涂料技术
可膨胀石墨在膨胀型钢结构防火涂料的应用
2结果与讨论
2.1可膨胀石墨用量对涂料防火性能的影响
为了考察可膨胀石墨对于涂料防火性能的影响,按照表2配方分别配制可膨胀石墨(牌号0807)含量不同的7种涂料,编号为F0、F1、F2、F3、F4、F5、F6,涂层厚度为2mm,养护7天后进行耐火性能测试,结果如表3所示。
表3可膨胀石墨用量对涂料防火性能的影响
2.1可膨胀石墨用量对涂料防火性能的影响
为了考察可膨胀石墨对于涂料防火性能的影响,按照表2配方分别配制可膨胀石墨(牌号0807)含量不同的7种涂料,编号为F0、F1、F2、F3、F4、F5、F6,涂层厚度为2mm,养护7天后进行耐火性能测试,结果如表3所示。
表3可膨胀石墨用量对涂料防火性能的影响
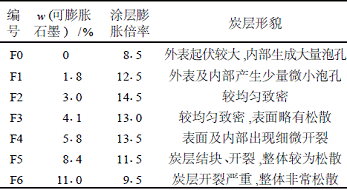
从表3可以看到,添加可膨胀石墨与否对防火涂料膨胀发泡层的性能有较大的影响,添加可膨胀石墨的防火涂料的炭层膨胀倍率与炭层强度均有较明显的增强。采用数码相机拍摄了可膨胀石墨加入前后炭质层内部形貌,结果见图2。通过对发泡层的观察可发现,未添加可膨胀石墨的防火涂料发泡层的内部存在着大量较大且不均匀泡孔(图2a)。当添加少量可膨胀石墨时,发泡层的表面不再出现突起,同时其内部也不再出现不均匀泡孔(图2b)。这表明膨胀后成纤维状的石墨形成网状结构,能够有效地在涂料表面和内部之间传导热量,导致炭层的发泡较为均匀致密。
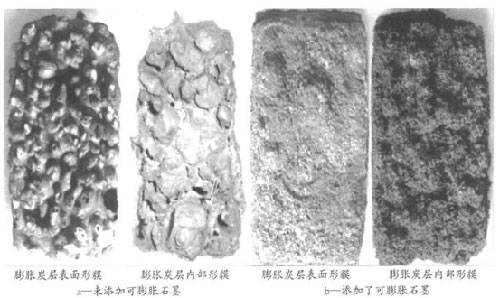
图2添加可膨胀石墨与否的涂料发泡层表面及内部形貌图
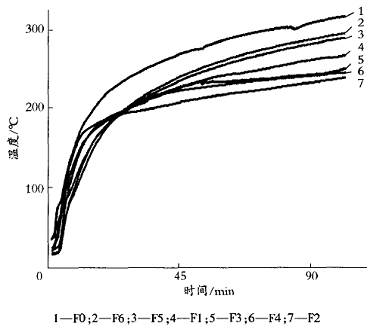
图3不同可膨胀石墨用量下涂料受火时间与样板背温曲线图
由图3所示,开始燃烧10min内7个样品的升温速率基本一致,10min后F0(未添加可膨胀石墨)的平均背温最高,其余添加了可膨胀石墨的防火涂料的背温升高速率则明显下降,并在180℃左右达到拐点温度。而未加可膨胀石墨的涂料的背温升高速率在230℃左右才出现拐点。在加入可膨胀石墨的各个配方中,F6(可膨胀石墨含量11.0%)的升温曲线平衡后的样板背温最高,同时在前25min内升温速率最慢;F2(可膨胀石墨含量3.0%)的升温曲线平衡后的样板背温最低,但在前25min内的升温速率最快。在防火涂料受火前25min内,F6(可膨胀石墨含量11.0%)的升温速率最慢,F2(可膨胀石墨含量3.0%)的升温速率最快。从实验中可观察到,可膨胀石墨在180℃左右时,“鳞片”状炭体受热时体积增大数百倍变成“蠕虫”状炭体。此物理过程是一吸热过程,而且由于“蠕虫”状炭体的密度较小,且生成的膨胀物具有较好的稳定性,覆盖在基材表面使发泡层保持有效的骨架成分,从而在发泡层中起到吸收热量、增强纤维的作用,并且使发泡层均匀受热,达到长期稳定的隔热目的。因此含有较多可膨胀石墨的试样具有较高的隔热能力。
当防火涂料继续受热至拐点温度以后,F6的升温速率加快,而F2的升温速率则减缓。分析涂层中各组分的作用可知,在到达拐点温度后,防火体系已基本上完成协同作用,形成坚固的膨胀炭层。但是随着可膨胀石墨含量的增加,可膨胀石墨进行完全膨胀所需要的时间延长,持续膨胀的可膨胀石墨会破坏已形成的发泡层,导致涂料的膨胀高度倍率降低,同时试样钢板背温上升速率加快,反而降低涂层的防火性能。从表3的数据可以看出,可膨胀石墨用量对涂层膨胀倍率的影响存在一个极大值。当可膨胀石墨含量为3.0%时涂层的膨胀倍率最大。在可膨胀石墨用量为3.0%~5.8%的范围内时,涂层的膨胀倍率比较稳定,当可膨胀石墨用量超过8.4%之后,涂层的膨胀倍率及发泡层的强度均大幅降低,并伴随发泡层开裂的现象,导致防火性能降低。
2.2可膨胀石墨性能对涂料防火性能的影响
固定膨胀石墨的加入量为3.0%,综合考察可膨胀石墨各性能参数对涂料防火性能的影响。
2.2.1可膨胀石墨的膨胀容积与粒径对涂料防火性能的影响
按照表2的配方分别配制可膨胀石墨膨胀容积与粒径不同的6种涂料,编号为P1、P2、P3、P4、P5、P6,实验结果如表4所示。由表4数据可知,除了P6(膨胀容积200mL/g)的涂层膨胀倍率略小于P5(膨胀容积180mL/g)之外,其余配方的涂层膨胀倍率均随着可膨胀石墨膨胀容积的增大明显增加。其中尤以P5的炭层膨胀倍率最高。
图4为配方P1~P6在燃烧测试中的受火时间与背温曲线图。
表4可膨胀石墨的膨胀容积与粒径对涂料防火性能的影响
由图3所示,开始燃烧10min内7个样品的升温速率基本一致,10min后F0(未添加可膨胀石墨)的平均背温最高,其余添加了可膨胀石墨的防火涂料的背温升高速率则明显下降,并在180℃左右达到拐点温度。而未加可膨胀石墨的涂料的背温升高速率在230℃左右才出现拐点。在加入可膨胀石墨的各个配方中,F6(可膨胀石墨含量11.0%)的升温曲线平衡后的样板背温最高,同时在前25min内升温速率最慢;F2(可膨胀石墨含量3.0%)的升温曲线平衡后的样板背温最低,但在前25min内的升温速率最快。在防火涂料受火前25min内,F6(可膨胀石墨含量11.0%)的升温速率最慢,F2(可膨胀石墨含量3.0%)的升温速率最快。从实验中可观察到,可膨胀石墨在180℃左右时,“鳞片”状炭体受热时体积增大数百倍变成“蠕虫”状炭体。此物理过程是一吸热过程,而且由于“蠕虫”状炭体的密度较小,且生成的膨胀物具有较好的稳定性,覆盖在基材表面使发泡层保持有效的骨架成分,从而在发泡层中起到吸收热量、增强纤维的作用,并且使发泡层均匀受热,达到长期稳定的隔热目的。因此含有较多可膨胀石墨的试样具有较高的隔热能力。
当防火涂料继续受热至拐点温度以后,F6的升温速率加快,而F2的升温速率则减缓。分析涂层中各组分的作用可知,在到达拐点温度后,防火体系已基本上完成协同作用,形成坚固的膨胀炭层。但是随着可膨胀石墨含量的增加,可膨胀石墨进行完全膨胀所需要的时间延长,持续膨胀的可膨胀石墨会破坏已形成的发泡层,导致涂料的膨胀高度倍率降低,同时试样钢板背温上升速率加快,反而降低涂层的防火性能。从表3的数据可以看出,可膨胀石墨用量对涂层膨胀倍率的影响存在一个极大值。当可膨胀石墨含量为3.0%时涂层的膨胀倍率最大。在可膨胀石墨用量为3.0%~5.8%的范围内时,涂层的膨胀倍率比较稳定,当可膨胀石墨用量超过8.4%之后,涂层的膨胀倍率及发泡层的强度均大幅降低,并伴随发泡层开裂的现象,导致防火性能降低。
2.2可膨胀石墨性能对涂料防火性能的影响
固定膨胀石墨的加入量为3.0%,综合考察可膨胀石墨各性能参数对涂料防火性能的影响。
2.2.1可膨胀石墨的膨胀容积与粒径对涂料防火性能的影响
按照表2的配方分别配制可膨胀石墨膨胀容积与粒径不同的6种涂料,编号为P1、P2、P3、P4、P5、P6,实验结果如表4所示。由表4数据可知,除了P6(膨胀容积200mL/g)的涂层膨胀倍率略小于P5(膨胀容积180mL/g)之外,其余配方的涂层膨胀倍率均随着可膨胀石墨膨胀容积的增大明显增加。其中尤以P5的炭层膨胀倍率最高。
图4为配方P1~P6在燃烧测试中的受火时间与背温曲线图。
表4可膨胀石墨的膨胀容积与粒径对涂料防火性能的影响
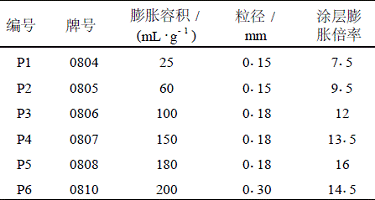
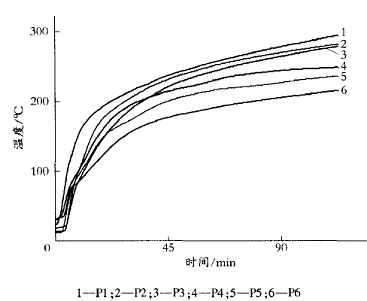
图4可膨胀石墨膨胀容积不同的涂料受火时间与样板背温曲线图
由图4可知,含有膨胀容积大的可膨胀石墨的防火涂料从受热之初到发泡完毕的整个过程中,背温曲线均低于用膨胀容积小的可膨胀石墨制备的防火涂料,这说明膨胀容积相当于可膨胀石墨的“膨胀效率”,直接影响涂层的膨胀倍率与涂料的防火性能。研究发现,在同等受热的条件下,膨胀容积越大的可膨胀石墨生成的“蠕虫”状纤维炭体也越大。较长的“蠕虫”状纤维穿插于发泡层中,起了很好的热量传导作用与支撑作用,从而使发泡层的受热更均匀、强度更高。结合表4及图4可知,膨胀倍率为180mL/g的可膨胀石墨对涂料防火性能的作用最为明显。图5为含有不同粒度的可膨胀石墨的防火涂料燃烧后的炭层局部放大照片。
由图4可知,含有膨胀容积大的可膨胀石墨的防火涂料从受热之初到发泡完毕的整个过程中,背温曲线均低于用膨胀容积小的可膨胀石墨制备的防火涂料,这说明膨胀容积相当于可膨胀石墨的“膨胀效率”,直接影响涂层的膨胀倍率与涂料的防火性能。研究发现,在同等受热的条件下,膨胀容积越大的可膨胀石墨生成的“蠕虫”状纤维炭体也越大。较长的“蠕虫”状纤维穿插于发泡层中,起了很好的热量传导作用与支撑作用,从而使发泡层的受热更均匀、强度更高。结合表4及图4可知,膨胀倍率为180mL/g的可膨胀石墨对涂料防火性能的作用最为明显。图5为含有不同粒度的可膨胀石墨的防火涂料燃烧后的炭层局部放大照片。
相关文章
发布评论