19],其涂层都是阴离子交换膜[17]。它们所含的阴离子为氢氧根离子(ES的阴离子为酸根离子),这导致EB与ES防腐蚀性能的不同[17]。
对单极性离子交换膜而言,离子交换能力越高则抗腐蚀能力越差[20]。 Zobov等[21]将工业阴、阳离子交换剂分别混入环氧树脂中制成阴、阳离子交换涂料,王周成等[22]用不同含钼化合物与酚醛树脂混合制成阴、阳离子交换涂料,他们都证明双极性涂层具有良好的防腐蚀性能.从开发工业双极性涂料考虑,聚苯胺比其它阴离子交换剂更实用[17]。
6 应用前景
当前最有效的金属防腐蚀颜料仍然是六价铬化物及含铅的化合物。六价铬化合物是致癌物质,铅也是严重污染环境的重金属。世界各国都急切地寻找无毒或低毒的替代物。聚苯胺涂料被看好是新一代环境可接受的高效防腐涂料[23,25]。德国Ormlecon公司制造的聚苯胺涂料似尚未打开市场[26]。本文介绍的聚苯胺双极性涂层防腐蚀机理与传统的腐蚀理论相接轨,应有助于腐蚀界了介这种新型涂料。我国已有数个单位从事聚苯胺涂料的工作。本人试制的聚苯胺防腐涂料已通过500小时盐雾试验,附着力、柔韧性等性能良好,现在正创造条件制备稍大量的样品试用。除防腐蚀外,聚苯胺涂料在防静电、电磁屏蔽等方面有广泛的用途,一旦制造出性能优良使用方便,价格合理的聚苯胺涂料,估计每年有上百亿美元的市场[16,23]。
参考文献
[1] D.Greenfield, D. Scantlebury http://www.umist.ac.uk/corrosion/JCSE/volume3/paper5/V3p5.html.
[2] 虞兆年防腐蚀涂料和涂装,化学工业出版礼北京(1998)
[3] R.C.Bacon,J.J. Smith, and F. MRugg, Ind. Eng.Chem, 40(1948)161
[4] H.Leidheiser,Jr,Progress in Organic Coatings,7(1979)79
[5] B.Wessllng,http:www.umist.ac.uk/corrosion/JCSE/voltumel/paperl5/vlpl5.html.
[6] M.FahlmAn,et al.,alqTlC(1998)1238
[7] Y.Wei.et a1.,US Patent 6,239,251(2001)
[8] T.Lswrence,et a1.,Polymer Preprints,41(2)(2000)1741
[9] G.W.Walter,Corrosion Science,26(1986)681
[10] H.Leidheiser,Jr,J of Coatings Technology,63(1991)
[11] D.E.Tallman,Y.Pae,G.P.Bierwaggen,Corrosion,55(1999)779
[12] P.Li,T.C.Tan,J.Y.Lee,Synthetic Metals,88(1997)237
[13] B.Wessling,ANTAC(1998)1242
[14] S.P.Sitaran et al.,Polymetric Materials Science & Engineering,75(1996)354
[15] a.请参阅参考文献[5]的comnents b.http://www.ormeon.de,进入此网站后seach关键词“Comments”就可找到有关讨论。
[16] 苏慈生, 现代涂料与涂装,01(2001)1
[17] J.Wang,Synthetic Metals,132(2002)53
[18] R.A.Dickie,A.C.Smith,Chemtech, January(1980)31
[19] J.Wang,Synthetic Metals,132(2002)49
[20] U.Ulfvarson and M.Khullar,J.0il col.Chem Assoc.,54(1971)604
[21] E.V,Zobov,Z.V. Mishina,Protection of Metals,19(1984)380
[22] 王周成等,中国腐蚀与防腐学报,17(1997)93
[23] S. Roberts,G. Ondrey,Chemical Engineering,July(1996)44
[24] S. P. Sitaram,J.0. Stoffer,T.J.OKeefe,J.of Coatings Technology,69(1997)65
[25] M.Fahlman,et al.,Polymer Preprint,41(2)(2000)1753
[26] 王光国,全面腐蚀控制,2(2002)23
1 前言
140年前化学家就报导了聚苯胺,但认识到聚苯胺是一种导电高分子材料才只有20多年。聚苯胺在抗静电、电磁屏蔽、有机发光二极管及抗金属腐蚀等方面有诱人的应用前景,因此,是一个热门的研究领域。聚苯胺防腐蚀涉及聚苯胺化学和金属腐蚀科学,现在世界每年发表的有关论文超过一千篇。本文简要介绍聚苯胺涂料防腐蚀机理研究的进展,首先介绍金属防腐蚀的有关知识,然后介绍聚苯胺防腐蚀的氧化膜机理及“双极性涂层”机理,最后讨论聚苯胺涂料的应用前景。
2 有机涂层电阻与其防腐性能的关系
有机涂层的防腐蚀作用曾被认为是将金属表面与环境中的氧气及水隔开。但是半个多世纪以来金属腐蚀研究表明,有机涂层的防腐作用在于阻挡离子的穿透[1,2]。当有机涂层浸在水溶液中时,其电阻越高则离子越难穿透。Baco等人[3]测定了碳钢上300多种有机涂层在海水中的直流电阻R(R=每平方厘米浸没面积的电阻,W)。他们发现,在浸入海水的最初5至10分钟内各种涂层log R约为9。浸泡过程中电阻的变化可分为三类(见图1)。若log R能保持在8以上者,涂层防腐效果良好,若电阻直线迅速下降,则防腐蚀效果差,电阻变化介于上述二者之间的,防腐蚀效果一般。改变成膜物质,改变颜料以及改变涂层厚度,其防腐蚀能力与电阻之间皆服从图1的关系。例如成膜物质为聚乙烯缩丁醛,底材为碳钢,颜料为二氧化钛(体积浓度22%),浸两天后涂层电阻降至log R<4,浸泡两周后即观察到大量锈蚀及起泡。若颜料改为红铅(体积浓度16%)浸泡50天log R仍高于8,浸泡6个月也没有观察到腐蚀迹象。
后来其它作者研究了钢表面上有机涂层在NaCl、KCl、稀盐酸、稀硝酸、海水等介质中涂层电阻与腐蚀的关系,所得结果与图1相符[4]。现在一般认为若涂层logR能保持在8以上该涂层防腐性能良好,若log R在6以下防腐性能就不好[1,4]。
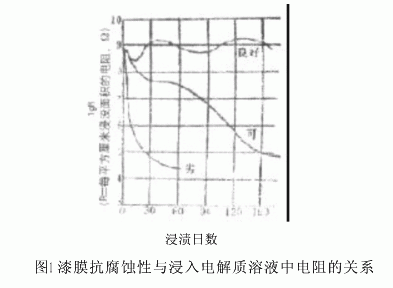
3 聚苯胺防腐蚀的“氧化膜机理”
自从1984年发现聚苯胺有防腐蚀作用以来,许多作者先后观察到聚苯胺涂层能使铁、铜等金属的电位明显上升,而且在一定条件下聚苯胺涂层与金属界面之间可生成一层致密的氧化膜(内层为Fe3O4,外层为Fe2O3)。基于以上实验结果,一般认为聚苯胺的优良防腐性能是由于这层氧化膜保护了金属,使其免于生锈。本文称之为聚苯胺涂料防腐蚀的“氧化膜机理”。
在“氧化膜”的共识之下,不同的学者间也有分歧。有人认为导电型聚苯胺(ES)的金属性导致表面电位上升,而且在ES的催化作用下生成了氧化膜[5]。但另外一些学者发现不导电的聚苯胺(EB)[6],甚至苯胺三聚物[7,8]都能使金属电位升高,并生成氧化膜。
4 聚苯胺涂层的电阻及防腐性能
由于可提供较多信息,常用交流阻抗法研究聚苯胺涂层。 当交流阻抗测定结果用Nyquist图表示时,第一个半园直径即代表涂层电阻[9]。若交流阻抗结果用Bode图表示,低频时的交流阻抗即近似等于涂层直流电阻[10]。
Ormcon公司的聚苯胺涂料在NaCl溶液中的logR约4~5[12],单独使用时效果并不好,需要与面漆配合使用[5,11]。 与好的面漆相配合,在5%NaCl溶液中浸140小时涂层log R仍高于7。与差的面漆配合使用,浸泡三小时后log R就低于7。经一千小时浸泡后,前者无可见腐蚀迹象,后者有起泡现象[13]。
面漆好并不意味它的电阻值就高。例如面漆在NaCl溶液中浸了8天之后log R降至5,品牌为PANDA的可溶性聚苯胺涂层log R为3。但二者配合使用,浸8天后log R为8,浸51天后仍高于6[12]。
虽然适当的面漆能大大提高聚苯胺涂料的防腐效果,但是若将其与聚苯胺底漆混合均匀,然后涂于铁表面,则防腐效果大减,比无面漆的聚苯胺涂层还差[14]。
上述结果说明聚苯胺底漆与面漆之间不是简单的加合作用,而是一种“协同作用”(Synergism)[11]。
根据氧化膜机理,聚苯胺涂层本身防腐蚀性能就该很好,难以解释上述种种实验结果。传统腐蚀界对聚苯胺防腐的质疑与此不无关系[15]。有人认为聚苯胺底漆提供氧化膜,而面漆提供对离子及水的高度屏蔽能力。但实验结果显示,面漆本身的电阻不高,因而对离子的屏蔽作用并不强[11,13]。
5 双极性涂层机理
导电聚苯胺是由带正电荷的高分子骨架与带负电荷的掺杂阴离子组成[16],符合阴离子交换剂的结构特征。导电聚苯胺具有阴离子交换性能也已广为人知。最近有人提出聚苯胺在防腐涂料中起阴离子交换剂的作用。聚苯胺涂层是阴离子交换膜,若与阳离子交换膜相配合,形成双极性涂层(Bipolar Coatings),这种涂层对离子穿透具有高度屏蔽能力,具有优良的防腐蚀性能[17]。现简介于下:作者在冷轧板上涂三种不同的涂层:
(1)双极性涂层:底漆用聚苯胺涂料,面漆为含阳离子交换剂的涂料。
(2)单极性涂层:面漆、底漆皆相同,均为聚苯胺涂料。
(3)非极性涂层:面漆、底漆皆相同,为双极性涂层的面漆与底漆的均匀混合物料。
上述三种涂层浸在3.5%NaCl溶液中19天后,用交流阻抗法测出它们的电阻如下:双极性涂层logR=7.8,单极性涂层logR=6.2,非极性涂层logR=3.5。双极性涂层与非极性涂层二者所含成份相同,但一个是聚苯胺底漆与面漆分别涂,另一个是聚苯胺底漆与面漆混合均匀后再涂,二者电阻竟相差2万倍,这说明聚苯胺涂层是阴离子交换膜。因为阳离子交换膜只允许阳离子通过而拒绝阴离子通过。同样,阴离子交换膜只允许阴离子通过而不允许阳离子通过。若两种膜组合在一起(双极性涂层),则阴阳离子皆通 不过,所以电阻最高。若二者均匀地混合在同一涂层内(非极性涂层)则阴、阳离子皆可以通过,所以电阻最低。
作为阴离子交换膜,聚苯胺涂层不允许阳离子通过,所以阻止金属的溶解,从而抑制了腐蚀的阳极反应。由于它允许阴离子通过,环境中的氯离子等阴离子达到金属表面后会加速腐蚀反应,若原来有氧化膜,也会被氯离子破坏[18]。为了阻止阴离子达到金属表面,就必须用一层阳离子交换膜为面漆。在双极性涂层中,这种阴离子膜与阳离子膜之间的相辅相成导致了稳定的高电阻及优良的防腐蚀作用,这就是聚苯胺底漆与面漆间的“协同作用”。
Wessling指出“面漆应具有一种足够的屏蔽能力,而这种屏蔽能力是聚苯胺底漆所不具备的”[5]。根据双极性机理,面漆屏蔽的是阴离子,聚苯胺底漆是阴离子交换膜,显然不可能有这种屏蔽能力。基于聚苯胺涂层的阴离子交换膜性质,作者还讨论了金属表面电位上升及氧化膜的生成等问题。有兴趣的读者,可参考原文。不导电的聚苯胺(EB),及苯胺三聚体均有阴离子交换能力[19],其涂层都是阴离子交换膜[17]。它们所含的阴离子为氢氧根离子(ES的阴离子为酸根离子),这导致EB与ES防腐蚀性能的不同[17]。
对单极性离子交换膜而言,离子交换能力越高则抗腐蚀能力越差[20]。 Zobov等[21]将工业阴、阳离子交换剂分别混入环氧树脂中制成阴、阳离子交换涂料,王周成等[22]用不同含钼化合物与酚醛树脂混合制成阴、阳离子交换涂料,他们都证明双极性涂层具有良好的防腐蚀性能.从开发工业双极性涂料考虑,聚苯胺比其它阴离子交换剂更实用[17]。
6 应用前景
当前最有效的金属防腐蚀颜料仍然是六价铬化物及含铅的化合物。六价铬化合物是致癌物质,铅也是严重污染环境的重金属。世界各国都急切地寻找无毒或低毒的替代物。聚苯胺涂料被看好是新一代环境可接受的高效防腐涂料[23,25]。德国Ormlecon公司制造的聚苯胺涂料似尚未打开市场[26]。本文介绍的聚苯胺双极性涂层防腐蚀机理与传统的腐蚀理论相接轨,应有助于腐蚀界了介这种新型涂料。我国已有数个单位从事聚苯胺涂料的工作。本人试制的聚苯胺防腐涂料已通过500小时盐雾试验,附着力、柔韧性等性能良好,现在正创造条件制备稍大量的样品试用。除防腐蚀外,聚苯胺涂料在防静电、电磁屏蔽等方面有广泛的用途,一旦制造出性能优良使用方便,价格合理的聚苯胺涂料,估计每年有上百亿美元的市场[16,23]。
参考文献
[1] D.Greenfield, D. Scantlebury http://www.umist.ac.uk/corrosion/JCSE/volume3/paper5/V3p5.html.
[2] 虞兆年防腐蚀涂料和涂装,化学工业出版礼北京(1998)
[3] R.C.Bacon,J.J. Smith, and F. MRugg, Ind. Eng.Chem, 40(1948)161
[4] H.Leidheiser,Jr,Progress in Organic Coatings,7(1979)79
[5] B.Wessllng,http:www.umist.ac.uk/corrosion/JCSE/voltumel/paperl5/vlpl5.html.
[6] M.FahlmAn,et al.,alqTlC(1998)1238
[7] Y.Wei.et a1.,US Patent 6,239,251(2001)
[8] T.Lswrence,et a1.,Polymer Preprints,41(2)(2000)1741
[9] G.W.Walter,Corrosion Science,26(1986)681
[10] H.Leidheiser,Jr,J of Coatings Technology,63(1991)
[11] D.E.Tallman,Y.Pae,G.P.Bierwaggen,Corrosion,55(1999)779
[12] P.Li,T.C.Tan,J.Y.Lee,Synthetic Metals,88(1997)237
[13] B.Wessling,ANTAC(1998)1242
[14] S.P.Sitaran et al.,Polymetric Materials Science & Engineering,75(1996)354
[15] a.请参阅参考文献[5]的comnents b.http://www.ormeon.de,进入此网站后seach关键词“Comments”就可找到有关讨论。
[16] 苏慈生, 现代涂料与涂装,01(2001)1
[17] J.Wang,Synthetic Metals,132(2002)53
[18] R.A.Dickie,A.C.Smith,Chemtech, January(1980)31
[19] J.Wang,Synthetic Metals,132(2002)49
[20] U.Ulfvarson and M.Khullar,J.0il col.Chem Assoc.,54(1971)604
[21] E.V,Zobov,Z.V. Mishina,Protection of Metals,19(1984)380
[22] 王周成等,中国腐蚀与防腐学报,17(1997)93
[23] S. Roberts,G. Ondrey,Chemical Engineering,July(1996)44
[24] S. P. Sitaram,J.0. Stoffer,T.J.OKeefe,J.of Coatings Technology,69(1997)65
[25] M.Fahlman,et al.,Polymer Preprint,41(2)(2000)1753
[26] 王光国,全面腐蚀控制,2(2002)23
相关文章
发布评论