涂料技术
研究高耐候性聚硅氧烷涂料的制备
2结果与讨论
2.1氨基硅烷固化剂用量的影响
按表1配方配制聚硅氧烷色漆,并用KH550固化,组分A/KH550质量比分别为10∶1.0和13.9∶1.0。
性能测试显示:涂层60°光泽83,铅笔硬度为2H,抗冲击性50cm通过。图1为相应聚硅氧烷涂层的人工加速老化结果。
2.1氨基硅烷固化剂用量的影响
按表1配方配制聚硅氧烷色漆,并用KH550固化,组分A/KH550质量比分别为10∶1.0和13.9∶1.0。
性能测试显示:涂层60°光泽83,铅笔硬度为2H,抗冲击性50cm通过。图1为相应聚硅氧烷涂层的人工加速老化结果。
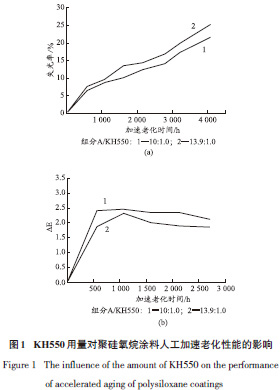
图1 KH550用量对聚硅氧烷涂料人工加速老化性能的影响
由图1(a)可见:涂层的失光率随着老化时间的增加而增大,当组分A/KH550比例为10∶1.0时,老化约2900h后失光率大于15%(即失光2级),而当组分A/KH550比例为13.9∶1.0时,老化约2300h后失光率大于15%。这表明KH550用量增加,有利于保光性的提高,主要是由于涂层中硅含量增加所致。由KH550的分子式(H2N(CH2)3Si(OC2H5)3,相对分子质量221.4g/moL)可知,其硅含量为12.6%,但若考虑其在湿固化过程中3个乙氧基团完全脱除,则其硅含量达29.2%,远高于改性聚硅氧烷树脂中的硅含量(13.5%),因此,KH550用量增加有利于提高固化涂层中的硅含量。图1(b)显示:在老化初期,涂层的色差迅速增加,其后基本保持不变或略有下降,且随KH550用量增加,老化变色增大,与失光率的结果正好相反,因老化变色主要是由固化剂中的氨基所致。另外,2个样板的最大老化色差均小于3.0(即1级变色),符合使用要求。
用ZH1170固化聚硅氧烷涂料,组分A/ZH1170质量比分别为10∶0.77、10∶1.0、10∶1.32。性能测试表明:涂层均具有较好的柔韧性(50cm通过)、耐溶剂性(丙酮擦拭200次通过)和硬度(2H或3H),60°光泽89。图2为ZH1170用量对涂层耐老化结果的影响。
用ZH1170固化聚硅氧烷涂料,组分A/ZH1170质量比分别为10∶0.77、10∶1.0、10∶1.32。性能测试表明:涂层均具有较好的柔韧性(50cm通过)、耐溶剂性(丙酮擦拭200次通过)和硬度(2H或3H),60°光泽89。图2为ZH1170用量对涂层耐老化结果的影响。
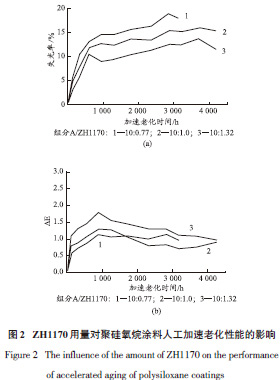
图2 ZH1170用量对聚硅氧烷涂料人工加速老化性能的影响
由图2(a)可见:在老化初期,涂层失光迅速增加,但在涂层老化500h后,涂层失光缓慢,这种失光除了涂层树脂本身老化外,还有部分原因是涂层表面出现了积灰,若将灰尘擦除,涂层的失光率有较大降低(见老化4240h的数据点)。另外,图2(a)显示:ZH1170用量增加,涂层失光率减小,在组分A/ZH1170质量比为10∶1.0和10∶1.32时,老化4200h后,涂层的失光率仍小于15%,满足面漆的使用要求。图2(b)的老化变色曲线显示:色差在老化初期较快增大,在1000h时达最大值,其后随着老化时间的增加,色差不变或略有减小。当ZH1170用量增加时,老化变色增大,与光泽变化规律相反。在老化较长时间时,3个样板的变色逐步趋于一致。因此,ZH1170用量与前述KH550用量对改性聚硅氧烷树脂涂料的影响规律一致。另外,图2中3个样板的老化变色均小于1.5,即涂层在老化4000h以上时也未发生变色现象,优于KH550固化的涂料体系。
如上所述,从人工加速老化结果看,氨基硅烷固化剂的用量增加有利于涂层的耐候性。但是,氨基硅烷固化剂用量过多会导致涂层柔韧性下降,涂料可施工期变短,因此,通过增加氨基硅烷固化剂用量来提高涂层耐候性仍受到一定的限制。
如上所述,从人工加速老化结果看,氨基硅烷固化剂的用量增加有利于涂层的耐候性。但是,氨基硅烷固化剂用量过多会导致涂层柔韧性下降,涂料可施工期变短,因此,通过增加氨基硅烷固化剂用量来提高涂层耐候性仍受到一定的限制。
相关文章
发布评论