涂料技术
研究热固性氟粉末涂料的制备及其应用
4.2.2除锈
除去钢铁基材表面锈垢,可以有效延长涂膜使用寿命,这一点已经得到人们的认可。除锈方法包括手工打磨除锈、机械除锈、喷射除锈和化学除锈4种,其中化学除锈也称为酸洗,是以酸溶液促使工件表面锈层发生化学变化,并溶解在酸液中而达到除锈目的。
4.2.3磷化
磷化处理是用铁、锰、锌、铬的正磷酸盐溶液处理金属工件,能在金属工件表面形成一层不溶性磷酸盐保护膜,该薄膜可提高金属工件的防腐蚀性和绝缘性。现在应用最广的磷化处理方法是化学磷化,即钢铁工件在磷化液中通过化学反应得到磷化膜,此外还有电化学磷化方法。常温磷化反应机理:当被清洗过的钢铁表面一接触到磷化液后首先发生铁溶解,如反应式(1)。在钢铁表面,处理液的pH值升高,进行化学反应,在钢铁表面析出磷酸锌膜,如反应式(2)和(3)。
除去钢铁基材表面锈垢,可以有效延长涂膜使用寿命,这一点已经得到人们的认可。除锈方法包括手工打磨除锈、机械除锈、喷射除锈和化学除锈4种,其中化学除锈也称为酸洗,是以酸溶液促使工件表面锈层发生化学变化,并溶解在酸液中而达到除锈目的。
4.2.3磷化
磷化处理是用铁、锰、锌、铬的正磷酸盐溶液处理金属工件,能在金属工件表面形成一层不溶性磷酸盐保护膜,该薄膜可提高金属工件的防腐蚀性和绝缘性。现在应用最广的磷化处理方法是化学磷化,即钢铁工件在磷化液中通过化学反应得到磷化膜,此外还有电化学磷化方法。常温磷化反应机理:当被清洗过的钢铁表面一接触到磷化液后首先发生铁溶解,如反应式(1)。在钢铁表面,处理液的pH值升高,进行化学反应,在钢铁表面析出磷酸锌膜,如反应式(2)和(3)。
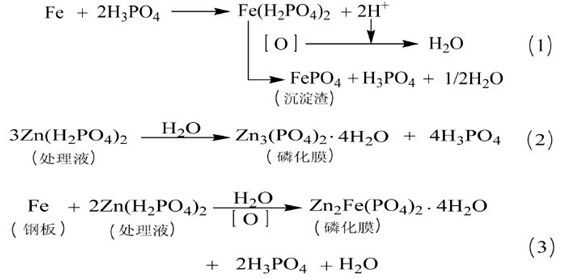
反应公式
金属基材表面磷化后,在显微镜下观察,可以看到有致密的微细结晶层覆盖在金属表面,使表面与大气隔离,因而增加了水汽渗入的阻力,加强了防腐蚀性能,同时微细的结构使表面粗糙度增大,增加与涂层间接触表面,相应地增加了底面在磷化膜上的附着力。
4.2.4铬化
铬化是最常用的一种化学转化前处理方法,铬化膜提高了金属与涂层之间的附着力,改善了涂层的防腐性能。铬化有两种形式:黄铬化和绿铬化。黄铬化池温度约25℃左右,加入硝酸调节pH值在1.8~1之间。黄铬化膜的结构为最外层是很薄的铁氰化铬和水合三氧化二铬,其下覆盖着一层很厚的水合三氧化二铬膜。
在金属与铬化膜的界面上存在少量的氧化物与氟化物。黄铬化后呈现黄色铬化层,颜色从浅黄到深金黄色,铬化膜的厚度在0.6~1.2g/m2。
绿铬化也叫磷化铬化,即使用磷酸调节pH值在1.7~1.9之间,有时可能更低一些。铬化温度通常为25~30℃。绿铬化膜的结构是大量的水合磷酸铬与少量的水合氧化铬组成较厚的膜层,氧化铬朝向金属表面。在金属与铬化膜的界面上存在少量的氧化铝与氟化物。铬化处理后呈现绿色,颜色由浅绿到深绿变化。铬化膜的厚度在0.6~1.5g/m2,颜色应尽量做到一致。
4.3热固性氟粉末涂料应用于不同金属基材表面处理方式选择
在实际应用中,不管采取那一种金属表面处理工艺,其最主要的目的有两方面,一是增强金属基材表面与涂层附着力,二是提高涂层防腐性能。为了针对不同金属基材选择出合适表面处理工艺,我们通过检测涂层附着力、冲击强度来考察表面处理工艺对涂层性能影响,通过耐丁酮擦洗来考察涂膜的交联程度。
4.3.1钢和铁基材 4.2.4铬化
铬化是最常用的一种化学转化前处理方法,铬化膜提高了金属与涂层之间的附着力,改善了涂层的防腐性能。铬化有两种形式:黄铬化和绿铬化。黄铬化池温度约25℃左右,加入硝酸调节pH值在1.8~1之间。黄铬化膜的结构为最外层是很薄的铁氰化铬和水合三氧化二铬,其下覆盖着一层很厚的水合三氧化二铬膜。
在金属与铬化膜的界面上存在少量的氧化物与氟化物。黄铬化后呈现黄色铬化层,颜色从浅黄到深金黄色,铬化膜的厚度在0.6~1.2g/m2。
绿铬化也叫磷化铬化,即使用磷酸调节pH值在1.7~1.9之间,有时可能更低一些。铬化温度通常为25~30℃。绿铬化膜的结构是大量的水合磷酸铬与少量的水合氧化铬组成较厚的膜层,氧化铬朝向金属表面。在金属与铬化膜的界面上存在少量的氧化铝与氟化物。铬化处理后呈现绿色,颜色由浅绿到深绿变化。铬化膜的厚度在0.6~1.5g/m2,颜色应尽量做到一致。
4.3热固性氟粉末涂料应用于不同金属基材表面处理方式选择
在实际应用中,不管采取那一种金属表面处理工艺,其最主要的目的有两方面,一是增强金属基材表面与涂层附着力,二是提高涂层防腐性能。为了针对不同金属基材选择出合适表面处理工艺,我们通过检测涂层附着力、冲击强度来考察表面处理工艺对涂层性能影响,通过耐丁酮擦洗来考察涂膜的交联程度。
试验选用0.8mm厚度的普通碳钢板和铁板。第一种方案,对金属基材表面脱脂—打磨除锈后直接静电喷涂烘烤成膜,检测结果发现,对于钢板和铁板,氟粉末涂料制备涂膜附着力都能达到1级,冲击强度50cm全通过。第二种方案,对两类基材采用磷化处理工艺,试验结果:涂层附着力和冲击强度都
能达到要求。另外,对经打磨除锈和磷化处理的样板喷涂氟粉末涂料后,进行了耐盐雾性能对比试验,结果发现,经过打磨处理的样板经过1000h后涂层表面开始起泡,而经磷化处理样板经过4000h后,涂层表面仍然无变化,具有很好的耐盐雾性能。表8给出铁板表面处理工艺对涂层性能影响。

铁板表面处理工艺对涂层性能影响
4.3.2镀锌钢材、锌、铝及其合金
锌铝等有色金属及其合金工件表面在涂装前需要进行表面处理,由于有色金属耐碱性差,不宜使用强碱性清洗液清洗,一般推荐使用溶剂除油、乳化除油或用磷酸钠、硅酸钠配制的弱碱性清洗液。通常采用表面化学处理在表面形成一层转化膜,提高涂膜结合力与防腐蚀性能。
由于锌和铝金属属性相似,所以我们以铝基材为例说明该类金属表面处理工艺方法选择。试验检测结果表明,如果铝板表面不进行化学处理,经过打磨后直接喷涂氟粉末涂料,涂层与铝板表面之间附着力、冲击强度都非常差。通过大量试验发现,对铝板表面进行黄铬化处理能很好地增强涂层与基材表面的附着力与冲击强度,但是铬化工艺条件和铬化膜的质量对涂层性能有很大影响。对铝板来说,如果铬化膜太厚,将大大提高防腐性能但附着力不如薄的铬化膜。如果铬化膜太薄可以产生非常好的附着力,但涂层的防腐蚀性能不如厚铬化膜,所以在实际应用时要根据工程需要做出合理的工艺选择。另外,黄铬化处理后应当在24小时内进行粉末喷涂。表9给出铝板表面不同黄铬化处理条件对涂层性能影响。表10给出铝板表面不同处理工艺对涂层性能影响。
锌铝等有色金属及其合金工件表面在涂装前需要进行表面处理,由于有色金属耐碱性差,不宜使用强碱性清洗液清洗,一般推荐使用溶剂除油、乳化除油或用磷酸钠、硅酸钠配制的弱碱性清洗液。通常采用表面化学处理在表面形成一层转化膜,提高涂膜结合力与防腐蚀性能。
由于锌和铝金属属性相似,所以我们以铝基材为例说明该类金属表面处理工艺方法选择。试验检测结果表明,如果铝板表面不进行化学处理,经过打磨后直接喷涂氟粉末涂料,涂层与铝板表面之间附着力、冲击强度都非常差。通过大量试验发现,对铝板表面进行黄铬化处理能很好地增强涂层与基材表面的附着力与冲击强度,但是铬化工艺条件和铬化膜的质量对涂层性能有很大影响。对铝板来说,如果铬化膜太厚,将大大提高防腐性能但附着力不如薄的铬化膜。如果铬化膜太薄可以产生非常好的附着力,但涂层的防腐蚀性能不如厚铬化膜,所以在实际应用时要根据工程需要做出合理的工艺选择。另外,黄铬化处理后应当在24小时内进行粉末喷涂。表9给出铝板表面不同黄铬化处理条件对涂层性能影响。表10给出铝板表面不同处理工艺对涂层性能影响。
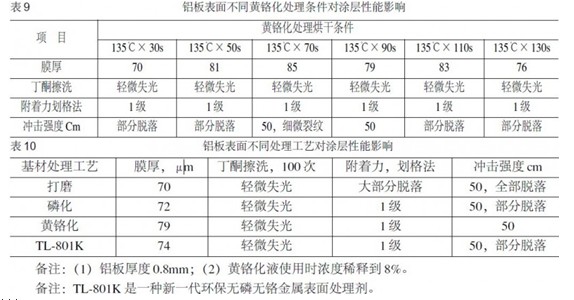
铝板表面不同黄铬化处理条件对涂层性能影响
铝板表面不同处理工艺对涂层性能影响
5结论
(1)采用溶液沉淀聚合工艺合成出具有优良热储存稳定性和优异综合性能的热固性氟粉末树脂,应用该树脂配制热固性氟粉末涂料烘烤温度、生产、施工工艺与普通粉末涂料类似。
(2)制备热固性氟粉末涂料具有优异的物理机械性能、耐酸碱、耐盐水、耐海水、耐盐雾及耐人工加速老化性能。
(3)对热固性氟粉末涂料的耐溶剂性能在实际应用过程中要有正确的认识,不能将其与全氟聚合物的耐溶剂性能相混淆。
(4)不同金属基材前处理工艺的正确选择和质量好坏,关系到热固性氟粉末涂料涂层整体使用寿命,在实际工程应用中,只有选择合适前处理工艺,保证质量,按时施工,才能发挥出热固性氟粉末涂料涂层的优异综合性能。
(1)采用溶液沉淀聚合工艺合成出具有优良热储存稳定性和优异综合性能的热固性氟粉末树脂,应用该树脂配制热固性氟粉末涂料烘烤温度、生产、施工工艺与普通粉末涂料类似。
(2)制备热固性氟粉末涂料具有优异的物理机械性能、耐酸碱、耐盐水、耐海水、耐盐雾及耐人工加速老化性能。
(3)对热固性氟粉末涂料的耐溶剂性能在实际应用过程中要有正确的认识,不能将其与全氟聚合物的耐溶剂性能相混淆。
(4)不同金属基材前处理工艺的正确选择和质量好坏,关系到热固性氟粉末涂料涂层整体使用寿命,在实际工程应用中,只有选择合适前处理工艺,保证质量,按时施工,才能发挥出热固性氟粉末涂料涂层的优异综合性能。
下一篇:研究防锈清漆在石油管道中的应用
相关文章
发布评论