涂料技术
水性环氧玻璃鳞片重防腐涂料的研制
2结果与讨论
2.1玻璃鳞片的不同表面处理工艺对于涂层性能的影响
使用表面处理剂对玻璃鳞片进行表面处理,一是保护玻璃鳞片表面不受侵蚀,二是为了提高玻璃鳞片与树脂的粘结力,使固化后的膜层形成坚实的整体膜,使用的处理剂如同在树脂与玻璃鳞片之间形成了“分子桥”,将两种性质不同的材料牢固的连接在一起,比未经处理的玻璃鳞片配制的涂料性能要高出许多[5-7]。本实验分别选用硅烷偶联剂KH550、KH560、KH570和钛酸酯偶联剂NDZ-311、NDZ-201分别利用浸润法和直接掺混法对相同用量的玻璃鳞片进行表面处理,然后配制成玻璃鳞片涂料,按照有关标准制备样板进行性能测试,对玻璃鳞片的表面处理效果进行对比。80目的玻璃鳞片经过不同的表面处理工艺处理之后制备成的涂层部分性能比较如表3所示;其相应的耐腐蚀性能比较如表4所示。由表3可以看出:与未经过任何处理的空白玻璃鳞片涂料相比,使用偶联剂处理之后的玻璃鳞片涂料,在物理机械性能上呈现出比较大的差别。利用硅烷偶联剂KH560直接掺混法处理的玻璃鳞片涂料机械性能明显提高了很多;而有的表面处理工艺处理过的玻璃鳞片涂料性能则出现了下降,说明这些表面处理工艺方法并不适用于水性环氧树脂和玻璃鳞片这一体系。在防腐蚀性能方面,大多数用偶联剂处理之后的玻璃鳞片涂料比未经任何处理的空白玻璃鳞片涂料有了较大的提高,尤其是利用硅烷偶联剂KH560直接掺混法处理玻璃鳞片效果最好,这说明硅烷偶联剂KH560直接掺混法这种表面处理工艺比较适用于这一体系。未经任何处理的空白玻璃鳞片涂料和利用硅烷偶联剂KH560直接掺混法处理之后的玻璃鳞片涂料的涂层的SEM照片分别如图1中a、b所示。从图1中的照片对比可以看出,未经任何处理的空白玻璃鳞片在树脂基体中的漂浮性相对比较差,玻璃鳞片在基体中的取向排列程度较低,鳞片之间没有能够形成比较好的搭接,造成涂层内部的结构的不均一,因此其对应的涂层的抗渗透能力必然不好,这样就造成了涂层的各种防腐蚀性能较差。
2.1玻璃鳞片的不同表面处理工艺对于涂层性能的影响
使用表面处理剂对玻璃鳞片进行表面处理,一是保护玻璃鳞片表面不受侵蚀,二是为了提高玻璃鳞片与树脂的粘结力,使固化后的膜层形成坚实的整体膜,使用的处理剂如同在树脂与玻璃鳞片之间形成了“分子桥”,将两种性质不同的材料牢固的连接在一起,比未经处理的玻璃鳞片配制的涂料性能要高出许多[5-7]。本实验分别选用硅烷偶联剂KH550、KH560、KH570和钛酸酯偶联剂NDZ-311、NDZ-201分别利用浸润法和直接掺混法对相同用量的玻璃鳞片进行表面处理,然后配制成玻璃鳞片涂料,按照有关标准制备样板进行性能测试,对玻璃鳞片的表面处理效果进行对比。80目的玻璃鳞片经过不同的表面处理工艺处理之后制备成的涂层部分性能比较如表3所示;其相应的耐腐蚀性能比较如表4所示。由表3可以看出:与未经过任何处理的空白玻璃鳞片涂料相比,使用偶联剂处理之后的玻璃鳞片涂料,在物理机械性能上呈现出比较大的差别。利用硅烷偶联剂KH560直接掺混法处理的玻璃鳞片涂料机械性能明显提高了很多;而有的表面处理工艺处理过的玻璃鳞片涂料性能则出现了下降,说明这些表面处理工艺方法并不适用于水性环氧树脂和玻璃鳞片这一体系。在防腐蚀性能方面,大多数用偶联剂处理之后的玻璃鳞片涂料比未经任何处理的空白玻璃鳞片涂料有了较大的提高,尤其是利用硅烷偶联剂KH560直接掺混法处理玻璃鳞片效果最好,这说明硅烷偶联剂KH560直接掺混法这种表面处理工艺比较适用于这一体系。未经任何处理的空白玻璃鳞片涂料和利用硅烷偶联剂KH560直接掺混法处理之后的玻璃鳞片涂料的涂层的SEM照片分别如图1中a、b所示。从图1中的照片对比可以看出,未经任何处理的空白玻璃鳞片在树脂基体中的漂浮性相对比较差,玻璃鳞片在基体中的取向排列程度较低,鳞片之间没有能够形成比较好的搭接,造成涂层内部的结构的不均一,因此其对应的涂层的抗渗透能力必然不好,这样就造成了涂层的各种防腐蚀性能较差。
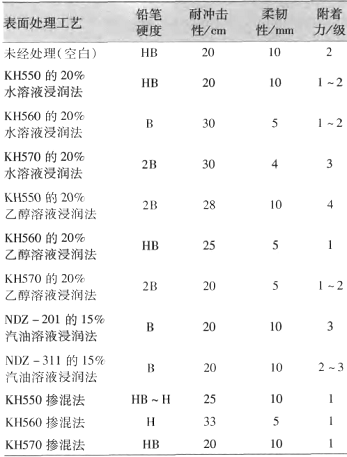
表3不同表面处理工艺处理对玻璃鳞片涂料涂层性能的影响
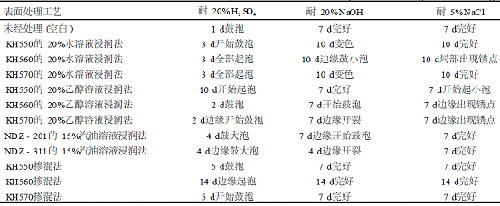
表4不同表面处理工艺处理对玻璃鳞片涂料涂层耐腐蚀性能的影响
而经过硅烷偶联剂KH560直接掺混法处理过的玻璃鳞片基本上是均匀地漂浮在基体中,玻璃鳞片在基体中的取向排列程度较好,而且鳞片之间形成了很好的搭接,因此在这种结构的涂层中,腐蚀性介质必须绕过排列紧密、均匀的玻璃鳞片才能从外表面向内部渗透,从而大幅度地提高涂料的抗渗透性,使得玻璃鳞片涂料具有很好的防腐蚀性能。另外,从图1中还明显可见,经过硅烷偶联剂KH560直接掺混法处理过的玻璃鳞片与基体(环氧树脂)结合紧密,孔洞较少,堆积密实。因此涂层的力学性能就比较好;而未处理过的玻璃鳞片与基体(环氧树脂)的结合不紧密,孔洞较多,堆积松散。所以涂层的力学性能就较差。
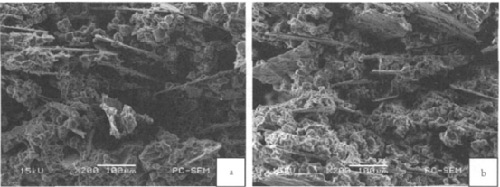
图1玻璃鳞片涂料涂层断面的SEM图
a—未经任何处理b—经硅烷偶联剂KH560直接掺混法处理
图1玻璃鳞片涂料涂层断面的SEM图
2.2玻璃鳞片的不同粒径对于涂层性能的影响
玻璃鳞片的粒径对涂层性能有着多方面的影响[8-9],一是对涂料黏度的影响,在其他条件不变的情况下,加入的玻璃鳞片的粒径越大,涂料的黏度就越高,这会影响涂料的施工性能;二是对涂层孔洞率的影响,玻璃鳞片的粒径增大,其表面积相应增大,对气泡的吸附作用也会增大,这样会使涂料在搅拌过程中产生的小气泡吸附于玻璃鳞片上不易脱离,导致气泡的残留率增加;三是对涂层抗渗透性的影响,玻璃鳞片粒径越大,纵横比就越大,这有利于鳞片在涂层中的平行排列,对介质渗透的屏蔽效果就越好。将相同用量、不同粒径的玻璃鳞片均利用硅烷偶联剂KH560直接掺混法进行表面处理,然后配制成玻璃鳞片涂料,按照有关标准制备样板进行性能测试,来对比不同粒径的玻璃鳞片对于涂层性能的影响。不同粒径的玻璃鳞片经过相同的表面处理工艺处理之后制备成的涂层部分性能比较如表5所示;其相应的耐腐蚀性能比较如表6所示。
图1玻璃鳞片涂料涂层断面的SEM图
2.2玻璃鳞片的不同粒径对于涂层性能的影响
玻璃鳞片的粒径对涂层性能有着多方面的影响[8-9],一是对涂料黏度的影响,在其他条件不变的情况下,加入的玻璃鳞片的粒径越大,涂料的黏度就越高,这会影响涂料的施工性能;二是对涂层孔洞率的影响,玻璃鳞片的粒径增大,其表面积相应增大,对气泡的吸附作用也会增大,这样会使涂料在搅拌过程中产生的小气泡吸附于玻璃鳞片上不易脱离,导致气泡的残留率增加;三是对涂层抗渗透性的影响,玻璃鳞片粒径越大,纵横比就越大,这有利于鳞片在涂层中的平行排列,对介质渗透的屏蔽效果就越好。将相同用量、不同粒径的玻璃鳞片均利用硅烷偶联剂KH560直接掺混法进行表面处理,然后配制成玻璃鳞片涂料,按照有关标准制备样板进行性能测试,来对比不同粒径的玻璃鳞片对于涂层性能的影响。不同粒径的玻璃鳞片经过相同的表面处理工艺处理之后制备成的涂层部分性能比较如表5所示;其相应的耐腐蚀性能比较如表6所示。
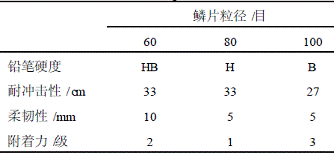
表5玻璃鳞片的粒径对玻璃鳞片涂料涂层性能的影响
对比表5和表6中的有关数据可以看出,无论是从涂层的物理机械性能还是防腐蚀性能来看,80目的玻璃鳞片涂料性能都要好于60目和100目的。原因在于60目的玻璃鳞片粒径较大,对气泡的吸附作用较大,鳞片混入涂料搅拌过程中带入的空气也较多,由此造成涂层内部气泡较多,气孔率增加,玻璃鳞片之间堆积松散,从而降低了涂层的抗渗透性;而100目的玻璃鳞片则粒径较小,鳞片的纵横比也较小,不利于鳞片在涂层中的平行排列,无序排列的比率就会增加,鳞片之间就不能形成很好的搭接,这种不利影响会抵消掉部分鳞片的屏蔽作用,所以就会降低涂层的抗渗透性。
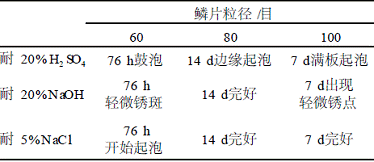
表6玻璃鳞片的粒径对玻璃鳞片涂料涂层防腐蚀性能的影响
2.3玻璃鳞片的不同用量对于涂层性能的影响
用不同用量的玻璃鳞片配制PVC从10%~35%的重防腐涂料,以此来制备样板对比涂层的各种性能,进而确定玻璃鳞片的最佳用量。不同颜填料体积浓度(PVC)对涂层性能的影响比较如表7和表8所示。
用不同用量的玻璃鳞片配制PVC从10%~35%的重防腐涂料,以此来制备样板对比涂层的各种性能,进而确定玻璃鳞片的最佳用量。不同颜填料体积浓度(PVC)对涂层性能的影响比较如表7和表8所示。
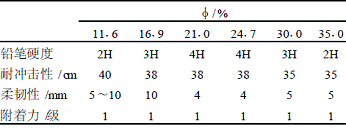
表7不同颜填料体积浓度(PVC)对涂层性能的影响
从表7中的数据可以看出,在PVC<24.7%,随着玻璃鳞片用量的增加,涂层的物理机械性能逐渐变好;在PVC为24.7%的时候,涂层的物理机械性能最佳;在超过24.7%之后,随着玻璃鳞片用量的增加,涂层的硬度有所降低,其他性能则变化不大。
下一篇:真石漆的施工工艺技术
相关文章
发布评论