涂料技术
栏污栅钢质锁锭涂层翻新工艺
栏污栅钢质锁锭涂层翻新工艺
李敏风 ( 上海斐然国际贸易有限公司 200136)
摘要:分析了宜昌长江电力公司水工检修厂栏污栅锁锭锈蚀严重的原因;提出了以 ROVAL( 冷镀锌 ) 为底涂的复合涂层的涂装设计配套,列举了它的优异性能,并在涂装施工中抓住了 4 个工艺关键,取得了 较好的涂层质量。
关键词:栏污栅锁锭;冷镀锌复合涂层;涂装施工
概况
2005 年春,宜昌长江电力公司水工检修厂承担了二滩电厂 42 只约 600 m 2 栏污栅钢质锁锭涂层的维修、更新业务。上海 ROVAL 富锌涂料公司配合水工检修厂首先调查了锁锭涂层的现状:锁锭表面锈蚀严重,锈蚀面积达到 30 %以上,不少部位涂层已经脱落。锁锭涂层破坏、锈蚀严重的原因有:
(1) 自然环境恶劣。
由于水位变化或栏污栅启闭,锁锭常处于干湿交替环境中;有时受到高压水流的冲击和泥沙、漂 浮物等的摩擦;平时还要受到日晒雨淋、潮湿污染 空气的作用,所处的自然环境十分恶劣。
(2) 钢材及结构因素。
锁锭系钢结构件。钢质 Q235 ,系热轨钢材,耐腐蚀性能差;加上锁锭在制作焊接时产生的应力,所以锁锭的电焊缝及结构上缝隙处等,特别容易发生锈蚀。
(3) 工作应力变形的影响。
锁锭在工作时,受到交变的拉应力,且受力不均匀,易造成锁锭应力集中和变形。应力和变形越大,腐蚀越甚。
(4) 原涂层配套耐腐蚀性能差。
二滩电厂锁锭第一次涂装在 1983 年。当时同栏污栅相同,由制造厂在安装前进行喷锌处理。到 1995 年,发现涂层锈蚀十分严重,打磨去除旧涂层后,用氯化橡胶铝粉底面漆重新涂装。由于该涂装配套防腐性能不佳,造成目前锈蚀严重的局面。
1 涂装设计配套及设计依据
业主对二滩电厂锁锭涂层使用年限要求在 l5 年。按 ISO 12944 标准和冷镀锌材料 ROVAL 的优良特性,设计的涂装配套见表 1 。
表 1 配套涂层的设计依据有:
1 . 1 ISO 12944~1998 国际标准
这是目前国际上关于涂装设计最先进的文件。在锁锭的涂装设计中,主要引用了 ISO l2944 — 2 “关于腐蚀环境的分类和定义”和 ISO l2944 — 5 “涂层配套及规定膜厚”两部分。同时根据 ISO l2944 — 5 的规定,防腐年限并不等同于“担保时间”。它只 是类似于工程设计中的设计寿命,也就是从涂装施 工到涂层第一次大修的年限。在防腐年限之内,还 需进行定期的检查和小范围的维修。 15 年后,锈蚀等级达到 ISO 4628 — 3 的 Ri3 级。即锈蚀面积约为 1 %。腐蚀环境、使用寿命和漆膜厚度的关系见表 2 。

表 1 锁锭涂装配套
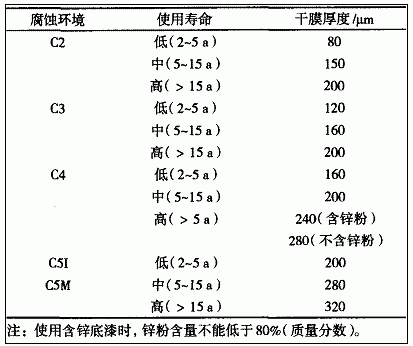
表 2 ISO 12944 中腐蚀环境、使用寿命和漆膜厚度的关系
1 . 2 中华人民共和国行业标准 SL 105-95
SL 105-95 “水工金属结构防腐蚀规范”中,“ D 2 ” 半浸没状态( 干湿交替 ) 结构涂料配套方案见 表 3 。
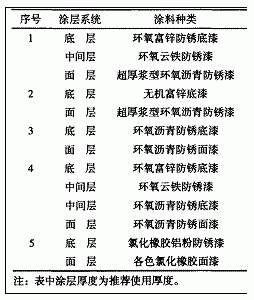
表 3 水下结构涂料配套参考
1 . 3 ISO 14713-1998 热 ( 电弧 ) 喷涂防腐蚀涂层体系 ( 表 4)
表 4 ISO 14713 热喷涂防腐蚀涂层体系
2 涂层的优异特性
本配套设计采用了冷镀锌 ROVAL 作重防腐涂 料的底层,使复合涂层具有下列优异特性。
2 . 1 防腐蚀性能优异
ROVAL 干膜涂层中锌粉含量高达 96 %,锌粉纯度 99 . 99 %以上,锌粉粒度为 3~6 μ m 。对钢材来说,它同热浸镀锌层及热 ( 电弧 ) 喷锌镀层具一样优异的防腐蚀性能来自于两个方面:一是具有电 化学保护作用,亦称阴极保护作用;其二是锌腐蚀沉淀物的屏蔽保护作用使涂层亦具有自修复性。根 据同济大学 蒋演德 教授和台湾镀锌协会等的经验公式,单独成膜冷镀锌材料涂层使用寿命的估算公式为: n=(G / g)X k
其中 n —— 耐用年数;
G ——锌层总附着量,其中 1 μ m 锌层涂布量约为 7 . 2 g / m2 ;
g ——年腐蚀量 ( 根据不同地区大气环境及不同使用部位决定,可参考 ISO 12944 标准——腐蚀 定义和环境表取对应数据,以 30 g / m 2 计算 ) ;
k ——折减系数,冷镀锌一般以 0 . 8 计。
60 μ m ROVAL 防护年限为:

更值得一提的是, ROVAL 涂层在局部遭到破坏时,有“自修复”作用,对防腐蚀能力无大的影响。
2 . 2 与重防腐涂料配套性能良好
除醇酸等油性涂料外, ROVAL 涂层可以与环 氧类中层漆,丙烯酸、聚氨酯、氟碳等面漆配套,并 具有国家级的检测报告,配套性能良好。
根据荷兰热浸 ( 喷 ) 锌研究所在长达 20 年的研 究中得出的等加效应规律,即在镀锌层表面复涂重防腐涂料后,复合涂层的防护年限为锌层防护年限 (A) 与重防腐涂料防护年限 (B) 之和的 1 . 5 ~ 2 . 4 倍。“ ROVAL ”及“锌加”等冷镀锌材料的应用历史也证 实了这一点。
锁锭涂装配套的防腐年限为:
ROVAL60 μ m : 10 a
环氧云铁中层漆 + 氯化橡胶面漆: 2 a
复合涂层: (10+2) × 1 . 5= 18 a
因此设计涂层的防腐寿命符合业主对涂层使用寿命的规定。
2 . 3 环保效应
环保是当前涂料、涂装行业的头等大事。在锁锭的涂装配套和涂装工艺中充分考虑到这个因素, 表现在:
(1)ROVAL 和配套的重防腐涂料中不含 Ph 、 Cr 、 Hg 等重金属成分。重防腐涂料的防锈颜料低 毒、低污染;
(2)ROVAL 稀释剂和溶剂内不含苯、二甲苯、甲苯、异氰酸酯等毒性大的有机溶剂。
(3) 锁锭配套中之 ROVAL 和重防腐涂料均为 厚膜型材料, VOC 低,触变性能好,经充分搅拌后可少加或不加稀释剂,即可涂装施工。由于高固体分,一次无气喷涂可达到较高膜厚,这些均为有机涂料的环保效应。
2 . 4 涂装工艺的可行性
锁锭涂装配套必须适应长江水工机械厂的施工条件。如锁锭表面不能进行喷砂处理,作底涂的 ROVAL 涂层必须能涂刷在打磨的表面; ROVAL 和环氧云铁、氯化橡胶面漆可在现场涂装,自然干燥等等。
3 施工工艺
“三分涂料、七分涂装”,只有保证涂装施工工 艺顺利进行,才能发挥涂料配套的优异性能;才能获得优秀的涂层质量。在涂层设计时,我们同时设计了涂装工艺。在锁锭维修的涂装过程中,不断修正、提高,以达到完善的目的。
3 . 1 工艺流程
锁锭表面打磨除锈除旧漆膜等→吹去灰尘,去油、干燥表面等→涂刷第 1 道冷镀锌材料→涂刷第 2 道冷镀锌材料→喷涂第 1 道稀释 20 %~ 30 %的环氧云铁中间漆→第 2 道环氧云铁中间漆→ 2 道氯化橡胶面漆 → 质量检查 → 修补 → 交验。
3 . 2 表面处理
鉴于长江水工检修厂涂装工艺的条件,对锁锭涂装前的表面处理采取了 2 条措施:
(1) 风 ( 电 ) 动工具及手工打磨。
用风 ( 电 ) 动钢丝刷、砂轮、齿子、铲子等去除 锁锭上的旧漆膜、铁锈、氧化皮和其他异杂物,直至露出金属的本色。
由于电焊缝部位是钢构件最易锈蚀的部位,在对锁锭的电焊缝进行表面处理时,工人应格外仔细,去除遗留的“飞溅”、“焊渣”等。
(2) 去油污。
锁锭经过长期使用,油污严重。在生产实践中, 水工检修厂采用了有机溶剂,如 200 号溶剂汽油等擦洗表面的办法,彻底去除油污。在工艺上为先打磨除锈,后去油的顺序。
经过上述两项措施使锁锭表面清洁度达到 ISO8501 — 1 的 St 3 级;电焊缝部位清洁度达到 ISO 8501 — 1 的 St 2 级。
3 . 3 涂装工艺
在锁锭的涂装工艺中,我们抓了 4 个技术关键,切实保证了涂层质量。
(1) 冷镀锌 ROVAL 的搅拌与稀释。
ROVAL 锌粉含量高,比常规涂料容易沉淀。在 涂装施工前,如不搅拌均匀,使上层涂料锌粉含量不足,涂层防锈性能差;下层涂料树脂含量低,涂层附着力差;所以必须进行机械搅拌, ROVAL 触 变性能好,极易搅拌均匀,一般每隔 0 . 5 h 搅拌 1 次,以保证涂料的施工质量。
锁锭的涂装采用手工涂刷法。为使 ROVAL 涂膜具有一定的渗透性和流平性,需加入 <5 %的稀 释剂。稀释剂必须专用,与其他品牌冷镀锌材料、 重防腐涂料稀释剂不可混用。
在工艺步骤上,应为搅拌一稀释一搅拌。
(2) 重视冷镀锌材料涂层的封闭处理。
由于 ROVAL 干膜中锌粉含量高达 96 %,又多为球形锌粉,涂膜中粘结剂不能填满锌粉颗粒间的孔隙,具有较高的孔隙率,因此应选择合适的涂料 封闭后,才能复涂重防腐涂料。在栏污栅锁锭涂装 中,我们用环氧云铁中层漆,稀释 30 %~ 40 %后,满涂一层,使之充分渗透,达到填封孔 隙之目的,待固化后再复涂一层环氧云铁中层漆,收到了较好的效果。
(3) 加强电焊缝的预涂装。
电焊缝是锁锭最易锈蚀的部位。因此在电焊缝表面处理完毕后,我们对焊缝进行预涂装,预涂材料为 ROVAL ,稀释 5 %,采用刷涂办法,以增加焊 缝的防腐蚀能力。
(4) 涂装环境条件。
长江电力厂栏污栅锁锭涂装期间,正值梅雨季节。在气温上适合 ROVAL 及重防腐涂料的涂装,但 由于雨水多相对湿度较高,为保证涂装质量,施工 中,还是坚持下列原则:在相对湿度小于 85 %、钢板温度大于露点温度 3 ℃ 时,冷镀锌材料与重防腐涂料才开始涂装。
4 涂装质量
由于涂装配套设计的先进性,加上涂装施工中坚持了 4 个关键,使锁锭的涂膜质量十分优异,它体现在 3 个方面:
(1) 漆膜外观质量:漆膜平整、光滑,由于配 套性能良好,无层间剥离、起泡、针孔、流挂、裂纹 等漆膜弊病出现。
(2) 膜厚质量:经检测,能保证各层涂层的膜厚要求,特别是 ROVAL 涂层的设计规定膜厚,达到 60 μ m 。总的膜厚质量达到两个 85 %的要求,即 85 % 的检测点膜厚,能达到规定的要求,不到规定膜厚 检测点的膜厚检测值,能超过规定膜厚的 85 %。
(3) 附着力:在现场,我们用划格法对各涂层的附着力进行检测,均能达到 GB 296-88 标准的 0 ~ 1 级。
李敏风 ( 上海斐然国际贸易有限公司 200136)
摘要:分析了宜昌长江电力公司水工检修厂栏污栅锁锭锈蚀严重的原因;提出了以 ROVAL( 冷镀锌 ) 为底涂的复合涂层的涂装设计配套,列举了它的优异性能,并在涂装施工中抓住了 4 个工艺关键,取得了 较好的涂层质量。
关键词:栏污栅锁锭;冷镀锌复合涂层;涂装施工
概况
2005 年春,宜昌长江电力公司水工检修厂承担了二滩电厂 42 只约 600 m 2 栏污栅钢质锁锭涂层的维修、更新业务。上海 ROVAL 富锌涂料公司配合水工检修厂首先调查了锁锭涂层的现状:锁锭表面锈蚀严重,锈蚀面积达到 30 %以上,不少部位涂层已经脱落。锁锭涂层破坏、锈蚀严重的原因有:
(1) 自然环境恶劣。
由于水位变化或栏污栅启闭,锁锭常处于干湿交替环境中;有时受到高压水流的冲击和泥沙、漂 浮物等的摩擦;平时还要受到日晒雨淋、潮湿污染 空气的作用,所处的自然环境十分恶劣。
(2) 钢材及结构因素。
锁锭系钢结构件。钢质 Q235 ,系热轨钢材,耐腐蚀性能差;加上锁锭在制作焊接时产生的应力,所以锁锭的电焊缝及结构上缝隙处等,特别容易发生锈蚀。
(3) 工作应力变形的影响。
锁锭在工作时,受到交变的拉应力,且受力不均匀,易造成锁锭应力集中和变形。应力和变形越大,腐蚀越甚。
(4) 原涂层配套耐腐蚀性能差。
二滩电厂锁锭第一次涂装在 1983 年。当时同栏污栅相同,由制造厂在安装前进行喷锌处理。到 1995 年,发现涂层锈蚀十分严重,打磨去除旧涂层后,用氯化橡胶铝粉底面漆重新涂装。由于该涂装配套防腐性能不佳,造成目前锈蚀严重的局面。
1 涂装设计配套及设计依据
业主对二滩电厂锁锭涂层使用年限要求在 l5 年。按 ISO 12944 标准和冷镀锌材料 ROVAL 的优良特性,设计的涂装配套见表 1 。
表 1 配套涂层的设计依据有:
1 . 1 ISO 12944~1998 国际标准
这是目前国际上关于涂装设计最先进的文件。在锁锭的涂装设计中,主要引用了 ISO l2944 — 2 “关于腐蚀环境的分类和定义”和 ISO l2944 — 5 “涂层配套及规定膜厚”两部分。同时根据 ISO l2944 — 5 的规定,防腐年限并不等同于“担保时间”。它只 是类似于工程设计中的设计寿命,也就是从涂装施 工到涂层第一次大修的年限。在防腐年限之内,还 需进行定期的检查和小范围的维修。 15 年后,锈蚀等级达到 ISO 4628 — 3 的 Ri3 级。即锈蚀面积约为 1 %。腐蚀环境、使用寿命和漆膜厚度的关系见表 2 。

表 1 锁锭涂装配套
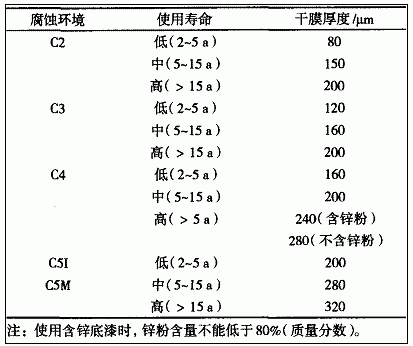
表 2 ISO 12944 中腐蚀环境、使用寿命和漆膜厚度的关系
1 . 2 中华人民共和国行业标准 SL 105-95
SL 105-95 “水工金属结构防腐蚀规范”中,“ D 2 ” 半浸没状态( 干湿交替 ) 结构涂料配套方案见 表 3 。
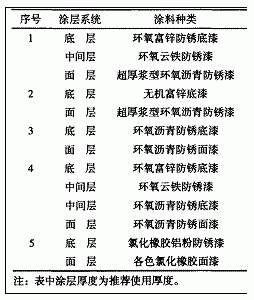
表 3 水下结构涂料配套参考
1 . 3 ISO 14713-1998 热 ( 电弧 ) 喷涂防腐蚀涂层体系 ( 表 4)
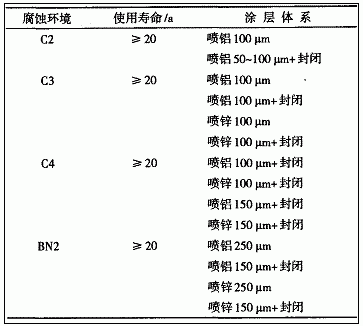
表 4 ISO 14713 热喷涂防腐蚀涂层体系
2 涂层的优异特性
本配套设计采用了冷镀锌 ROVAL 作重防腐涂 料的底层,使复合涂层具有下列优异特性。
2 . 1 防腐蚀性能优异
ROVAL 干膜涂层中锌粉含量高达 96 %,锌粉纯度 99 . 99 %以上,锌粉粒度为 3~6 μ m 。对钢材来说,它同热浸镀锌层及热 ( 电弧 ) 喷锌镀层具一样优异的防腐蚀性能来自于两个方面:一是具有电 化学保护作用,亦称阴极保护作用;其二是锌腐蚀沉淀物的屏蔽保护作用使涂层亦具有自修复性。根 据同济大学 蒋演德 教授和台湾镀锌协会等的经验公式,单独成膜冷镀锌材料涂层使用寿命的估算公式为: n=(G / g)X k
其中 n —— 耐用年数;
G ——锌层总附着量,其中 1 μ m 锌层涂布量约为 7 . 2 g / m2 ;
g ——年腐蚀量 ( 根据不同地区大气环境及不同使用部位决定,可参考 ISO 12944 标准——腐蚀 定义和环境表取对应数据,以 30 g / m 2 计算 ) ;
k ——折减系数,冷镀锌一般以 0 . 8 计。
60 μ m ROVAL 防护年限为:

更值得一提的是, ROVAL 涂层在局部遭到破坏时,有“自修复”作用,对防腐蚀能力无大的影响。
2 . 2 与重防腐涂料配套性能良好
除醇酸等油性涂料外, ROVAL 涂层可以与环 氧类中层漆,丙烯酸、聚氨酯、氟碳等面漆配套,并 具有国家级的检测报告,配套性能良好。
根据荷兰热浸 ( 喷 ) 锌研究所在长达 20 年的研 究中得出的等加效应规律,即在镀锌层表面复涂重防腐涂料后,复合涂层的防护年限为锌层防护年限 (A) 与重防腐涂料防护年限 (B) 之和的 1 . 5 ~ 2 . 4 倍。“ ROVAL ”及“锌加”等冷镀锌材料的应用历史也证 实了这一点。
锁锭涂装配套的防腐年限为:
ROVAL60 μ m : 10 a
环氧云铁中层漆 + 氯化橡胶面漆: 2 a
复合涂层: (10+2) × 1 . 5= 18 a
因此设计涂层的防腐寿命符合业主对涂层使用寿命的规定。
2 . 3 环保效应
环保是当前涂料、涂装行业的头等大事。在锁锭的涂装配套和涂装工艺中充分考虑到这个因素, 表现在:
(1)ROVAL 和配套的重防腐涂料中不含 Ph 、 Cr 、 Hg 等重金属成分。重防腐涂料的防锈颜料低 毒、低污染;
(2)ROVAL 稀释剂和溶剂内不含苯、二甲苯、甲苯、异氰酸酯等毒性大的有机溶剂。
(3) 锁锭配套中之 ROVAL 和重防腐涂料均为 厚膜型材料, VOC 低,触变性能好,经充分搅拌后可少加或不加稀释剂,即可涂装施工。由于高固体分,一次无气喷涂可达到较高膜厚,这些均为有机涂料的环保效应。
2 . 4 涂装工艺的可行性
锁锭涂装配套必须适应长江水工机械厂的施工条件。如锁锭表面不能进行喷砂处理,作底涂的 ROVAL 涂层必须能涂刷在打磨的表面; ROVAL 和环氧云铁、氯化橡胶面漆可在现场涂装,自然干燥等等。
3 施工工艺
“三分涂料、七分涂装”,只有保证涂装施工工 艺顺利进行,才能发挥涂料配套的优异性能;才能获得优秀的涂层质量。在涂层设计时,我们同时设计了涂装工艺。在锁锭维修的涂装过程中,不断修正、提高,以达到完善的目的。
3 . 1 工艺流程
锁锭表面打磨除锈除旧漆膜等→吹去灰尘,去油、干燥表面等→涂刷第 1 道冷镀锌材料→涂刷第 2 道冷镀锌材料→喷涂第 1 道稀释 20 %~ 30 %的环氧云铁中间漆→第 2 道环氧云铁中间漆→ 2 道氯化橡胶面漆 → 质量检查 → 修补 → 交验。
3 . 2 表面处理
鉴于长江水工检修厂涂装工艺的条件,对锁锭涂装前的表面处理采取了 2 条措施:
(1) 风 ( 电 ) 动工具及手工打磨。
用风 ( 电 ) 动钢丝刷、砂轮、齿子、铲子等去除 锁锭上的旧漆膜、铁锈、氧化皮和其他异杂物,直至露出金属的本色。
由于电焊缝部位是钢构件最易锈蚀的部位,在对锁锭的电焊缝进行表面处理时,工人应格外仔细,去除遗留的“飞溅”、“焊渣”等。
(2) 去油污。
锁锭经过长期使用,油污严重。在生产实践中, 水工检修厂采用了有机溶剂,如 200 号溶剂汽油等擦洗表面的办法,彻底去除油污。在工艺上为先打磨除锈,后去油的顺序。
经过上述两项措施使锁锭表面清洁度达到 ISO8501 — 1 的 St 3 级;电焊缝部位清洁度达到 ISO 8501 — 1 的 St 2 级。
3 . 3 涂装工艺
在锁锭的涂装工艺中,我们抓了 4 个技术关键,切实保证了涂层质量。
(1) 冷镀锌 ROVAL 的搅拌与稀释。
ROVAL 锌粉含量高,比常规涂料容易沉淀。在 涂装施工前,如不搅拌均匀,使上层涂料锌粉含量不足,涂层防锈性能差;下层涂料树脂含量低,涂层附着力差;所以必须进行机械搅拌, ROVAL 触 变性能好,极易搅拌均匀,一般每隔 0 . 5 h 搅拌 1 次,以保证涂料的施工质量。
锁锭的涂装采用手工涂刷法。为使 ROVAL 涂膜具有一定的渗透性和流平性,需加入 <5 %的稀 释剂。稀释剂必须专用,与其他品牌冷镀锌材料、 重防腐涂料稀释剂不可混用。
在工艺步骤上,应为搅拌一稀释一搅拌。
(2) 重视冷镀锌材料涂层的封闭处理。
由于 ROVAL 干膜中锌粉含量高达 96 %,又多为球形锌粉,涂膜中粘结剂不能填满锌粉颗粒间的孔隙,具有较高的孔隙率,因此应选择合适的涂料 封闭后,才能复涂重防腐涂料。在栏污栅锁锭涂装 中,我们用环氧云铁中层漆,稀释 30 %~ 40 %后,满涂一层,使之充分渗透,达到填封孔 隙之目的,待固化后再复涂一层环氧云铁中层漆,收到了较好的效果。
(3) 加强电焊缝的预涂装。
电焊缝是锁锭最易锈蚀的部位。因此在电焊缝表面处理完毕后,我们对焊缝进行预涂装,预涂材料为 ROVAL ,稀释 5 %,采用刷涂办法,以增加焊 缝的防腐蚀能力。
(4) 涂装环境条件。
长江电力厂栏污栅锁锭涂装期间,正值梅雨季节。在气温上适合 ROVAL 及重防腐涂料的涂装,但 由于雨水多相对湿度较高,为保证涂装质量,施工 中,还是坚持下列原则:在相对湿度小于 85 %、钢板温度大于露点温度 3 ℃ 时,冷镀锌材料与重防腐涂料才开始涂装。
4 涂装质量
由于涂装配套设计的先进性,加上涂装施工中坚持了 4 个关键,使锁锭的涂膜质量十分优异,它体现在 3 个方面:
(1) 漆膜外观质量:漆膜平整、光滑,由于配 套性能良好,无层间剥离、起泡、针孔、流挂、裂纹 等漆膜弊病出现。
(2) 膜厚质量:经检测,能保证各层涂层的膜厚要求,特别是 ROVAL 涂层的设计规定膜厚,达到 60 μ m 。总的膜厚质量达到两个 85 %的要求,即 85 % 的检测点膜厚,能达到规定的要求,不到规定膜厚 检测点的膜厚检测值,能超过规定膜厚的 85 %。
(3) 附着力:在现场,我们用划格法对各涂层的附着力进行检测,均能达到 GB 296-88 标准的 0 ~ 1 级。
下一篇:耐候性粉末涂料种类及性能介绍
相关文章
发布评论