涂料技术
可膨胀石墨在膨胀型钢结构防火涂料的应用
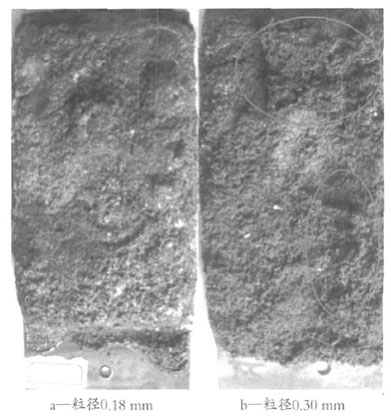
图5可膨胀石墨粒径对涂层表观的影响
其中,图5a为P5(膨胀容积180mL/g,粒径0.18mm)的照片,图5b为P6(膨胀容积200mL/g,粒径0.30mm)的照片。由图5可以看出,P5与P6的表面形态有较大的差别,P6的发泡层表面有数条深达发泡层内部的明显裂缝,同时膨胀容积较高的P6的发泡层膨胀倍率反而小于膨胀容积较低的P5。这说明粒径较大的可膨胀石墨生成的“蠕虫”状炭体纤维较粗大、发泡层的表面更疏松,在火焰冲击下容易被破坏,从而降低发泡层的隔热能力。
2.2.2可膨胀石墨的起始膨胀温度对涂料防火性能的影响
为了考察可膨胀石墨的起始膨胀温度对于涂料防火性能的影响,按照配方分别配制可膨胀石墨起始膨胀温度不同的2种涂料,编号为Q1、Q2,实验结果如表5所示。
表5可膨胀石墨的起始膨胀温度对涂料防火性能的影响
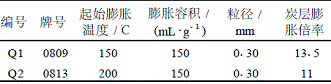
图6与图7为添加起始膨胀温度不同的可膨胀石墨的防火涂料在空气气氛中的TG与DSC图。
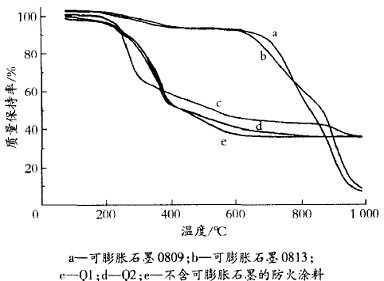
图6可膨胀石墨与防火涂料在空气气氛下的TG图
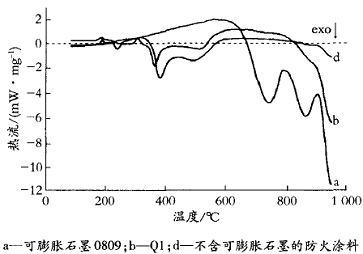
图7可膨胀石墨与防火涂料在空气气氛下的DSC图
由图6可知,可膨胀石墨热失质量发生在两个阶段[6]:第一阶段为190~620℃,由于可膨胀石墨层间的H2SO4与石墨发生氧化还原反应释放出气体,使可膨胀石墨发生不可逆膨胀。这一阶段吸收热量,最大吸热速率出现在586.3℃。第二阶段为620~1000℃,可膨胀石墨在热氧条件下被氧化为CO2,最大失质量速率在780℃,当温度达到1000℃时累积失质量达92.8%,这一阶段释放热量。可见,可膨胀石墨在190℃左右开始膨胀,在620℃的空气气氛中能形成稳定的多孔结构。与可膨胀石墨0813相比,可膨胀石墨0809热失质量的第一阶段开始较早,因此Q1(起始膨胀温度150℃)第一阶段热失质量速率及发泡层反应程度均高于Q2(起始膨胀温度200℃),并且Q1的残余质量比Q2提高了近7%,温度超过900℃后累计失质量才达到65%。这说明Q1生成的发泡层的质量更大,有利于阻隔热量向钢板的传递,具有更好的防火性能。防火涂料的热降解范围为190~600℃。其中,190~390℃是发泡层的形成阶段。190℃时聚磷酸铵开始分解产生NH3和H3PO4,H3PO4进一步聚合生成聚磷酸,与季戊四醇发生酯化反应生成多羟基磷酸盐和酯。250℃时C3H6N6开始分解出NH3使黏性体系迅速膨胀形成多孔结构,体系进一步脱水并交联成炭,固化形成发泡层。该发泡层以C和TiO2为骨架,结构多孔疏松,导热系数接近空气。这一阶段涂料组分因分解释放出大量气体而失质量。390℃以后发泡层已膨胀到数厘米厚,热量必须通过发泡层才能传递到钢结构上,温度上升非常缓慢,这一阶段是发泡层的稳定隔热阶段,其作用时间的长短决定了钢结构的耐火极限。但发泡层中的炭和其他有机物在热氧作用下会被逐渐氧化,到600℃以后残余质量保持在35%不再变化,主要成分是剩下的TiO2等无机物。结合图6及图7可以推断,Q1(起始膨胀温度150℃)的起始膨胀温度低于防火助剂的热降解温度范围下限值(190℃),会先于防火助剂的作用而进行膨胀,形成“蠕虫”状纤维炭体直达涂层内部,起到支撑及传导热量的作用,有利于促进防火助剂在涂料表面及内部的协同作用及发泡过程更加均匀、同步,从而提升发泡层的致密度与发泡倍率。而Q2(起始膨胀温度200℃)与防火涂料的热降解及发泡层的膨胀几乎同步,对改善防火涂料在受火时发泡层各部分反应程度不均匀的缺陷其效甚微。因此,起始膨胀温度为150℃的可膨胀石墨对涂料防火性能的增强优于起始膨胀温度为200℃的可膨胀石墨。
3结语
(1)可膨胀石墨受热膨胀形成“蠕虫”状纤维炭体作为骨架成分穿插于防火涂料发泡层中,在提高涂层膨胀倍率的同时使发泡层更加致密,有利于涂料防火性能的提高。但可膨胀石墨用量过大反而会破坏涂料的发泡层结构,出现开裂及脱落,对涂料防火性能产生负面影响。(2)可膨胀石墨的膨胀容积越大,形成的“蠕虫”状纤维炭体越大,支撑发泡层及传导热量的效率更高,对涂料防火性能的增强效果越明显。同时可膨胀石墨的粒径过大会降低发泡层的致密度并导致表面疏松及开裂现象。(3)起始膨胀温度较低的可膨胀石墨在受热时膨胀期较早,对防火助剂的协同作用具有较好的促进作用,对涂料防火性能的增强作用较大。(4)综合实验数据,选用膨胀倍率为180mL/g、粒径为0.18mm、起始膨胀温度为150℃,并且用量占涂料总质量3.0%的可膨胀石墨能够有效增强以硅丙乳液为基料的水性防火涂料的防火性能。
由图6可知,可膨胀石墨热失质量发生在两个阶段[6]:第一阶段为190~620℃,由于可膨胀石墨层间的H2SO4与石墨发生氧化还原反应释放出气体,使可膨胀石墨发生不可逆膨胀。这一阶段吸收热量,最大吸热速率出现在586.3℃。第二阶段为620~1000℃,可膨胀石墨在热氧条件下被氧化为CO2,最大失质量速率在780℃,当温度达到1000℃时累积失质量达92.8%,这一阶段释放热量。可见,可膨胀石墨在190℃左右开始膨胀,在620℃的空气气氛中能形成稳定的多孔结构。与可膨胀石墨0813相比,可膨胀石墨0809热失质量的第一阶段开始较早,因此Q1(起始膨胀温度150℃)第一阶段热失质量速率及发泡层反应程度均高于Q2(起始膨胀温度200℃),并且Q1的残余质量比Q2提高了近7%,温度超过900℃后累计失质量才达到65%。这说明Q1生成的发泡层的质量更大,有利于阻隔热量向钢板的传递,具有更好的防火性能。防火涂料的热降解范围为190~600℃。其中,190~390℃是发泡层的形成阶段。190℃时聚磷酸铵开始分解产生NH3和H3PO4,H3PO4进一步聚合生成聚磷酸,与季戊四醇发生酯化反应生成多羟基磷酸盐和酯。250℃时C3H6N6开始分解出NH3使黏性体系迅速膨胀形成多孔结构,体系进一步脱水并交联成炭,固化形成发泡层。该发泡层以C和TiO2为骨架,结构多孔疏松,导热系数接近空气。这一阶段涂料组分因分解释放出大量气体而失质量。390℃以后发泡层已膨胀到数厘米厚,热量必须通过发泡层才能传递到钢结构上,温度上升非常缓慢,这一阶段是发泡层的稳定隔热阶段,其作用时间的长短决定了钢结构的耐火极限。但发泡层中的炭和其他有机物在热氧作用下会被逐渐氧化,到600℃以后残余质量保持在35%不再变化,主要成分是剩下的TiO2等无机物。结合图6及图7可以推断,Q1(起始膨胀温度150℃)的起始膨胀温度低于防火助剂的热降解温度范围下限值(190℃),会先于防火助剂的作用而进行膨胀,形成“蠕虫”状纤维炭体直达涂层内部,起到支撑及传导热量的作用,有利于促进防火助剂在涂料表面及内部的协同作用及发泡过程更加均匀、同步,从而提升发泡层的致密度与发泡倍率。而Q2(起始膨胀温度200℃)与防火涂料的热降解及发泡层的膨胀几乎同步,对改善防火涂料在受火时发泡层各部分反应程度不均匀的缺陷其效甚微。因此,起始膨胀温度为150℃的可膨胀石墨对涂料防火性能的增强优于起始膨胀温度为200℃的可膨胀石墨。
3结语
(1)可膨胀石墨受热膨胀形成“蠕虫”状纤维炭体作为骨架成分穿插于防火涂料发泡层中,在提高涂层膨胀倍率的同时使发泡层更加致密,有利于涂料防火性能的提高。但可膨胀石墨用量过大反而会破坏涂料的发泡层结构,出现开裂及脱落,对涂料防火性能产生负面影响。(2)可膨胀石墨的膨胀容积越大,形成的“蠕虫”状纤维炭体越大,支撑发泡层及传导热量的效率更高,对涂料防火性能的增强效果越明显。同时可膨胀石墨的粒径过大会降低发泡层的致密度并导致表面疏松及开裂现象。(3)起始膨胀温度较低的可膨胀石墨在受热时膨胀期较早,对防火助剂的协同作用具有较好的促进作用,对涂料防火性能的增强作用较大。(4)综合实验数据,选用膨胀倍率为180mL/g、粒径为0.18mm、起始膨胀温度为150℃,并且用量占涂料总质量3.0%的可膨胀石墨能够有效增强以硅丙乳液为基料的水性防火涂料的防火性能。
相关文章
发布评论